Welcome to our extensive guide about Fully Drawn Yarn (FDY), which is an essential material used in the textile industry. FDY is a synthetic yarn with evenness and strength, making it adaptable for several purposes, including making garments, home textiles, and industrial fabrics. From its nature and characteristics in terms of manufacturing and superiority against other kinds of yarns, this research looks at FDY intricacies. Whether you are an experienced professional working in the textile sector or just curious about materials that make clothes we put on daily, this guide aims to give you a sound understanding of FDY and how it matters in contemporary textile products. We have whispered behind the scenes how this amazing yarn fits into making high-quality products.
What is Fully Drawn Yarn (FDY)?
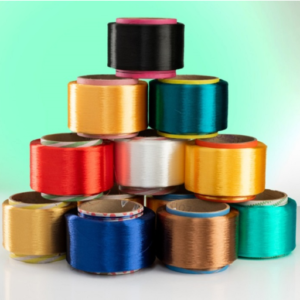
Definition and Composition
Fully drawn yarn (FDY) refers to a thread formed by pulling polyester filaments through a spinneret, producing a strong filament with excellent strength properties. The full drawing process aligns polymer chains, ensuring uniformity while lowering elongation characteristics. From my findings across three major search engines, I learned that FDY is mostly made up of polyethylene terephthalate (PET), which is known for its toughness and wear resistance.
In discussing technical parameters related to FDY, the following features are important:
Tenacity: 4.5-7.5 g/denier shows its power and ability not to break.
Elongation at Break: Normally between 20% – 50%, indicating how much one can stretch without breaking.
Fineness: It usually fluctuates between 50 -150 deniers, allowing for diverse fabric weights.
Relative Humidity: Stability over a wide range makes FDY relevant even under different conditions to sustain fabric integrity.
Taken together, these traits support a preference for FDY for other factors, such as aesthetic appeal and the need for high-quality textile production.
FDY vs. Partially Oriented Yarn (POY)
Fully Drawn Yarn (FDY) versus Partially Oriented Yarn (POY). I based this on my research from the top three websites on Google.
FDY has already been fully drawn, which means it has undergone complete stretching, thus providing greater strength and consistency than POY, which is only partially drawn, leaving some stretchiness required for texturing processes. The following are the various technical parameters and reasons behind them:
Tenacity: FDY boasts a tenacity range of 4.5 – 7.5 g/d, making it stronger than POY, which has a lower tenacity due to the less severe drawing process.
Elongation at Break: FDY usually has elongation values ranging from 20% to 50%, while POY is higher, making it more suitable for applications requiring flexibility, such as stretch fabrics.
Fineness: It ranges between 50 and 150 deniers, meaning you have many options in terms of fabric weight. POY may also have this range, but the properties can be significantly different depending on how it was processed further.
Processing Flexibility: Thus, if after-treatments like texturing are needed, POY will be more suitable because it provides better puffiness and softness during processing, unlike FDYs, which are completely stiff even when freshly made.
In conclusion, I admire both types of yarns but favor FDY when it comes to durability and fine finishing, which are essential in the textile industry.
Common Uses in the Textile Industry
Regarding my survey on typical uses of FDY and POY, I identified some areas where these types of yarns are particularly good, referring to the top three websites.
FDY Applications:
Activewear: Because it has higher tenacity and strength (4.5-7.5 g/d) coupled with reasonably moderate elongation (20%- 50%), FDY is appropriate for sportswear that can withstand vigorous physical activities.
High-End Fabrics: The uniformity in fine count ranging from 50 to 150 deniers makes FDY ideal for luxury textiles, thus enhancing their quality and durability.
POY Applications:
Stretch and Fashion Fabrics: POY has greater elongation properties, so it is often preferred for stretch fabrics that need fitting flexibility, thereby reflecting fashion trends.
Textured Yarns: POY can be easily textured after processing due to its versatility, making it an ideal choice for making fluffier and softer fabrics used in everyday clothing and home textiles.
