The textile is a dynamic and confusing fabric that can be used in various ways; it has the characteristics of being like silk and also being breathable. Viscose is often referred to as a man-made fiber, which is produced from natural sources, mostly wood pulp and several chemical processes that are done on it transform it into its final form. The text will analyze viscose rayon fabric in depth by exploring its attributes, manufacturing process and fashion industry applications. This article will discuss the process of making viscose as well as some special features about this fabric that make it popular for fashion designers and those who buy clothes.
How is viscose rayon made?
From the outset, the production of viscose rayon involves cellulose extraction by it from wood pulp. This cellulose is then converted into a highly viscous solution called “viscose” through treatment with an alkaline substance. Apart from that, the viscose solution is passed through a spinneret to make long fibers. Moreover, they are then stiffened via immersion in sulfuric acid bath that return cellulose back and form ultimate fibers. After rinse-drying cycle, they are now ready for spinning into yarn and weaving into fabrics resulting to a smooth shiny fabric which is known as Viscose Rayon.
What are the different types of viscose rayon?
The most important raw material for making Viscose Rayon is Cellulose. This comes mostly from renewable sources such as wood pulp. The main types of trees used for pulping include spruce, pine and beech. Other possible raw materials may include bamboo and some kinds of cotton linters as well. Wood selection can influence the characteristics and quality of the final viscose fibers, with hardwoods generally having superior pulps due to their smaller fibers.
Technical Specifications:
Cellulose Content: High-quality wood pulp typically contains at least 90-95% cellulose, which is essential for producing strong viscose fibers.
Viscous Value: Depending on the concentration of cellulose and specific production parameters this value can range between approximately 250 – 1200 mPa·s.
Dissolving Pulp Specifications: To ensure purity and performance in the end product, dissolving pulp for viscose manufacture should have a brightness level (ISO) greater than 90 percent and residual lignin content less than 0.5 percent.
These raw materials along with precise technical specifications help manufacturers achieve uniformity in quality during production of Viscouse Rayon hence making it a preferable option in textile industry.
The Production Process for Viscose Fiber
Conversion of cellulose into textile material that can be used in the production of viscose fiber goes through several important stages. These include:
Pulping: The initial stage involves breaking down wood or other sources of cellulose into pulp. This is done using chemical processes that remove lignin, producing high purity dissolving pulps. In this phase, the pulp must have a certain level of purity such as residual lignin content below 0.5% for efficient production of viscose.
Alkaline Treatment: Then, the purified pulp is reacted with sodium hydroxide to form an alkaline cellulose. This makes cellulose fibers swell and ready to dissolve later on. When treating it should be a target concentration of cellulose accepted, which may comprise about 90-95% cellulose by weight.
Viscose Solution Preparation: Alkaline cellulose is then dissolved in carbon disulfide giving rise to a thick solution called viscous solution. Its viscosity usually ranges from 250 to 1200 mPa·s depending on the concentrations and methods employed in producing them.
Filtration and Spinning: Following filtration to remove undissolved particles, the viscose solution is extruded through spinnerets resulting in continuous filaments that are hardened by being passed through a bath.
Washing and Drying: After spinning, fibers go through washing process where residual chemicals are removed followed by drying for moisture attainment at desired levels; hence, final characteristics of tensile strength and overall quality depend on its parameters.
Cutting and Finishing: In conclusion the continuous filaments are cut into staple fibers then subjected to finishing treatments to boost their performance properties before they are sold as finished goods.
Following these steps with strict adherence to technical parameters mentioned above will help manufacturers produce viscose fibers that satisfy industry requirements while maintaining consistent quality standards as may be necessary at any time.
A Comparison of Conventional Viscose and Sustainable Viscose
When it comes to conventional viscose production, there are usually great environmental consequences due to use of toxic chemicals such as carbon disulphide and deforestation in the sourcing wood pulp. On the other hand, sustainable viscose is made through much more ecological means that attempt to reduce chemical use and encourage responsible raw material procurement. Below are some key technical parameters showing the distinction:
Chemical Management: Most sustainable methods used for producing viscose often entail closed-loop processes for recycling chemicals thereby reducing harmful waste and emissions significantly. For instance, up to 80% can be generated by carbon disulfide in a single process while sustainable technologies keep this figure below 5%.
