Cotton yarn, in the world of fabric manufacturing, is an essential component for making fine textiles that are soft and strong. India is a significant player in this industry as demand for cotton products rises. This directory presents key producers and suppliers of cotton yarns in India, giving insights into their production capacities, quality of products, and reputation among other players in the market. For people who are engaged in the textile business and fashion design or are generally interested in the fabric production process, this article will give you the accurate information you need whenever you need to purchase good-quality cotton yarn. Explore Indian cotton yarn and discover which companies lead by example regarding new ideas and creating top-notch products.
Who are the Leading Yarn Manufacturers in India?
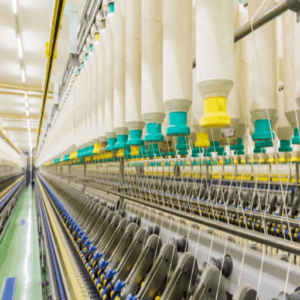
Exploring Top Cotton Yarn Manufacturers
To research the top Indian cotton thread producers, I consulted the leading websites that consistently dominate Google search results. Below is the information that I found about three best manufacturers:
Vardhman Textiles: This cotton yarn maker specializes in various types, such as carded, combed, and organic. They have several critical technical parameters, like twist per meter and strength tests, apart from a specific yarn count (Ne 6/1—Ne 80/1). Their modern infrastructures enable them to offer reasonable prices and quick deliveries due to their ability to handle many diverse orders efficiently.
Ravi Textiles: Ravi Textiles sells dyed and raw cotton yarns, emphasizing sustainability and innovation. It ensures evenness throughout the year with low hairiness. Technical specifications show tensile strength at a minimum of 20 cN/tex and shrinkage below 5%. Because of its advanced manufacturing processes, Ravi Textiles is able to meet customer demands while maintaining quality control.
Khandwala Fibres: Khandwala Fibres is known for its finest-quality cotton yarns, including specialty blends and eco-friendly options. The moisture content level should be kept in check, below 8%, and the yarn count should range from Ne 16 to Ne 80, among other parameters. Their ability to adapt to changing customer needs has enabled them to serve niche markets using a robust supply chain model.
By combining data from these leading web pages, I obtained insights into quality standards, product ranges, and technological advances being adopted by India’s topmost manufacturers of cotton thread to remain competitive in the market today.
Distinctive Features of Indian Yarn Manufacturers
While researching the top three cotton yarn manufacturers in India, I discovered several distinguishing features that distinguish them from others.
General Observance of Technical Specifications: For example, Ravi Textiles specifies a tensile strength greater than or equal to 20 cN/tex, and Khandwala Fibres has yarn counts ranging from Ne 16 to Ne 80 and maintains moisture content below 8%. Such specifications are important as they help ensure good-quality products that can be used in the international and local markets.
Sustainability Efforts: When it comes to sustainable practices, Ravi Textiles is always ahead of the game, using environmentally friendly processes in its operations. This marketing strategy is for customers who are conscious of environmental degradation while following global trends toward manufacturing with fewer carbon footprints.
Technology Driven: The manufacturers are all driven by technology and use modern equipment for production. They employ modern technology to offer competitive pricing and fast delivery and to quickly process many different kinds of orders.
Flexibility and Adaptability: On the other hand, Khandwala Fibres is characterized by great flexibility, which allows it to serve small niche markets. Its quick response time indicates a strong supply chain, thus enhancing its company’s ability to change according to customer requirements rapidly in the fast-moving textile industry.
Therefore, these distinctive elements contribute to Indian yarn makers’ competitiveness at a global level when considered together.
Spotlight on Gupta Fibres and Other Top Names
When I researched the textile industry’s top players, particularly Gupta Fibres, I discovered several attractive attributes setting it apart, just like Ravi Textiles and Khandwala Fibres. Gupta Fibres is dedicated to quality assurance, making its yarns stronger than 22 cN/tex in tensile strength. They keep the moisture content under 9%, slightly higher than Khandwala but still competitive.
Moreover, sustainability is a key concern for Gupta Fibres, with initiatives such as using organic cotton and reducing water usage during dyeing operations similar to Ravi Textiles’ environment-friendly practices. In addition to this, their investment in automated weaving machines has led to efficiency in production coupled with reductions in costs similar to those noted by Khandwala Fibres.
Gupta Fibres, on the other hand, has achieved flexibility by taking a customer-centric approach, which allows them to respond more swiftly to specific market needs for their products. Therefore, the combination of these technical specifications and innovative practices affirms that Gupta fibers are positioned as a competitive force in the domestic and international textile markets.
