Polyester fiber and filament have transformed the fashion industry; it is now one of the most practical and trendy fabrics on the market. Being tough, strong and inexpensive in nature, these artificial fibres, unlike natural fibers, have a scope in environments such as fashion or domestic textiles that stretch to industrial and technical textiles. Nevertheless, what makes polyester threads so essential and what are the differences in design and use of them? This tutorial delves into the world of polyester yarns, explaining its major features, varieties, and specific application fields. Whether you produce goods, create collections or just observe the state of affairs in the discipline of textile, you. It will give you a great deal of information on the use of polyester, today’s innovative material.
Introduction to Polyester Yarn
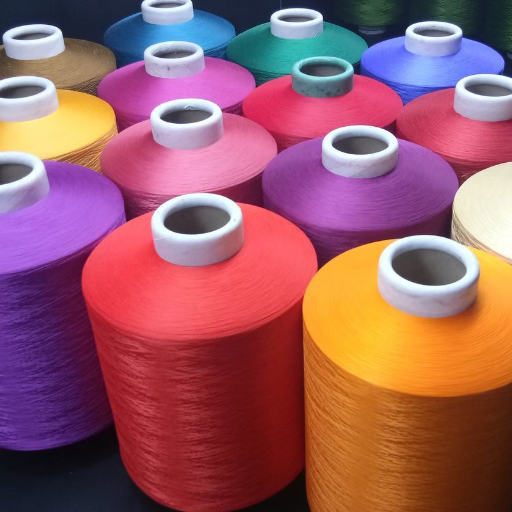
Polyester yarn is a man-made fibre particularly appreciated for its robustness and elasticity, as well as for being water-tight. It is developed using a polymerization technique with the main part being polyethylene terephthalate (PET) which offers considerable tensile loading elongation factors. One of the most remarkable reactions of this particular fibre is that it does not get faded with time even if it is gamble to the sun or washed regularly. In addition, the polyester yarn dries fast and is resistant to wrinkles and thus is used in a wide range of textile applications, so. These are among the reasons behind the extensive use of polyester in fashion, home textiles, upholstery, and technical textiles.
What is Polyester?
As it is known, Polyester is an artificial fiber which is composed mainly of polyethylene terephthalate (PET), obtained from the two major raw materials ethylene glycol and terephthalic acid, and processed through a process of chemical reaction. Its most basic structure includes long repeating ester groups arranged in the form of regular stable chains which are responsible for the high strength and stiffness of this material. Among the key features attributed to polyester is its high tensile strength, making it especially advantageous for applications where tensile load is applied. Furthermore, polyester fibers showcase absorption properties where the moisture is very low, which results in better moisture wicking properties of the fiber when used in textile, thereby increasing the wearability of the garment.
This type of material is utilized in many fields but in different forms; it is used as an activator, isochronous, and impractical pieces of appreciated stylishness in the fashion domain, coats and jackets in particular. Other than the fashion industry, due to its resistance to stretching and splitting, and its good bonding ability, the polymer in its specific form extends to various industrial uses such as making conveyor belts, reinforcing structures in tires, as well as in geotextile materials. Besides, in the context of environmental efforts, post-consumer PET polymer has been advanced, and it is now possible to process PET waste into new polymer without changing its functions. These changes have made the material known as polyester central to the development of many modern technologies.
Properties of Polyester Fibers
- High Tensile Strength
- Polyester fibers are typically strong and have a breaking point that typically ranges from 4.4 to 9.5 grams per denier (g/d) and is dependent on the type (standard vs. high-tenacity). Because of this quality, polyester may be applied as abrasion-resisting materials like belts for tires or reinforcement for industrial textiles.
- Chemical Resistance
- The facts available establish that polyester does not interact with most substances, including the majority of chemical compounds known to man. This property has the effect of making polyester-based products such as Polyester film suitable for use in extreme conditions and environments without corrosion or degradation for a longer time.