Sourcing Practices: Conventional cellulose or wood pulp used in making viscose mainly comes from unsustainable timber practices while sourcing for sustainable viscose is done from responsibly managed forests certified by bodies such as the Forest Stewardship Council (FSC).
Water Consumption: Generally sustainable methods of producing viscose consume less water than conventional ones which may use several thousands litres per tonne of viscose produced thus employing efficient water recycling techniques could aim to cut down by about 50%.
Biodegradability: Sustainable viscose is an improvement on traditional viscosity in terms of biodegradability because they include fewer non-biodegradable additives during their production hence after disposal; there is safety on environment.
However, it should be noted that these safer and more responsible practices enable sustainability of viscous not only to achieve performance standards but also capable of satisfying consumer demand for green textile solutions as well.
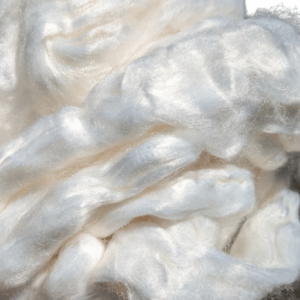
Why choose viscose as a fabric?
Viscose rayon has various categories depending on the manufacturing process and end use application:
Regular Viscose: commonly known type that is generated through traditional methods; suitable for general textiles or clothes.
High Wet Modulus (HWM) Viscose: this kind has optimized strength allowing it to be used in products like bed linens that require higher wash durability.
Cupro: a posh variation made by dissolving cellulose in copper solution, noted for its silky texture and ability to drape well.
Modal: This subclass of rayon is outstanding in terms of moisture absorption and comfortable touch, which makes it ideal for sportswear and underwear.
Lyocell: Just as viscose comes from cellulose, lyocell is also derived from this substance but using a more eco-friendly solvent-spun process that results into a bio-degradable fiber endowed with high tensile strength and comfort.
Each type of viscose rayon is unique with specific features and advantages suited to market demands and consumer preferences.
Modal and Lyocell Understanding
Both Modal and Lyocell are types of rayon often preferred because they are made from natural resources but produced by different methods that affect their characteristics and sustainability.
Modal: Modal is basically derived from fibers made of beech tree pulp which is then subjected to a similar process as viscose but using an improved way of spinning that increases its strength and durability. Usually, it has the following technical specifications:
Capillary action: Modal absorbs moisture more effectively than cotton does making it appropriate for undergarments and other tight outfits.
Luxuriousness: Its feel is usually opulent compared to that of cotton thereby being ideal for clothing such as underwear and sleepwear.
Longevity: Modal does not shrink or fade easily hence is highly suitable for clothes meant to last long in use.
Lyocell: Produced by Lenzing AG (Tencel), lyocell is manufactured in a closed loop system so that solvents used during the process can be recycled thus reducing environmental damage. Logistic includes:
Decay ability: It decomposes rapidly when exposed to natural conditions, meaning it leaves a smaller ecological footprint.
Power: It surpasses viscose, modal, in terms of tensile strength; thus best suited for denims or sportswear among others
Coziness: This material feels so soft on our bodies as if the wearer was wearing silk garments instead.
Modal and Lyocell are both considered sustainable alternatives to conventional rayon; they have unique features that target consumers who want eco-friendly fabrics but maintain high standards in performance.
How artificial silk is different from rayon fabric?
When it comes to artificial silk, it is also called silk-like fabrics or luxury synthetic materials and differs in several significant aspects from rayon. Here, however, are the main distinctions with their respective technical specifications:
Fiber Origin:
Artificial Silk: This is usually made from synthetics like polyester or nylon designed to mimic the luxurious smoothness and shine of natural silk.