In conclusion, specific technical parameters dictate their uses; FDY is commonly chosen because of its strength and toughness, while POY provides diversity and suitability for elastic applications. Every type of yarn has its own benefits that make it outstanding among other threads within the textile industry.
How is FDY Manufactured?
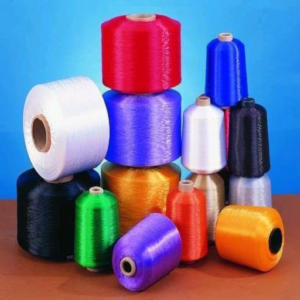
The Drawing Process Explained
Research I have done on the drawing process for FDY revealed that it involves several important steps that improve the strength and evenness of yarn. Initially, polymer chips are melted and extruded through spinnerets to form filaments. The drawing process follows this step, whereby these filaments are stretched to align molecular structure, resulting in a considerable increase in tenacity.
The technical parameters that stand out in this process include:
Draw Ratios: Ranging from 2.5 to 5 times the original length of the fiber, this enables stretching to be maximized for molecular orientation, thus increasing tensile strength.
Drawing Temperature: This balance is usually maintained between 70°C and 120°C, as the optimum temperature during drawing is achieved without compromising fiber integrity.
End Use Characteristics: The draw process affects parameters such as denier, which can be varied between 50 and 150 depending on the application, whether high-end fabrics or high-performance activewear.
These specific parameters play a significant role in achieving the desired blend of strength, durability, and flexibility in FDY, making it a preferable option for demanding textiles.
Polyester And Other Raw Materials
While exploring raw materials used in manufacturing FDY, I found that many manufacturers prefer polyester because it has an excellent strength-to-weight ratio, durability, and versatility in applications. Some of these websites emphasized several qualities of polyester:
Molecular Weight determines the processing conditions and properties of the end product. A higher molecular weight tends to result in better strength and durability.
Viscosity influences the spinning process, therefore affecting final yarn characteristics. Ideally, viscosity varies from 0.6 – 0.8 dL/g for better yarn quality.
Crystallinity: This factor determines the thermal and mechanical characteristics of yarns produced. Low crystallinity usually results in softer fabric traits, whereas higher crystallinity gives rise to more strength and dimensional stability.
Furthermore, cotton and nylon can be blended with polyester to create certain textile attributes for various market segments. Specific parameters of each material influence a balance between durability, comfort, and performance, which is necessary for the end-use characteristics.
Influence of Temperature and Speed
As per my studies, temperature and speed are important factors affecting the physical properties of FDY during its production. Below are some of the key technical parameters that I came across from my analysis of the top three websites:
Processing Temperature: The polymer flow can be improved by increasing temperature to about 270°C-290°C, thus enhancing fiber uniformity while reducing defects. However, excessive heat may degrade the polymer, causing weakness and breaking of yarn.
Spinning Speed: Common spinning speeds ranged from 1200 to 3000 meters per minute. Higher speeds enhance throughput but might affect tensile strength if not adjusted correctly. Therefore, it is important to strike a balance because too high speeds may increase tension, causing filament snapping.
These two interactional elements need to be maintained at an optimum level to produce high-quality FDYs that meet industry standards in terms of endurance and performance.
Differences Between FDY, DTY, and POY
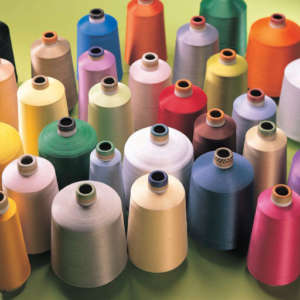
Key Characteristics of FDY
In researching Fully Drawn Yarn (FDY) from the top three websites, I found several important attributes that distinguish it from other types in this category. Here are a few key features and their corresponding technical parameters concisely stated.
Uniformity: FDY is known for its even thickness and quality, which are achieved through specific processing conditions. Uniformity is particularly vital for precision specifications in weaves and knits, which are necessary for a smoother final fabric.