- Low Moisture Absorption
- The fibers have a moisture take-up of about 0.5% to 0.8% at 65% relative humidity. This property of the fibers alone is advantageous for applications that need to be quick dried and can also be identified with outdoor and sportswear.
- Thermal Stability
- The maximum recommended temperature range that includes air drying is 150°C. However, this material can still show its resistance under the same temperature range to maintain its integrity at the specified limit of deformation and heat resistance is of good quality, for polyester fabrics.
- Dimensional Stability
- What is good with polyester fibers is that they do not elongate and deteriorate as a result of being developed or exposed to stress or high temperatures; this is due to their low shrinkage. Their resistance to elongation is due to the fact that it is between 10% and 30% and is critical for applications where the uses are automobiles and ships.
- Abrasion Resistance
- Polyester fibers also possess unparalleled toughness attributes as they can withstand wear and tear more than most natural fibers. It is this particular feature that enhances their resistance to wear and tear especially when they are used in the construction of objects under pressure such as seat belts and conveyer belts.
There is a multitude of properties comprising mechanical, and chemical, so as to say polyester fibers are irreplaceable in many different sectors, textile industry, aircraft construction, and other innovative applications.
Types of Polyester Yarn
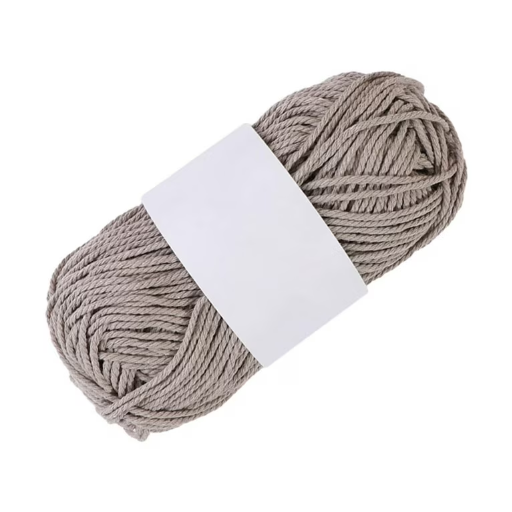
- Filament Yarn
- So, let’s begin with one of the oldest known and that is the long-staple fiber which is extruded in squiggly lines and is perfect for all military industrial clothing as much as for sewing beautiful clothes and garments.
- Spun Yarn
- Made by chopping up polyester threads into fine particles and mixing them with water before being twisted, the construction of polyester fibers. These fibers are widely used in sewing threads as well as mixed with other textiles.
- Textured Yarn
- Texturing of polyester yarn corresponds to various procedures, such as blowing modified texturizing or crimping machine, which allows bulking it up and obtaining additional stretch as well. The feature enhanced elasticity makes such type of yarn highly suited to prepare sportswear or stretchable fabrics.
- High-Tenacity Yarn
- Spun from solid filaments with an added twist in the thread, this last type of filament has more tensile strength, which is why it is mainly found in vehicle parts, seatbelts, hoses and other protective gear.
The above-mentioned variations bear testimony to the fact that this polyester fiber concrete yarn resourcescome in all sorts of configurations in order to meet the needs/requirements/orientations of both consumer as well as industrial societies.
Staple Fiber Polyester
Conventional polyester staple fiber is widely used in both clothing and non-woven sectors and is made by chopping the continuous filaments into short, equal-length segments in what is known as cut fiber. They are commonly coped with by blending with natural fibers such as cotton or wool, enhancing aspects such as durability, absence of creasing in the fabric structure, and wicking due to moisture uptake over the resultant fibers. An evolution in the short fiber production to process recycled PET plastic preforms has also been witnessed. This indicates that casual polyester staple fiber can be utilized in the manufacture of pillows, furniture, edges, filling or cushion bags, foam insulation, and within the interiors of vehicles, just to mention a few. The generation of growth in the utilization of the technology is in the integration of higher productivity, eco-balance, structure improvement, as well as the increase in the achievable physical and mechanical properties, such as breaking strength, elongation, melt temperature, etc.