Rayon: It’s a kind of semi-synthetic fiber that derives its features from naturally existing cellulose sources such as wood pulp; it therefore imitates the texture of silk but without being such origin.
Moisture Management:
Artificial Silk: Some forms of artificial silks are treated for better moisture-wicking capacities, making them suitable for use in various climates while still giving comfort.
Rayon: When wet, this material loses its comfort properties despite having pores and being breathable therefore prone to water absorption and sagging.
Durability:
Artificial Silk: In general, compared to rayon they possess more durability and resistance against abrasion allowing them to be washed and worn without significant damages occurring.
Rayon: However soft and expensive it may seem, rayon has less durability thus can easily tear or fray especially when wet.
Care Requirements:
Artificial Silk: Often needing dry cleaning or gentle washing maintenance of structure and look can be done by caring. Most synthetic silks can be machine-washed without wrinkling.
Rayon: Dry cleaning or delicate washing is required as the fabric needs gentle care so as not to lose its form and shape.
These differences highlight the unique attributes of both materials where artificial ones tend to be preferred for their ability to last longer and ease of maintenance while naturally occurring softness makes people go for rayons.
How Cellulose Fibers are used to Make Rayon
Rayon is produced from natural cellulose sources into a versatile fiber through multi-step process. Below are the main steps involved in making rayon:
Selection of Raw Material: Cellulose for this process is always got from wood pulp or cotton linters. Wood chips are normally used because they are abundant and contain high cellulose levels.
Chemical Treatment: Sodium hydroxide, also referred to as caustic soda, is used on the cellulose leading to the conversion of the latter into alkali cellulose. This transition is important because it prepares the cellulose for further processes.
Visco Solution Formation: The alkali cellulose then undergoes aging and other treatments so that it dissolves in a viscous solution. At this stage, it is mixed with carbon disulfide yielding a thick syrup-like substance referred to as viscose.
Extrusion and Regeneration: Spinnerets are extruded with viscous solutions. Filaments emerging from the spinneret pass through a coagulating bath (often containing sulfuric acid or sodium sulfate) that regenerates cellulose and solidifies fibers.
Washing and Drying: The fibers are first washed after being formed in order to remove any remaining chemicals before being dried. The drying process can affect rayon’s final texture and strength.
Technical Parameters
Cellulose Content: Quality rayon production calls for a high content of cellulose at around 90% which determines its strength and softness.
Sodium Hydroxide Concentration: The percentage of sodium hydroxide concentration lies between 10-20 %, having an impact on how effectively the alkaline converts cellulosic matter into alkali celluloses.
Spinning Conditions: During extrusion control of temperature humidity controls filament properties; by providing optimal condition better filament cohesion and durability can be achieved.
Coagulating Bath Composition : The specific chemicals used (sulfuric acid or sodium sulfate) and their concentrations are crucial to the success of the regeneration process and determine the final characteristics of the fiber.
These steps and parameters reveal how complex it is to produce rayon, an amazing process where environmentally friendly raw materials are converted into fabrics widely used today.
What is the history of viscose?
Viscose, also called rayon, originated from France in the late 19th century as a synthetic alternative to silk. The French chemist Hilaire de Chardonnet invented the process for producing viscose which was patented in 1884. By dissolving cellulose made from wood pulp and reconstituting it through a chemical method, viscose material became popular because it imitated luxurious silk but at less cost. In the course of the twentieth century, production of viscose expanded quickly leading to wide use in clothing, home furnishings and industrial textiles. However, even though sustainability poses problems for this industry today, there are ongoing efforts towards enhancing the environmental impact of making viscose by employing eco-friendly techniques.
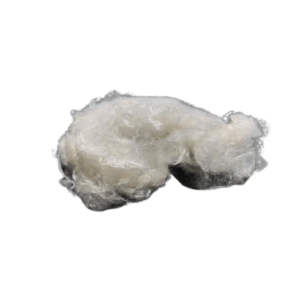
How did man-made silk originally come about?