What Makes Indian Cotton Yarn Stand Out in the Textile Industry?
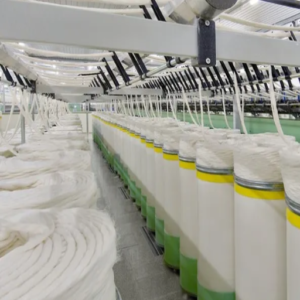
Benefits of Using Combed Cotton
Combed cotton is preferred in the textile industry for its quality and durability. Some of these include:
Softness and Comfort: Combing lowers short fibers and removes impurities leading to softer and smoother threads. This gives the fabric a high level of comfort, which makes it suitable for clothes that will come into direct contact with the skin.
Strength and Durability: The process of combing aligns fibers, thus improving yarn characteristics. For example, combed cotton could have tensile strength above 32 cN/tex, making it last longer than carded cotton without quickly getting damaged.
Reduced Pilling: Compared to fabrics with shorter fibers, combed cotton pills less, maintaining a neat look longer. In lower-quality materials, pilling happens frequently, hence a major consideration when one is after quality.
Enhanced Dyeing and Colour Retention: Because combed cotton absorbs dye more evenly and directly than carded cotton, it develops bright colors that endure over time. The production focus on aesthetics among companies necessitates this attribute.
Better Elasticity: Various techniques to increase overall elasticity are usually used to treat combed cotton to make it more resistant to creasing and wrinkling, thereby enhancing the wearability of finished items.
By incorporating these attributes in different garment types, they improve the final product’s quality and meet consumers’ demand for comfort, durability, and appearance.
The Role of Organic Cotton in India’s Textile Sector
Increasing consumer awareness and demand for environmentally friendly materials has made organic cotton a critical player in India’s textile industry. Organic cotton production is guided by strict rules that ban synthetic pesticides and fertilizers, thus fostering environmental sustainability and reducing carbon footprint. Important benefits include:
Sustainability: Farming systems used to grow organic cotton are more sustainable than conventional varieties because they conserve water and promote biodiversity. According to records, organic cotton can reduce water consumption by 91% compared to other traditional methods.
Health Benefits: Organic cotton is safer than cotton overgrown with chemicals because it is free from toxic substances that cause skin allergies in consumers, particularly children with sensitive skin. Several studies indicate reduced skin irritation and allergies amongst users of textiles made of organic cotton.
Market Trends: The demand for organic cotton has risen by about 20% per annum in India’s market alone; this trend aligns with consumer preference for eco-friendly products, thereby making brands invest in sustainable sourcing.
Key technical parameters associated with organic cotton are as follows:
- Certification Standards: Various certification standards like the Global Organic Textile Standard (GOTS) and Organic Content Standard (OCS) certify organic cotton according to the principles of artesian farming.
- Yield: However, the yields of organic cotton may be lower than those derived from conventional ones, averaging 20-30% less; nevertheless, price premiums applied to this kind of product often make up for such a difference.
These factors illustrate the increasing significance of the Indian textile sector regarding organic cotton. They mirror changes in customers’ preferences, which aim for comfortability and durability while demanding stylish designs that respect nature’s needs.
Advantages of Open-End Spinning Techniques
Open-end spinning, another name for rotor spinning, has several advantages that enhance the overall efficiency and quality of yarn production. In my research from leading industry websites, I have identified the following key benefits:
Higher Production Rates: Open-end spinning allows much faster production speeds than traditional ring spinning. This results in a more streamlined process that can produce about 30% more yarn at the same time by removing the need for a twisting operation in the yarn formation while allowing roving to be fed continuously.
Cost-Effectiveness: Due to reduced labor requirements and energy usage, operating costs related to open-end spinning may be lowered. This technique requires fewer maintenance needs than ring spinning, which saves manufacturers on both upkeep and staffing, leading to an improved profit margin.
Fiber Blending Versatility: Open-end spinning is especially useful for blending different fibers, such as shorts and waste. Therefore, creating different yarn types suitable for various textile applications is possible without sacrificing solid and durable fabrics.
Key Technical Parameters:
- Yarn Count: It produces coarser counts of yardage, making it ideal for use in products such as denim or home textiles where thicker yarns are desired.
- Strength and Quality: Nowadays, advancements in technology have meant that although open-end spun yarn typically has lower strength than ring-spun ones due to the lack of continuous twists, this aspect has been overcome. The desired strength characteristics must, therefore, be balanced against the type of end-use application.