Filament Yarn Polyester
Polyester filaments constitute one of the longest continuous fibers with silk-like smoothness, extraordinary toughness, and excessive application flexibility. In this case, these types of fibers are commonly used in the manufacturing of clothing, home goods, and other industrial fabrics. One of the unique aspects of such fibers is that they are engineered in order to fit particular assemblages. If desired, one can easily adjust physical and chemical properties of fibers like elasticity, stain resistance, or the ability to hold colours as the fibers are. Filament yarn polyester has very good tensile and elastic characteristics and, therefore, it is well suited for the fabrication of active wear or sportswear and technical textiles.
Recent advances in filament production have rationalized and improved significantly from the point of sustainability. For example, very efficient technological activities turn waste into new(useful) products, but they do not adversely affect the quality of the fibers. The research further suggests that in some fashion, in automobile markets, there is a rise in the sale of filament yarn polyester. Here, it is expected that the current improvement in production will also improve the thermal efficiency of the material, and thereby reduce the level of microplastic pollution from shedding, accompanied by the process of production, which also helps in creating a more circular production process.
Textured Yarn Polyester
Applications of Polyester Yarn
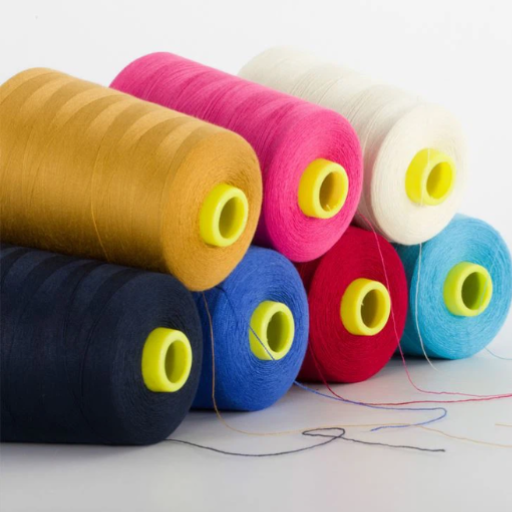
- Textile Industry
The exclusive use of Polyester fiber material in the garment industry is endless, including such products as sports, business, and even evening wear. The estimates suggest that more than 70% of all the polyester manufactured in the world is consumed by the textile industry. The ability of the material to be lightweight and wrinkle-resistant is such that it can be used for everyday clothing, and also if one demands special modern wear, for instance, highly developed kinds of cloth such as moisture-wicking and stretchy fabrics.
- Home Furnishings
Home accessories such as curtains, furniture using such upholstery material as polyester carpets or beddings using pearly grey colored sheets or finishing are just a few of the myriad examples where polyester yarn finds its usefulness. When it comes to durability issues, polyester is known to be resistant to fading and weakening after continuous exposure to sunlight or washing many times. Home textiles alone account for about 15% of the world’s total polyester yarn consumption.
- Technical and Industrial Applications
Given the high breaking load, polyester yarn is heavily used in industrial ventures, as well as fabrication sectors, such as articles such as conveyor belts, ropes, vacuum hoses, or even fishing nets. It is also an essential component in the making of non-woven materials, primarily in the course of medical and automotive usages. The need of the industrial sector for strong and long-lasting polyester yarn has resulted in a rise of above 5% CAGR in recent years.
- Automotive Industry
In terms of the automotive interior, polyester yarn is used to make seat covers, car carpets, and airbags. With good fire-retardant properties and tolerance of high load conditions, it is considered excellent for the purpose. Growth in the production of vehicles has constantly boosted the market for polyester yarn since automotive textiles have always had polyester yarn included in bulk production due to its inert properties.
- Packaging Industry
Polyester yarn is a must for the packaging sector as it is used as straps for loads, stiffening materials, and bonds. Among the well-known categories, polyethylene terephthalate or PET-based polyester yarn is commonly utilized in the production of flexible and lightweight packaging solutions.
