Viscose textile has the silk touch and flexibility, thus it is highly used in the fabric industry. It is made from natural sources such as wood pulp, which are semi-synthetic fibers that undergo a unique manufacturing process to make them soft and breathable enough for many clothing items. In this blog post, we will explore the origin of viscose fabric discussing about how it’s made and highlighting some of its properties, advantages and uses. With this knowledge at hand, you will be able to see how viscose fabric can contribute to modern apparel and home textiles if you are a fashion lover or just interested in sustainable fabrics.
What is Viscose?
Viscose is a kind of semi-synthetic fiber made from regenerated cellulose whose primary source is the wood pulp. In most cases, it is considered as silk’s fake due to its glossiness that can be mistaken for silk and its soft nature. Viscose fabric has good absorbency, breathability and drapability which make it suitable for producing different types of garments such as dresses, blouses or linings. While viscoses are turned into fibers with the help of chemical treatments, they still contain many advantages of their natural precursors which makes them act like a bridge between natural and synthetic fabrics.
Viscose and Rayon: Differences Between the Two
Often, viscose and rayon are used interchangeably although they are not exactly the same. They both come from cellulose but the manufacturing processes and characteristics differ.
The Definition of Viscose: Viscose is a form of rayon; however, when we talk about “rayon” we mean a large variety of partially artificial fibers that are made of regenerated cellulose, while viscount represents mainly through viscose method.
Manufacturing Process: The production of viscose involves dissolving cellulose in sodium hydroxide and then regenerating it into fibers. In contrast, rayon can be made using other methods such as cuprammonium process and modal process which have an effect on its properties and applicability.
Properties:
Absorbency: Both viscose and rayon are highly absorptive materials but it appears that viscous absorbs moisture slightly better.
Drape And Feel: Softness and superior drapes are some attributes that distinguish viscous from certain types of rayons necessitating clothing with flowing movement.
Durability: Though not always, usually rayon is more long lasting material that can wrinkle less than vicuna does depending on its type as well.
Applications: While for luxurious aesthetics among others, such as fancy patterns etc., this fiber is widely employed in fashion industry, different forms of Rayon find their use in products like clothes or even industrial textiles.
In summary,Varieties within these two groups exist to assist buyers or manufacturers who wish to make good choices while selecting fabric type.
Applications of Viscose Fabric
Viscose fabric, an extremely versatile material, finds use in a wide range of applications due to its unique properties. Here are some main applications:
Clothing: Viscose is generally used in the fashion industry as fabric for shirts, dresses and linings. It is smooth and drapes well providing comfort when worn.
Upholstery: Being soft with lustrous appearance makes viscose suitable for upholstering in furniture and home décor. In most cases, it is combined with other fibers to strengthen it while maintaining its luxurious feel.
Home Textiles: Moisture-wicking qualities of this fabric make it a great choice for various home textiles such as bed linens, curtains and towels thereby enhancing comfort during use.
Technical Parameters
Moisture Regain: 11-13% – This characteristic indicates how much moisture viscose can absorb thus improving breathability of clothes and ensuring comfort.
Strength: Strong when dry, weaker when wet – During normal usage viscose will retain its strength but may weaken slightly on wetting which is important for durable products.
Production Process: Chemical-intensive – The process of producing viscose involves chemicals that may be dangerous if not handled correctly hence affecting the environment directly.
All these uses together with the technical characteristics of viscose underline the importance of textile materials and fashion so that clients would comprehend what they gain from using them while also understand their production consequences.
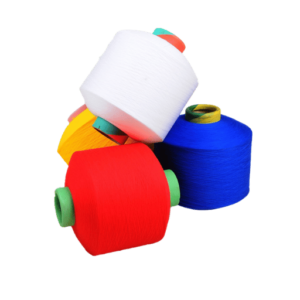
How is Viscose Fabric Produced?
A complex process results in the production of viscose fabric from wood pulp cellulose. Thus, it begins with pulping of wood chips to obtain cellulose, which is then dissolved in a chemical solution (usually sodium hydroxide) to produce a viscous liquid. The viscous solution is then allowed to age for some time before being run through spinnerets where it emerges as long filament fibers. This liquid is then passed through various filters and finally emerges as long strings of solidified fibers. These are further washed, bleached and dried prior to being spun into yarns for knitting or weaving into fabrics. However, the process raises concerns about the use of chemicals and their impact on the environment as efficient methods are used to create various fabrics.