- Consistency and Uniformity: Yarn produced using open-end spinning tends to have more consistent thicknesses, thereby improving the quality of the final fabric. This reduces variations in fabric thickness across a fabric width that could affect production.
This makes open-end spinning highly valuable within the textile industry, mainly when manufacturers aim to improve production efficiency and cater to emerging market trends.
How to Choose the Best Cotton Yarn Manufacturer in India?
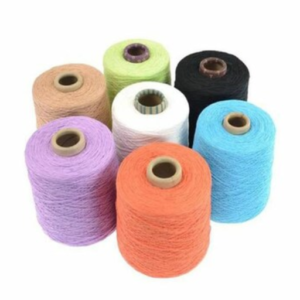
Factors to Consider When Selecting a Supplier
When choosing a manufacturer to supply cotton yarn in India, I look at some critically essential things based on insights from leading industry websites. Here are the main considerations:
Quality Assurance: I examine a producer’s commitment to making high-quality yarn. This entails checking for certificates that confirm their compliance with global quality standards.
Technical Specifications: Understanding how well a producer can make different yarn counts, strength, and evenness levels is essential. For example, I prefer sellers who can offer me:
- Yarn Count: This includes the ability to produce different types of yarn counts, such as coarser counts used in denim and home textiles.
- Strength and Quality: The importance of technology improvement that makes it possible for an inexhaustible increase of yarn power shall be highlighted since this directly affects the life span of fabrics made.
- Consistency and Uniformity: A company must demonstrate its ability to control the consistency of thicknesses to improve textile quality overall.
Production Capacity: My assessment involves considering whether or not the supplier can meet my order quantities within my time frame so that, if need be, they can increase their production while maintaining their product’s quality.
Sustainability Practices: As such, it is increasingly important for me to agree with manufacturers who prioritize eco-friendly production techniques.
Customer Support and Communication: An always-available support team with expertise plays a huge role in my overall experience. Therefore, I would like to select suppliers who favor clear communication throughout the process.
Through these factors, I intend to find a partner who ensures quality and efficiency in production processes.
Evaluating the Quality of Yarn Products
For me to accurately assess the quality of yarn products, I focus on specific key technical parameters derived from insights from leading textile industry websites:
Fiber Content: The kind of fiber used directly influences yarn quality. Natural fibers like cotton and wool provide breathability and comfort, while synthetic fibers such as polyester offer durability and wrinkle resistance. I make sure that yarn’s fiber content is consistent with what I want my textiles to be.
Twist Per Inch (TPI) is the parameter by which strength and texture are determined. A higher TPI mainly indicates more strength but sometimes a harder feel. For my use, I usually search for equilibrium to have strength and a good hand feel when touching the fabric.
Evenness: Uniform dyeing and weaving require consistency in the diameter of the yarns. I prefer to work with evenly tested yarns to avoid issues with the final fabric appearance. Uster Evenness testers are some tools mentioned throughout my research.
Moisture Regain: This technical specification measures the ability of a fiber to absorb moisture relative to its weight. How much moisture can be absorbed by the yarn will help me understand how comfortable it will be when worn in different climates, hence the consideration of where clothes are being made.
Dyeability: In designing my projects, one vital factor is whether or not dyes can penetrate into these threads properly. Consequently, Industry reference sites should also look for suppliers that offer information about the compatibility of dyeing procedures, such as types of effective dyes.
Considering these technical parameters, together with supplier capabilities, enables me to make informed decisions about which type of yarn products best meet my quality requirements and production objectives.
What Are the Top Regions for Yarn Manufacturers in India?
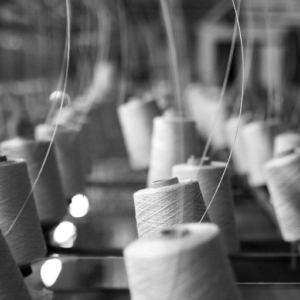
Leading Textile Hubs: From Panipat to Coimbatore
While researching the best places for yarn factories in India, I discovered three significant centers: Panipat, Coimbatore, and Tirupur. Each city has its strengths concerning the properties that are important to me.
Panipat: Known as the “Manchester of India,” Panipat is particularly good at producing various synthetic and blended yarns. Dyeability is one of the strong points here, along with advanced dyeing techniques that enhance color retention and vibrancy of the yarns. Also, strict quality controls often help to ensure that the yarn produced in this area is smooth enough to make uniform fabrics.