Home Textiles
Polyester yarn is important for interior furnishings: it affects work as it provides strength, and it has great value as it can be put into many forms at an economical cost. It is used for various purposes such as curtains, furnishings, bed linens, head ties, carpets, and other materials where it is necessary to achieve wear resistance or durability. The low moisture content, which is peculiar to polyester, is ideal for commodities meant for easy care, such as bedding and furniture, especially in warm climates where quick drying is required. In addition, the modification of polyester fibers, for example, the production of microfiber, has made it possible to improve the ‘hand’ or ‘drapability of the material, which in turn serves the consumer better. The global market for home textiles is presently increasing, and polyester in yarn form takes the lead in propelling enhanced and value-driven textiles at home.
Automotive Industry
Polyester in the form of yarn is much needed in the automotive industry, especially in the making of interior parts and safety-mounted parts. High-tensile strength of the material, wear resistance, and resistance to heat are necessary for making car interiors – seat, floor carpet, back skirt and wing fabrics, to name just a few. In addition, polyester is very suitable for manufacturing of seat belt because of its high strength and resilience to high tension. Based on the latest available data, the growth of consumption of lightweight and economical motor vehicles has also led to an enlarged usage of polyester-based composites, which help cut down the weight of the auto with no loss in deliverables. There have, however, been more advances in polyester fiber technology, and such improvements have enabled the use of the material in the safety designs of automobiles through fire-resistant and ultraviolet stabilised varieties, thus expanding their use in the automotive industry.
Industrial Uses
Comparing Polyester with Other Fibers
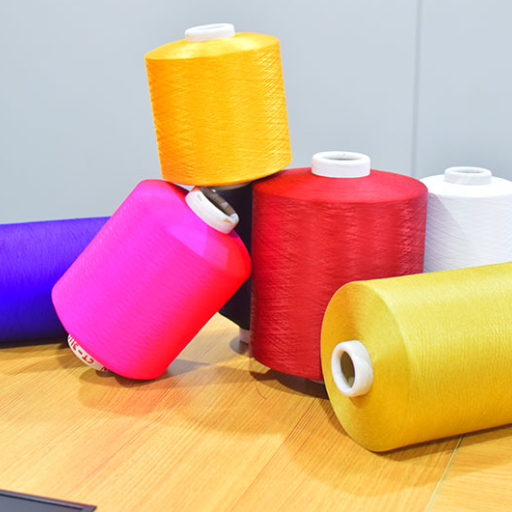
While analyzing polyester vis-à-vis other materials, it is evident that certain attributes stand out with regard to the material’s properties, performance, and application areas.
- Durability – Polyesters are highly durable textiles, particularly in terms of cloth resistance to stretching, shrinkage, and tear, outshining comparable textile made of natural fibers, such as cotton. This makes them suitable for industrial and outdoor use including for heavy-duty projects.
- Moisture Resistance – Unlike normal fibers such as wool and cotton, Polyesters are referred to as hydrophobic which in layman terms means they repel water. This quality makes it particularly suitable for making products to be used in wet areas or areas that require low wet detection time.
- Cost Efficiency – Understood to the expense of producing Synthetic Fibers, polyester carries the most advantages even when considering the costs comparing with the natural fibers and other synthetics such as nylon etc.
- Elasticity – Pure polyester threads do have some stretch abiliity, but are outperformed by the likes of spandex or elastane for their are two compounds that are far more stretchy, particularly when it comes to such items as athletic wear.
- Environmental Impact – This is because biodegradation rather, is not forth coming with polyester since it is a synthetic fabric. Nevertheless, the use of waste plastics, mainly refining plastic bottles, to make polyester is eliminating issues of sustainable development.
The above comparative factors indicate in the most unambiguous way polyester’s flexibility and appropriateness in certain contexts, especially in terms of durability, cost and resistance to dampness.