Man-made silk came into being as a response to the need for cheaper alternatives. This innovation began in the 19th century when Hilaire de Chardonnet, a Frenchman, patented the process of making viscose. This involved immersion of cellulose into a chemical solution, commonly derived from pulp made from timber and then reconstituting it to fibers that can be woven.
Technical Parameters Justification:
Cellulose Source: Viscose rayon is mainly derived from renewable sources like wood pulp hence it could be an environmentally friendly alternative compared to petroleum-based fibres.
Production Process: The versatility of design and texture is provided by the steps composing dissolving cellulose, spinning fibres and weaving them used in making viscose.
Softness and Drapability: For garments that require ease of movement, viscose rayon is soft in touch and drapes well..
Eventually, other than just clothing items, this has found its way into applications such as home textiles and industrial materials where it has become synonymous with luxury at low cost. However, current practices are increasingly geared towards reducing environmental impacts associated with its production.
Viscose Production Technology has undergone major advancements.
Recent developments in the field of viscose production technology have been geared towards ensuring sustainability and efficiency, in response to environmental concerns and consumer preferences.
Closed-loop Production Process: Many companies have embraced a closed loop system which has led to significant decrease in wastewater as well as emissions from by-products. In this process, chemicals used for dissolving cellulose are recycled resulting into reduced impacts on the environment and overall improvement of its sustainability.
Technical Parameters Justification: This method is resource-saving and minimizes pollution so it complies with global sustainable development goals.
Innovative Cellulose Sources: The studies are focused on alternative cellulose sources such as agricultural residues and non-wood fibers that can diversify supply chains and reduce reliance on traditional wood pulp.
Technical Parameters Justification: Combining diverse sources will enhance resource sustainability thereby keeping viscose eco-friendly.
Advanced Fiber Spinning Techniques: The progress of modern spinning technologies like wet spinning or dry-jet-wet spinning has improved the strength as well as quality of fibers. These processes enable better control over fiber properties giving an opportunity for higher performance at different finishing stages.
Technical Parameters Justification: The increased strength and quality of fibers contributes to longer textile life time making clothes made of viscose more attractive to buyers.
Overall, these advances seek not only to improve the quality and sustainability of viscose rayon but also deal with increasing consumer demands for responsible manufacturing practices within the textile industry.
Is viscose environmentally friendly?
Viscose can be recognized as environmentally friendly if sustainably produced. The use of other sources of cellulose, less chemical use during processing, and progress in recycling techniques considerably reduce its ecological impact. But still, traditional ways to produce this material may lead to deforestation and pollution if not properly controlled. Hence, the environmental implications of viscose are mainly influenced by how the cellulose is sourced and the manufacturing practices are done. In addition to that, embracing sustainability in terms of responsible forestry and closed loop systems will enhance its eco-friendliness positioning it well as a potential alternative within the textile industry itself.
The Environmental Effect of Viscose Manufacturing
Production of viscose results in various ecological implications; most notably, the usage of wood pulp and chemicals. The following are some key environmental impacts observed in different researches:
Deforestation: Conventional viscose production often involves sourcing wood from old forests which leads to loss of habitats and reduction of biodiversity. It is necessary to find sources that are sustainable.
Water Pollution: Chemical processes used in making viscose can release poisonous substances into water systems. Wastewater issues can be minimized and chemical discharge may decrease when closed-loop systems are implemented.
Water Usage: Viscose industry utilizes considerable amounts of water thereby overwhelming local potable resources especially in already water-scarce regions. Adequate water management plans should be developed to address this concern.
Carbon Emissions: Depending on the production energy sources employed, this manufacturing process can result in greenhouse gas emissions. This carbon footprint can be significantly reduced by using renewable energy sources instead.
Technical Parameters Justifications:
Cellulose Sourcing: Use sustainable harvested materials for conserving land as well as biosphere diversity that mitigates deforestation concerns.
Chemical Reductions: Innovations reducing hazardous chemical use mitigate environmental degradation while improving air and water quality.