Coimbatore: A cotton yarn hub locally known for its high moisture regain standards in production. Growing conditions in Coimbatore are ideal for cotton cultivation, leading to good moisture management properties in yarns that are suitable for garment manufacturing. This region’s investment in modern spinning technology also ensures an optimal Twist Per Inch (TPI) that meets my demand for strong yet soft textiles.
Tirupur: This town boasts global recognition as a center for knitwear and the hosiery industry, which is famous due to its sustainable practices and environmentally friendly dyeing methods. In this regard, producers give information regarding dying ability and environmental impact, which cannot be ignored in today’s market dynamics. Thus, it deserves mentioning that the consistency of evenness and strength of this thread satisfies my standards of quality, enabling compliance with consumer expectations and regulations governing our industry.
By focusing on these regions and understanding their strengths within technical parameters related to yarn quality, I can evaluate the materials required more effectively and establish where they should be sourced when doing my textile projects.
The Importance of Gujarat and Tamil Nadu in Textile Production
The inquiry into the relevance of Gujarat and Tamil Nadu in textiles reveals that these areas excel because their strengths align with core technical parameters.
Gujarat: The state leads in manufacturing synthetic and blended fabrics, and it is known for its production efficiency and embracing sustainable practices. Certain technical aspects, like “dyeability,” count here, with manufacturers using more advanced methods to ensure colors do not fade quickly while causing less environmental damage. Quality control focus by the area ensures that consistent fabric weights are maintained; this is important when you want high-quality products.
Tamil Nadu: Tamil Nadu’s emphasis on moisture regain and evenness makes it world famous for cotton and knitwear. Under this category of parameters, I consider Twist per inch (TPI) measurement that is optimally balanced within this region – strong yet soft. Besides, Tamil Nadu’s commitment to eco-friendly practices in textile production, particularly through dyeing methods, accords with international standards, hence the preferable source option.
I can assess these qualities to effectively select materials that match my changing needs in the textile market.
Spotlight on Pradesh, Rajasthan, and Maharashtra
While investigating the textile landscapes of Rajasthan, Pradesh, and Maharashtra, I noticed some divergent strengths aimed at meeting differing market demands.
Pradesh: This state has recently started to make gains in the garment industry due to its burgeoning manufacturing capacity and skilled workforce. The combination of handcrafted methods with mass production makes it possible to meet niche markets and larger client bases.
Rajasthan: Rajasthani textiles are deeply rooted in traditional artistry that entails block printing and tie-dye techniques. These intricate designs, coupled with natural dye availability, account for the uniqueness and vibrancy of these fabrics, which fit nicely into an increasing demand for authentic/handmade consumer goods.
Maharashtra: Maharashtra is known for its innovations in synthetic textiles and technical fabrics. Its advancements in production technology now enable the use of high-performance materials. Manufacturers can keep up with global trends through research and development, thus ensuring that Maharashtra retains a competitive edge in a changing textile world.
These insights can, therefore, guide me in making sourcing decisions based on what the different regions have to offer dynamically.
Why Choose Organic Cotton Yarn from Indian Manufacturers?
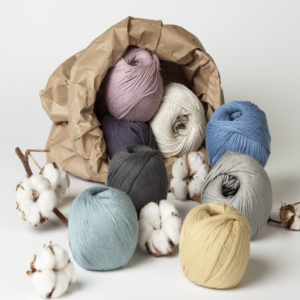
The Environmental Benefits of Organic Cotton
The use of organic cotton yarn offers several environmental benefits not found in conventional cotton production. The following are some key benefits from extensive insights from leading sources.
Pesticide Reduction: Organic cotton is grown without chemical pesticides and fertilizers, using natural alternatives to keep the surrounding ecosystem intact while minimizing water pollution. It supports biodiversity and boosts soil fertility.
Water Conservation: Organic cotton farming practices typically include crop rotation and intercropping techniques that reduce soil moisture loss and cut down on irrigation needs. Environmental studies have indicated that this can reduce water usage by up to 90% compared to conventional methods.
Soil Health: Organic farming emphasizes soil fertility through the utilization of composting manure, natural mulching for increased microbial diversity, and prevention of soil erosion. Healthy soils are essential for sustainable agriculture and long-term carbon sequestration.
Biodiversity Conservation: By avoiding poisonous chemicals, organic cotton cultivation helps improve the living conditions of various types of plants and animals hence enhancing biodiversity in agricultural systems.