Polyester vs. Nylon
Parameter |
Polyester |
Nylon |
---|---|---|
Origin |
Synthetic, derived from petroleum |
Synthetic, derived from petrochemicals |
Strength |
High tensile strength |
Higher tensile strength than polyester |
Moisture Resistance |
Hydrophobic, resists moisture well |
Absorbs more moisture than polyester |
Durability |
Highly durable, resists abrasion |
Extremely durable, excellent abrasion resistance |
Elasticity |
Moderate elasticity |
High elasticity and stretchability |
Heat Resistance |
Less resistant to heat |
Higher melting point than polyester |
UV Resistance |
Good resistance to sunlight |
Moderate UV resistance |
Biodegradability |
Non-biodegradable |
Non-biodegradable |
Recyclability |
Widely recyclable with advanced processes |
Recyclable but techniques less common |
Cost |
Generally less expensive |
Typically more expensive |
Applications |
Apparel, home furnishings, industrial uses |
Activewear, ropes, parachutes, technical uses |
Texture |
Smooth but less silky feel |
Soft, silky, and smooth texture |
Environmental Impact |
Often recycled from PET bottles |
Lesser availability of sustainable variants |
Polyester vs. Natural Fibers
Parameter |
Polyester |
Natural Fibers |
---|---|---|
Source |
Synthesized from petrochemical compounds |
Derived from plants or animals |
Durability |
Highly durable and resistant to wear |
Durable but susceptible to degradation |
Breathability |
Low, traps heat and moisture |
High, allows airflow and moisture wicking |
Moisture Retention |
Dries quickly, low moisture absorption |
Absorbs moisture, slower drying |
Environmental Impact |
High carbon footprint, microplastic pollution |
Biodegradable, lower environmental footprint |
Maintenance |
Easy to wash, wrinkle-resistant |
May require special care, wrinkles easily |
Cost |
Generally less expensive |
Often more expensive than polyester |
Texture |
Smooth but synthetic feel |
Soft, comfortable, natural texture |
Applications |
Widely used in various industries |
Typically preferred for everyday apparel |
Recyclability |
Advanced recycling processes available |
Biodegradable, challenging to recycle |
Skin Sensitivity |
Can irritate sensitive skin |
Hypoallergenic, gentle on skin |
Thermal Properties |
Insulates poorly, traps heat |
Natural insulation, adaptable to weather |
Water Resistance |
Water-resistant, dries fast |
Absorbs water, not water-resistant |
Resilience |
Resistant to shrinking and stretching |
May shrink or stretch over time |
Lifespan |
Long-lasting with proper care |
Dependent on maintenance and natural wear |
Advantages of Using Polyester
- Durability and Strength
Polyester fibers possess an inherent stability, making these fibers bear a high resistance to elongation and shrinkage and thus appropriate for those products which are required to be long-lasting and exhibit high-level performance characteristics. In a range between 2.5 grams per denier and as much as 9 grams per denier, the tensile strength of Polyester would typically be within that range, or it may even surpass it when other factors are taken into account.
- Resistance to Environmental Factors
Compared with organic fibers, polyester is markedly durable when it comes to the influence of elements on it such as UV light, water, and microorganisms, this being one of its critical advantages for outdoor use, for instance in sails, tents, boat covers, etc.
- Lightweight and Flexible
Polyester, unlike many other alternative materials, has an even greater advantage in terms of weight, as its bulk density is at approximately 1.38 g/cm³. This of course provides great benefits in applications such as aerospace, automotive, and renewable energy, particularly in the construction of wind turbine blades.
- Cost-Effectiveness
Polyester is much less expensive to manufacture than the most common types of man-made fibers which includes nylon with costs typically being 20-30% lower production cost. This amount of price makes it possible to have mass manufacture without compromising the quality of the material.
- Chemical Resistance
The high stability of polyester fibers allows them to retain great circular strength (kNm). The stability of polyester fibers under harsh outer conditions makes them especially useful in heavy engineering industry and in corrosion protection in sophisticated equipment.