Viscose Production Process
Quality and sustainability of viscose production depends on several crucial steps and technical parameters. Here is a brief summary from the leading industry websites:
Choice of Raw Material:
Viscose sourcing: Mainly, this product is made from wood pulp that comes from sustainably managed forests. The quality of the wood pulp affects the strength as well as appearance of the final fiber.
Chemical Treatments:
Caustic Soda: Used to dissolve cellulose in order to form a viscous solution. An optimum concentration (usually around 18-20%) is required for complete dissolution without destroyng cellulose.
Carbon Bisulphide: Commonly employed in converting cellulose into soluble substance, but usage raises concerns over its ecological impacts as it has high toxicity levels.
Fiber Formation:
Spinneret Specifications: The diameter of the spinnerets is significant, usually ranging between 0.03 and 0.5 mm, which defines fineness of filament produced.
Coagulation Bath: A solution that solidifies fibers; typically a weak sulphuric acid bath. Temperature and pH must be precisely controlled within this bath for consistent fiber quality.
Post-Production Treatments:
Washing and Bleaching: Fiber washing eliminates any remaining chemicals that may have been used during processing. Ideally, bleaching should not use toxic agents that result in environmental pollution (several times hydrogen peroxide).
Environmental Considerations:
Waste Management: Chemical recycling and reduced water consumption are being addressed by manufacturers—whichever address the large environmental print traditionally associated with normal vescouse methods.
Manufacturers can create viscous fabrics that meet superior standards by considering these technical parameters and reasons, while also aiming at more sustainable ways of producing them.
Raw Materials: Pulpwood and Beyond
Wood pulp is the main raw material for viscose production. The pill should have to meet certain quality specifications that will ensure fibers production is done most effectively. The following technical parameters must be considered in relation to sourcing wood pulp:
Type of Wood: Hardwood vs. Softwood – A hard type of wood has higher cellulose content and therefore is more suitable for viscose manufacturing than the soft one, which can still be used but crude processing may be needed.
Cellulose Content: Ideally, this should be above 90% for dissolving the cellulose successfully and formation of fiber.
Purity: Minimization in presence of lignin and hemicelluloses improves the quality of dissolved cellulose while high purity enables smooth and consistent filament output.
Dyes and Fillers – Other additives such as dyes can either be added or fillers to help make certain colors or improve fabric strength.
Chemical Solvents: Ethanol or ionic liquids are some of alternative solvents being looked into so far in a bid to reduce environmental impacts associated with traditional chemical processes.
By matching these raw materials with their respective technical parameters, manufacturers can achieve sustainable production of better qualities viscose fabrics.
The Role of Chemicals such as Sodium Hydroxide and Sulfuric Acid
Sodium hydroxide (NaOH) and sulfuric acid (H₂SO₄) play vital roles in the process of viscose production, particularly in treating cellulose to produce a solution of viscose.
Role of Sodium Hydroxide: This chemical is primarily used in alkaline. These include;
Cellulose Activation: The applied sodium hydroxide increases the size of cellulose making it more reactive and helping in dissolving it at later stages.
Degradation Prevention: This keeps the cellulose intact by inhibiting premature hydrolysis while being dissolved.
Technical Parameter: Typically, sodium hydroxide is diluted with water to 5% – 15% on weight basis for swelling purposes without excessive degradation of cellulose.
Role of Sulfuric Acid. This acidic substance is needed for the regeneration of cellulose from viscose solution. Some important tasks that it performs are:
Precipitation: While extruding, sulphuric acid precipitates regenerated cellulose fibers allowing them to form solid structures.
pH Control: It helps optimize fiber spinning process by maintaining the acidic nature of the solution.
Technical Parameter: The concentration range for sulphuric acid can be from 10% to 25% depending on desired properties of final viscose fiber used as its coagulation bath.
Thus, proper management of these chemicals not only improves the yield and quality but also enhances sustainability through increasing process efficiency and reducing wastage. Within given technical parameters, their concentrations adjustment makes the production process efficient as well as ecologically friendly.
Is Viscose an Eco-Friendly Fabric?
The eco-friendly nature of viscose in a responsible procurement and production can be seen. It is renewable as it is made from natural cellulose in wood pulp. However, the sustainability of forest practices for raw materials and the chemicals used during its production determine its environmental impact. The traditional processes for making viscose are much better than those of synthetic fabrics though they may cause considerable environmental damage if not well controlled. In this respect, therefore, how environmentally friendly it is depends mainly on modern methods of production, sustainable sourcing as well as chemical use management.