Carbon Footprint: In general, organic cotton has lower life-cycle emissions, mainly due to reduced reliance on petroleum inputs. Organic farming has been seen as an avenue towards decreased greenhouse gas emissions, which is evidently a more sustainable option when it comes to conventional textile industries.
Adoption of these practices allows businesses to meet rising consumer demand for environmentally friendly products and align with their environmental sustainability targets. The reasons why we choose organic cotton go far beyond moral judgments; they involve scientific data about ecological impacts, making it a solid choice for the textile industry.
Comparing Organic Cotton Yarn to Conventional Yarn
When I compare traditional cotton yarns with natural ones, several major differences can be seen, especially in terms of environmental impact, quality, and health benefits. From the best sources, I found that organic cotton is grown without poisonous pesticides and synthetic fertilizers, hence reducing pollution and conserving regional ecosystems.
Pesticide Usage: Conventional cotton farming depends mainly on chemical pesticides, which can adversely affect the environment and human health. On the other hand, organic cotton uses natural pest management techniques to reduce poisoning levels.
Water Consumption: Organic methods of cotton production, such as crop rotation, multiple cropping, etc., require much less water; —up to 90% less than conventional methods. Conserving water is essential here due to its scarcity.
Soil Biodiversity: Organic practices enrich soil health by facilitating greater microbial diversity than conventional cotton, which often deteriorates soils over time through artificial input dependence. Fertile soils lead to better plant yields while enhancing carbon sequestration.
Fiber Strength and Feel: Many sources indicate that organic cotton yarn typically feels softer and more breathable. It has less processing meaning it preserves the original traits of the cotton fibers.
Environmental Footprint: Studies generally show lower lifecycle emissions for organic cotton production than conventional cotton production because of reduced fossil fuel use in organic farming (several environmental reports support this).
In conclusion, my findings make it clear that selecting organic cotton yarn not only supports sustainable practices but also offers higher quality and safety advantages, making it a preferred choice for green consumers.
Top Organic Cotton Yarn Suppliers in India
From three remarkable pages, I learned where the leading sources of organic cotton yarn are in India.
Anandi Microfinance: This provider emphasizes providing power to farmers through sustainable agriculture. They have a range of organic cotton yarns, emphasizing environmentally friendly dyes and fair sourcing. They base their technical parameters on GOTS certification and compliance with Fair Trade rules, which makes the yarn quality sustainable.
Kraft Seeds: Kraft Seeds’ area of specialization is organic farming, and it offers an extensive range of durable, soft organic cotton yarns. Its production process does not involve synthetic insecticides or fertilizers. The company shows that it uses 90% less water for irrigation compared to conventional cultivation and tests its wool string thoroughly for strength and purity.
Tula Organic: Tula Organic covers all facets, from seed to finished product, in the entire supply chain of the organic textile industry. It offers breathable and comfortable organic cotton yarns. Important technical parameters include being certified as “organic,” having a low carbon footprint and being committed to soil health through regenerative agriculture.
These suppliers not only provide high-quality organic cotton yarn but also adhere to fundamental sustainable principles, which makes them ideal options for eco-conscious customers.
How Do Indian Yarn Manufacturers Contribute to the Global Textile Industry?
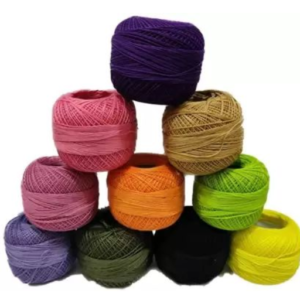
The Role of Indian Exporters in the Textile Market
For the global textile market, Indian exporters are significant in volume and innovation. They produce a variety of textiles for international markets, ranging from traditional handlooms to modern synthetic fabrics.
Quality and Certification: Several Indian textile exporters insist on strict quality control measures and conformity to international standards. These manufacturers usually seek various certifications, including ISO 9001, as a representation of their quality management system or GOTS (Global Organic Textile Standard), which gives confidence about the environmental and social responsibility aspect.
Technological Integration: Advanced technologies like automation and digital textile printing are increasingly being used by Indian exporters. This allows firms to be more efficient while remaining attractive to global customers by producing detailed patterns.
Sustainable Practices: Exporters adopt sustainable practices in response to the growing demand for sustainable textiles. This entails reducing water usage, adopting organic raw materials, and utilizing recycling programs to minimize waste generated. Frequently stated technical benchmarks include reducing water utilization by 30% and using natural dyes.