Manufacturing Processes of Polyester Yarn
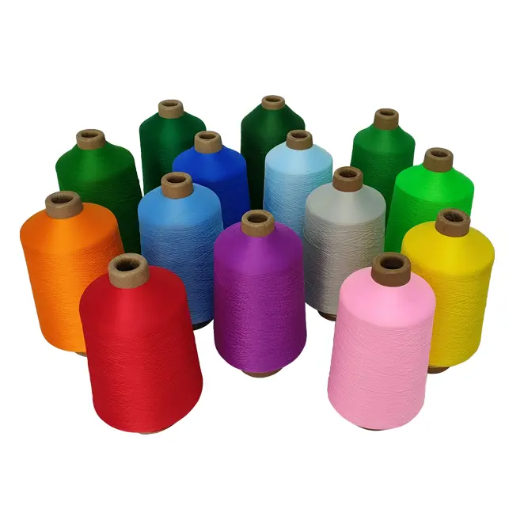
- Polymerization
The process itself begins with the following stage – the polymerization of monomers – most often terephthalic acid and ethylene glycol. They undergo reactions that help them combine and make polymer known as polyethylene terephthalate – PET which is mainly composed of polyester.
- Drying and Cooling
In the next step, the dried PET molten is immediately cooled fast to produce tiny hard lumps called chips. It is important that cooling is done effectively so as to avoid any moisture left on the chips, which can lead to later complications.
- Melt Spinning
These chips are then remelted and reprocessed to manufacture drawn polyester in the form of continuous filaments by extrusion through a spinneret. The properties of the fibers, that is, the diameter and tensile strength of the drawn filaments, are determined by the design of the spinneret.
- Drawing
The process of drawing or stretching the filaments for the incorporation of the polymers enables them straighten up and gather to make the material harder and even more resistant.
- Texturizing (if required)
Filaments formed are textured to crimp, bulk, stretch or impart any additional elasticity required by the application.
- Winding and Packaging
Spinning Techniques
- Melt Spinning
This technique of manufacturing fibers is applicable to those fibers that are used as outer textiles. For this type of process, the polymer is thermoplastic and the fiber is produced as a melt. The polymer solution is heated up, and the resultant solution is extruded out of a spinning dope blend through the pores on the tip. The spinnerets through which the solution is extruded rotate as it is extruded to form the fiber. The melt spinning process is cost-effective and simple.
- Solution Spinning
Solution spinning, on the other hand, is mainly used in the production of some special fibers, and it is carried out by dissolving the polymer in a solvent before spinning. This method is especially useful where fibers with tailor-made properties are required, and the way the drawing takes place after the fiber is made is such that the solvent used is extracted. The instant spinning allows very tight control of fiber cross-section and fiber properties, which are highly desirable features in the aerospace and military industries, as super high-performance materials are required.
The use of real time monitoring, temperature adjustments and draw ratio control systems, has significantly improved the perfection and productivity of spinning. This testimony goes further to show the efforts being made by spinners to produce, quality-based polyester yarns specifically.
Weaving and Knitting with Polyester
Development of fabrics, including those made of polyester staple, is highly structured and is based on the ability of the fibers to fulfill a particular function or to meet an aesthetic requirement. Polyester, with its good tensile elongation, is particularly useful in the generation of medium weight and heavy weight fabrics for various applications such as decorative laminates, fashion clothing and in the psyche materials that are reinforced with polypropene fiber. Also, current weaving techniques, such as rapier and air jet, allow for high weave speed with the highest tension consistent with no fabric spills and defects. Circular and flat knitting machines’ advancement has now enabled seamless garment making and the development of complex knit structures that make use of polyester, with controlled shrinking and the ability to resist color wash in the fabric. This ensures that the polyester, such as fabrics, stage shows a solution that provides high-standard quality for all the applications, especially for active wear, home interiors, and the sport industry textiles.
Reference Sources
-
Fibre2Fashion: Bicomponent Fibers: This article explores the capabilities and applications of bicomponent fibers, which combine two polymers to achieve unique properties. It discusses various configurations like side-by-side, sheath-core, and matrix-fibril structures. Key benefits include thermal bonding, self-bulking, and fine fiber production. Applications span technical textiles, hygiene products, and industrial uses.