Conventionally Manufactured Viscose: An Environmental Perspective
The environmental impact of producing viscose by conventional methods is varied due to the extraction of raw materials and the production process. The main areas for concern include:
Deforestation: Deforestation often occurs in the production of viscose, especially if cellulose is derived from trees from original forests. It’s been revealed that a significant percentage of man-made fibres are obtained from endangered woods resulting in habitat loss for numerous species.
Water Consumption: It is considered that approximately 10,000 liters of water can be used to produce just one kilogram of viscose hence making this a highly water-intensive method. As such, it can deplete local water supplies particularly in areas where water shortage issues are concerned.
Chemical Pollution: Traditional manufacture involves toxic chemicals like carbon disulphide and sodium hydroxide which could if not managed properly lead to major pollution. As per reports, these substances are found in wastewater coming out from viscose plants which can then pollute neighboring waters thereby threatening aquatic life.
Carbon Footprint: Viscose manufacturing requires high energy processes than other textiles produced sustainably leading to a higher carbon footprint. Depending on whether coal, gas or renewables power them; greenhouse gas emissions associated with producing viscose vary greatly.
Waste Generation: Both liquid and solid wastes may be generated through conventional methods used in processing viscoses. Moreover, many facilities still have weak regulations and limited supervision regarding good waste management practices thus posing serious environmental concerns.
In order to reduce the environmental footprint of viscose textiles, we need sustainable forest management systems; better regulatory frameworks as well as advancements in production technologies. Furthermore, closed-loop systems should be adopted so that harmful chemicals can be recaptured or recycled thereby minimizing pollution levels at large.
Sustainable Viscose Production Drive
Efforts are being made towards more sustainable production of viscose. One major initiative to be mentioned is the implementation of CanopyStyle to advocate for responsible sourcing of raw materials and discourage textile makers from buying endangered forests. This approach has been backed up by the leading brands that promise transparent supply chain.
Similarly, closed loop production technologies have come into vogue. It is a method for solvent recycling which greatly reduces chemical waste. Nevertheless, such companies as Ecovero have managed to produce ecological man-made fibres based on this system. In comparison with conventional methods it helps decrease water footprint in the process of producing viscose by nearly 50% while maintaining zero discharge of dangerous substances.
Furthermore, certification programmes like Forest Stewardship Council (FSC) serve to ensure that wood pulp used in production of viscoses comes from sustainably managed forests. The programme requires strict environmental rules and social responsibility commitments.
In summary, responsible sourcing, technological advances and certification frameworks all contribute to sustainability in viscose production which aims at minimizing environmental effects and towards an eco-friendly textile industry.
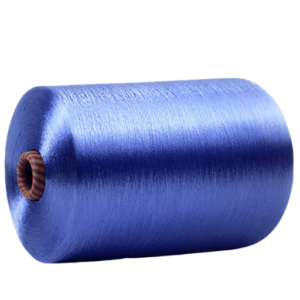
What are the Different Types of Rayon?
There are various kinds of rayon which is a versatile fiber. These include:
Viscose Rayon: This has been made from wood pulp and is the most commonly used type of rayon. It is soft and feels like silk hence well-liked in clothing and furnishings.
Modal: Its toughness, breathability, and ability to resist color fading distinguish modal from other types of viscose that come from beech tree pulp. Therefore, it finds wide applications in high quality garments especially underwear.
Lyocell: Being produced through a more environment friendly method than other types, lyocell comes from wood pulp and is extremely good at taking away moisture. Some examples of its use can be seen in clothes, hospital bed sheets, etc.
All the different types of rayon possess some particular features that suit them for application within various textile industries.
Exploring Modal, Lyocell, and More
Rayon is derived from cellulose as a fiber encompassing different kinds such as Modal and Lyocell which are characterized by unique properties and production methods.
Modal: A high strength fiber with a softness that is characterized by smooth feel. It is primarily produced through semisynthetic process of beech tree cellulose. Key technical parameters include:
Moisture Absorption: Modal can take in up to 50% more moisture than cotton thus making it comfortable to wear.
Durability: Modal does not shrink or fade and retains its shape and quality over time.
Biodegradability: Modal, like other cellulosic materials, biodegrades hence aligning well with sustainable practices.
Lyocell: This material usually stands as the most environmentally friendly substitute for rayon due to its closed-loop method of production where solvents are recycled thus minimizing environmental impact. Notable technical parameters include:
Water Consumption: As compared to conventional viscose, Lyocell utilizes less water during production thereby reducing the total environmental footprint.
Strength: Even when it becomes wet or dry, Lyocell fibers are exceptionally strong and durable.