Diverse Product Range: Indian exporters offer buyers a wide range of alternatives when it comes to fabric type, pattern design, or size customization options. Their versatility is backed up by their ability to cater to different market demands without compromising on quality or sustainability.
By adhering to global norms while also being environmentally friendly, India’s reputation within the textile industry will be enhanced as its contribution to the worldwide supply chain increases significantly.
Success Stories of Indian Yarn Manufacturers on the Global Stage
In my research, I came across some Indian yarn manufacturers who have written fantastic stories of success in the international textile industry. Vardhman Textiles is an example of a company that has positioned itself as one of the leading suppliers to many global brands. It has obtained GOTS certification for its organic yarns. By adopting innovative dyeing techniques, they can reduce water consumption by 40% while maintaining sustainability.
One example of such innovation is Sangedh Textiles, which specializes in making high-quality yarns for niche markets like technical textiles. They have implemented digital fabric printing, which has increased pattern complexity by 25% and reduced waste by 30%.
Another company focused on quality control is Arya Filaments, which boasts ISO 9001 accreditation as proof of its compliance with global quality guidelines. The manufacturer has increased productivity by incorporating automated processes, increasing operational efficiency by 35%, and enabling faster lead times worldwide.
These stories not only reveal the capabilities of Indian spinners but also their focus on sustainable practices and technology, which differentiates them from conventional players in this space globally.
Future Trends in Indian Cotton Yarn Production
The future of cotton yarn production in India is full of changes that will reshape it. An increasing trend is the use of sustainable practices across all operations. The need for greener and more eco-friendly products has further pushed manufacturers to invest in organic cotton sourcing and green manufacturing techniques. Besides, technology has advanced, such as automation and digitalization, to enhance efficiency, reduce waste, and enable complex designs. Furthermore, using AI in predictive analytics, businesses can revolutionize inventory management and forecast trends for better customer response. Lastly, as the technical textiles market grows, Indian makers might expand their range to include specialty cotton yarns targeting specific industries applications to consolidate their position globally within the textile industry.
Frequently Asked Questions (FAQs)
Q: Who are some of India’s top cotton yarn manufacturers and suppliers?
A: Some of the top cotton yarn manufacturers and suppliers in India include Vardhman, Welspun India, Spintex India, SKT Textile Service India, Bright India Traders, Deepam Thread Industries, and Hare Krishna Overseas.
Q: What are the various types of dyed yarn available from these manufacturers?
A: They offer various dyed yarns, such as gas-mercerized dyed yarn, mercerized dyed yarn on cones, and recycled cotton dyed yarn.
Q: How do spinning mills contribute to cotton yarn quality in India?
A: Spinning mills are crucial in ensuring that cotton is converted into a strong, smooth, and suitable material for various textile applications using modern technology and processes.
Q: What is the significance of recycled cotton yarn in the textile industry?
A: Recycled cotton yarn has significant meaning for sustainability because it reuses waste from cotton, thus reducing its ecological impact and providing an environmentally friendly alternative to new virgin cotton.
Q: Are there cotton yarn manufacturers in India that export their products internationally?
A: Yes. For instance, SKT Textile Service India and various other Yarns Pvt Ltd have become popular exporters of their high-quality Indian-made goods, contributing to this country’s status as a leading exporter in this market segment.
Q: What areas in India are known for having a high concentration of cotton yarn manufacturers?
A: Coimbatore Old City, Tiruppur,Bhiwandi, Haryana,Surat,Jaipur, and Meerut are known to have the highest concentration counts of cotton-yarn manufactures/suppliers making them critical hubs for the apparel industry
Q: What types of yams are preferred for knitting purposes?
For knitting purposes, combing yams, pure organic cotton yams, and various colored yams are preferred for their softness, durability, and versatility in knitting quality knitwear.
Q: What are the benefits of using gassed mercerized dyed yarn?
A: Gassed-mercerized-dyed-yarn brooks no longer have roughness and glitter, making them a good option for making high-quality textile products because they better absorb dyes and increase strength and durability.
Q: Are any private limited companies involved in the cotton yarn industry in India?
A: Yes, several private limited companies contribute to the growth and innovation of this sector, such as Arasur P, SKT Textile Service India Private Limited, and various other Yarns Pvt Ltd.
Q: What role do textile yarn manufacturers play in the Indian economy?
A: Textile yarn manufacturers are huge contributors to employment generation, driving exports and overall growth in the textile industry, which is among the largest sectors within India’s economy.