-
Wikipedia: Bicomponent Fiber: This entry provides an overview of bicomponent fibers, focusing on their formats (e.g., side-by-side, core-sheath, segmented, and islands-in-the-sea) and applications. It explains how these fibers combine two materials to optimize properties like elasticity, softness, and durability.
-
WPT Nonwovens: Bicomponent Fiber Nonwovens: This blog highlights the composition, properties, and applications of bicomponent fiber nonwovens. It emphasizes their strength, softness, thermal bonding capabilities, and elasticity. Applications include hygiene products, medical supplies, filtration systems, and agricultural fabrics. innovation, and sustainability.
Frequently Asked Questions (FAQs)
Q: What are the different types of yarn used in the textile industry?
A: In the textile industry, there are various types of yarn made from synthetic fibers such as polyester and nylon. Polyester yarn is popular due to its strength and durability, making it ideal for a wide range of applications, including apparel and home textiles. Additionally, cotton yarn is often blended with synthetic yarn to enhance moisture-wicking properties. Other yarn types include spun yarn and filament yarn, which can be further categorized into monofilament and multifilament. Each type of yarn has unique characteristics that determine its suitability for different projects.
Q: What is the meaning of yarn in terms of fabric properties?
A: The meaning of yarn in relation to fabric properties refers to the strands of fiber twisted together to create a continuous length suitable for weaving or knitting. The quality of yarn affects the overall durability and texture of the fabric. Yarn can be made from a variety of materials, including synthetic filament yarn, which offers high tenacity and resilience. Understanding the fabric properties associated with different yarn types helps in choosing the right material for specific uses, such as moisture-wicking apparel or strong and durable upholstery.
Q: How is polyester filament yarn produced?
A: Polyester filament yarn is produced through a process that involves the extrusion of melted polyester resin through spinnerets to create continuous strands. These strands are then cooled and drawn to achieve the desired properties, such as strength and flexibility. The production can yield fully drawn yarn or partially oriented yarn, depending on the intended application. Polyester filament yarn is known for its versatility, making it suitable for a range of uses, from clothing to industrial textiles. The production process allows for the creation of various filament fibers that can be dyed to achieve vibrant colors.
Q: What are the uses of recycled polyester in textile production?
A: Recycled polyester is gaining popularity in textile production due to its environmental benefits and versatility. It is made from post-consumer plastic waste, reducing reliance on virgin materials. This type of polyester can be utilized in making strong and durable fabrics for clothing, accessories, and home decor. Additionally, recycled polyester retains the desirable properties of traditional polyester, such as moisture-wicking capabilities and resistance to stretching. The use of recycled polyester not only contributes to sustainability efforts but also meets consumer demand for eco-friendly products.
Q: What are the properties of polyester staple fiber?
A: Polyester staple fiber is characterized by its strength, durability, and resistance to wrinkling and shrinking. It is made by cutting polyester filament into shorter lengths, which are then processed into spun yarn. This type of fiber is ideal for various applications, including apparel and household textiles, as it provides comfort and longevity. Additionally, polyester staple fibers can easily blend with natural fibers like cotton, enhancing fabric properties and performance. The versatility of polyester staple makes it a popular choice in the textile industry for creating a wide range of products.
Q: How does dyeing of polyester differ from other fibers?
A: Dyeing of polyester is distinctive due to the synthetic nature of the fiber, which requires specific dyeing techniques to achieve vibrant colors. Unlike natural fibers, polyester typically requires disperse dyes that can penetrate the fiber’s structure. The dyeing process can be more complex and may involve high temperatures and pressure. This method ensures that the colors are fast and resistant to fading. Furthermore, the dyeing of polyester can be more environmentally challenging, prompting the industry to explore eco-friendly dyeing practices. Understanding these differences is essential for textile production and design.