Breathability: This particular kind of fiber is very breathable and feels silky on skin hence making it suitable for clothing.
Viscose – While not the focus of this section, I have to mention Viscose which is the original form of rayon. Its production is more resource-intensive than that of either Modal or Lyocell resulting into greater environmental concerns related to its manufacturing process. Key parameters include:
Production Volume: While viscose takes a significant portion in the market share of rayon , it has lesser environmental benefits as compared to other types mentioned herein above .
Silk-like Appearance- Luxurious drape; silkiness etc., make viscose popular for many garments reasons.
These fibers show how much progress has been made in cellulose fiber technology, reflecting a movement towards sustainability and eco-friendly practices within the textile industry.
How Viscose Differs from Other Rayon Fabrics
In terms of manufacturing processes and ecological impact, viscose differs from other rayon fabrics such as Modal and Lyocell.
Production Process: In contrast to Lyocell which recovers solvents in a closed-loop system, viscose uses much more chemicals and discharges huge amounts of wastewater. This is one reason why it has far-reaching implications on the environment.
Water Consumption: When compared with Modal and Lyocell, producing viscose typically involves using greater amounts of freshwater. High water consumption by viscose raises concerns about sustainability and resource management.
Durability: For instance, when comparing fiber strength; due to their higher wet and dry strength then it tends to provide better durability in case of fabric applications. On the other hand; modal offers good strength but not as strong as viscose despite being softer than it .
Breathability: All rayon fabrics are breathable even though Lyocell is known for its superior moisture-wicking properties that make it more comfortable in active wear than visscose.
Market Role: Nonetheless, consumers are increasingly shifting away from viscose towards eco-friendly options like Modal and Lyocell whose production methods do not pollute the environment making them gain popularity over time while at the same time reducing demand for new clothes thereby putting less pressure on resources around us.
These variations showcase an ongoing transformation within the textile industry toward greener materials, highlighting the significance of production practices vis-à-vis environmental factors as well as consumer choice.
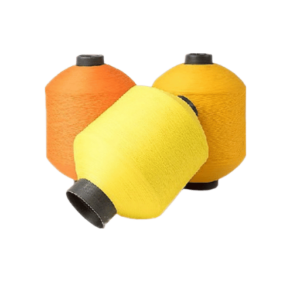
The History and Evolution of Viscose Fabric
Developed towards the end of the 19th century, viscose fabric came up as an artificial substitute for silk. Invented by French scientist Hilaire de Chardonnet in 1884, it was originally branded as “artificial silk.” The production process was refined through the years, eventually leading to its mass production before 1900. During the period between 1920 and 1930, these fabrics became popular because they were both inexpensive and could be used in making any kind of clothing item. Nevertheless, half a century later, this substance had several ecological worries associated with its manufacturing like chemical usage and waste management issues. However, despite these problems that appeared on its way, this material has changed over time with sustainable methods being integrated such as Modal and Lyocell closed- loop systems which have minimized its ecological effects within modern day textile manufacturing. Even now viscose is still important in textiles since it balances affordability against the backdrop of increasing sustainability needs.
Viscose’s Start
Viscose was created as a novel innovation during the latter part of the 19th century, and it aimed to imitate silk and provide an option that is affordable for consumers. In this context, viscose was created by dissolving cellulose from wood pulp into a thick solution which could be spun into threads or yarns. Another important characteristic of viscose production is the viscosity of the cellulose solution, which typically falls in the range of 50 to 200 centipoise (cP). This viscosity level facilitates proper flow and spinning of fibers thus contributing to ultimate quality and texture of textile.
The first methods were associated with serious difficulties such as hazardous wastes, which have stimulated significant progress in textiles manufacturing since then. The most modern techniques utilize closed-loop designs that greatly reduce harmful effluents while also making the process more sustainable in many ways. Furthermore, development has seen introduction into production eco-friendly solvents including Lyocell (a solvent-spinning technique) that are used when creating other viscous substances. To sum up, the origins of viscose represent a continuous change driven by interactions between innovation, economic requirements, and environment concerns in textile industry.
Development through Time
Viscose has greatly evolved over the years to be a versatile and environmentally friendly fabric. For starters, the production methods were primitive and entailed dangerous chemicals. Nonetheless, research and innovation have improved manufacturing techniques especially with the advent of closed-loop systems that reduce environmental pollution.
These include key parameters like:
Viscosity of the Spinning Solution: As previously mentioned, it usually varies between 50 and 200 centipoise (cP), which is vital to having good fibre formation qualities. The spinning process can still be efficient even at high viscosities though fibres produced are poor in quality as a result.