Waste Management: Closed loop production effectively recycle solvents thereby reducing water pollution hence greater sustainability of the process itself.
Energy Source: Reducing carbon emissions through adoption of renewable energy contributes towards a more environmentally friendly production environment.
In conclusion, although the impact of visiting on environment is huge, adopting sustainable methods and new inventions may eventually make visiting an alternative option for textile manufacturing with less harm to nature.
Viscose Production with Eco-friendly Alternatives
There have been several other eco-friendly alternatives that are gaining popularity in viscose production with respect to curbing environmental impacts while maintaining quality. Here are the three main approaches that were investigated, their technical details and rationales:
Lyocell (Tencel):
Sourcing of Cellulose: Lyocell is made from sustainable eucalyptus trees which grow very fast and require little water and chemicals.
Chemical Reduction: Non-toxic solvents are used in an enclosed system during the manufacturing process so as to enable any emissions or waste to be reused or recycled.
Justification: This would help workers decrease exposure to toxic chemicals and mitigate environmental pollution.
Recycled Viscose:
Sourcing of Cellulose: It uses post-consumer waste such as old fabrics and paper thus ensuring sustainable supply chain of raw materials.
Waste Management: Reusing existing materials through recycling ensures resource conservation, thereby reducing need for virgin cellulose.
Justification: This would reduce the amount of waste going into landfills, while also cutting down on carbon footprint due to extraction of raw materials.
Modal:
Sourcing of Cellulose: Modal is manufactured from pulp derived from beech trees which come from well-managed forests sustainably obtained.
Water Usage: The manufacture of Modal can be more efficient in terms of water usage compared to conventional viscose since trees do not require much water for growth.
Justification: This sourcing is environmentally friendly and its manufacturing practices are efficient both contributing to biodiversity conservation as well as minimizing environmental footprints.
Therefore, by using these eco-friendly alternatives it will be possible for a substantial transformation regarding sustainability within the viscose production, addressing many critical issues relating traditional ways.
FQA
Q: What materials are used to make viscose fiber?
A: Viscose fiber is mainly produced from cellulose, primarily sourced from wood or bamboo. These natural substances are chemically treated in a process that produces the semi-synthetic fiber called viscose.
Q: How does conventional viscose differ from sustainable viscose?
A: Conventional viscose is made using normal chemical processes that could be detrimental to the environment while on the other hand, sustainable viscose is manufactured with less harmful chemicals and eco-friendly practices to minimize environmental footprint.
Q: Is it breathable and comfortable?
A: Yes, this fabric is famous for its breathability and high comfort levels. Its cellulose fibers absorb moisture leading to softness and coolness against skin making it ideal for all things soft and warm.
Q: How does it compare to others like modal and lyocell?
A: Viscose, modal, lyocell are all different types of rayon but they vary in terms of production processes as well as properties. Modal and lyocell have higher eco-friendliness rating compared to standard viscose; more so, they are stronger. Concerning texture modal has been noted for its softness whilst lyocell has earned accolades due to being durable and sustainable.
Q: Is it synthetic or natural material?
A: Semi- synthetic fibers such as Viscose result from chemically modifying organic fibers (from plants). It combines features of cotton (a natural fiber) with those of artificial ones like polyester.
Q: Can you use it as a silk replacement?
A: Frequently people go for viscous silk instead because of smoothness in texture plus excellent drape it possesses. In textile world this asset has given rise to epithet “fake silk”.
Q: What are some of the environmental concerns associated with producing this substance?
A: The process involves utilization of hazardous chemical reagents like sodium hydroxide and carbon disulfide which are not only harmful to the environment but also pose health risks. Nonetheless, efforts to create sustainable, ecofriendly modes of production continue.
Q: Why is viscose called a versatile fabric?
A: Viscose has been described as a versatile material due to its use in making clothes, furniture and other textile products meant for heavy usage. It is very absorbent, soft textured and can be blended with other fibers hence suitable for wide range applications.