Regeneration Efficiency: The latest viscose processes have regeneration levels beyond 90% implying that most of cellulose is recycled instead of going to waste.
Resource Consumption: Modern techniques now consume about 50% less water per kilogram of viscose compared to previous ones thereby improving on water efficiency across different steps involved in this process.
Presently, there are various initiatives aimed at developing sustainable alternatives for fibers such as bamboo or wood from sustainable sources. Use of Lyocell process is one major step taken towards environmental sustainability by using more eco-friendly solvent with solvent recovery rates between 99.5%. This further cements viscose’s position in the textile market as an eco-conscious choice. Even then, consumers play a significant role in influencing how sustainable practices guide not only present but also future developments in the industry.
Viscose Fabric in the Textile Industry: Modern Age
The presence of viscose fabric is critical to the modern textile industry as it is known for its soft texture and silk-like touch. Below are some key technical parameters that govern its use and manufacture:
Breathability: Viscose possesses outstanding breathability, making it a popular choice in summer garments and sportswear; this has been related to its porous structure enabling the circulation of air.
Moisture Absorption: Viscose’s high moisture absorption rate, which may exceed that of cotton in certain cases, means it is especially appropriate for outfits designed for hot regions and physical activities; thus, enhancing comfort when wearing them.
Drape and Flow: The natural fluidity of this fabric makes possible elegant draping necessary in fashion design. Therefore viscose imparts graceful lines into clothes leading to its popularity among designers.
Color Retention: Excellent color fastness due to dye taking on viscoses ensures bright colors that resist fading needed for both fashion items and home textiles. Ability to achieve broad range of shades increases its market value.
Durability and Maintenance: Nevertheless, despite various benefits offered by viscose, it should be maintained with caution because of tendencies towards shrinkage or deterioration on being soaked. Thus, instructions regarding washing as well as care are important for people wishing to make the most out of their fabrics’ lives.
On-going innovations in the production processes for producing viscose match contemporary trends emphasizing sustainability and reduced environmental impact. Thus, as more consumers look for ecological materials, viscose responds by adjusting itself hence ensuring it finds relevance in sustainable textile future.
FQA
Q: Which is the difference between cellulose fibers and polyester filament?
A: Polyester filament is a kind of man-made fiber made through chemical process, while cellulose fibers come from sources such as plants. Cotton and rayon are examples of these materials.
Q: Is polyester filament breathable relative to natural fibres?
A: Natural fibers like cotton and viscose rayon are more breathable than polyester filaments. This is due to their lack of ability to absorb moisture, making them unsuitable for hot weather or humid locations.
Q: Could silk be replaced with polyester filament?
A: Polyester filament can act as a good substitution for silk in certain cases because it has the capacity to imitate its lustre and smooth touch. Nevertheless, unlike natural silk, it does not provide similar comfort or breathability.
Q: What are some advantages of using polyester filament in fabrics?
A: Some main benefits to using polyester filament include its durability, resistance to shrinkage and stretching, quick drying time as well as being easy care. In addition, it is less costly compared with other textile options such as cotton or silk.
Q: How does the drape of polyester filament compare to that of viscose rayon?
A: Usually, polyester filaments have stiffer drapes than viscose rayons which tend to flow better and feel softer. Viscose rayon resembles the drape and feel of silk thus making it suitable for graceful garments which fall loosely around the body.
Q: Is there any eco-friendly aspect about polyester filament?
A: When compared with other kinds of fabric production processes petroleum based products used in producing this material cannot be considered environmentally friendly since they come from non-renewable resources. Further still, this method generates waste substances that have an adverse effect on the environment; plus harmful chemicals are utilized in manufacturing steps.
Q: With what types of fabrics is polyester filament often blended?
A: In most cases, polyester filament is blended with natural fibers like cotton, rayon or wool to get the best of both worlds. This process improves texture as well as performance and hence makes fabric more versatile.
Q: In what way does polyester filament get produced?
A: Chemical processing technique through which ethylene glycol and terephthalic acid are polymerized is used in making polyester filaments. The resultant polymer is extruded through spinnerets into filament strands that are stretched and wound on spools.
Q: How widely used is polyester filament in textiles?
A: Polyester filaments are commonly found in diverse types of textiles including clothes, home décor items, technical fabrics and outdoor wears. Sporting garments such as jerseys, upholstery for furniture and curtains benefit from being made using this material given its strength.