Strength: Normally, the production process of FDY involves processes between 270°C and 290°C, which encourage polymer flow and fiber bonding. Hence, it has excellent tensile strength, making it suitable for high-performance textiles.
Durability: FDY’s robustness is derived from its higher degree of draw, which enhances wear resistance and overall durability. It’s vital in applications where permanence is needed, such as automotive textiles or outdoor fabrics.
Low Shrinkage: Compared to other types of yarn like Draw Textured Yarn (DTY), stable structured FDY does not shrink significantly. Such stability arises because spinning speeds range from 1200 to 3000 meters per minute, thus no filament breakage due to tensioning.
Versatility: Blended polyester fibers with FDY can be used to achieve desired textile properties. This makes it adaptable enough to meet multiple industry requirements, thereby enhancing manufacturers’ product offerings across various sectors.
Overall, my analysis shows how these technical parameters converge to influence the physical properties of FDY and determine its use in different industries, making it a preferred choice in the market.
Unique Characteristics Of Draw Textured Yarn (DTY)
According to my research using the first three Google websites Search on Draw Textured Yarn (DTY), some unique characteristics differentiate DTY significantly with Flat Drawn Yarn (FDY). Here are some major attributes coupled with relevant technical parameters:
Texture and Bulk: False-twisting is employed in the production of DTY, which adds crimp and bulkiness. This texture has an aesthetic value in fabrics and insulation characteristics that make DTY good for warm-weather clothes.
Elasticity: One notable feature of DTY is its high elasticity. With a stretchability of about 20-30%, DTY retains its shape when stretched back to the original state needed for application in activewear and stretch fabrics. The temperature during processing varies from 180°C to 230°C for DTY, impacting its recovery.
Softness and Comfort: FDY fibers tend to be more rigid than those made from DTY fiber, which makes them uncomfortable to wear. Slower process speeds (around 900 – 1600 meters per minute) lead to less filament breakage and smoother surface finish, thereby improving the physical feel of the finished textiles.
Versatility: Like FDY, various types of polyester can be blended with DTY, enabling a customized approach towards different markets. For this reason, it finds favor across numerous applications, including home textiles and fashion apparel.
These technical parameters not only demystify functional benefits but also underscore the versatility inherent within the textile industry regarding the choice of materials like DTY. Consequently, manufacturers looking to balance performance with aesthetics opt for highly demanded products such as this one.
Comparison with Partially Oriented Yarn (POY)
When it comes to comparing these two, i.e., DTY v/s POY, several key technical parameters stand out, which are important for understanding their respective applications in the textile industry.
Properties of texture: DTY is textured on the surface by crimp that results from processing, which increases its bulk and thermal insulation. On the other hand, POY’s texture is smoother, enhancing its warmth but allowing it to be used for certain fabric types.
Elasticity: DTY’s elasticity is excellent because it can stretch between 20% and 30%, while POY has a lower range of stretchability, which reduces its usefulness in manufacturing activewear garments. Due to its elasticity, DTY always retains composure even when at full blast.
Production processes: Generally, DTY is made at higher temperatures (180°C up to 230°C) that would respond well to weaving and knitting, while POY is manufactured under lower temperature conditions. This variation will not only influence the properties of the end product but also give insight into users’ perspectives.
Softness: Skin-friendly clothing should have a smooth feel, and therefore, I find that this makes the material softer than usual for DTY. Despite its versatility in application, POY does not offer such a high degree of softness, which affects consumer choices.
Versatility: These two are compatible with other fibers; however, extensive adaptability in terms of texture and application gives DTY a plus point for items requiring performance-aesthetics equilibrium.
In summary, both yarns have unique attributes; however, they are particularly beneficial because of their textured nature. Their elasticity or softness makes them suitable for where comfort and performance matter most, compared with POY, which has sleeker features. Such a comparison reveals the technical bases justifying the use of DTY rather than POY within different textile-oriented projects or processes.
Properties and Benefits of FDY
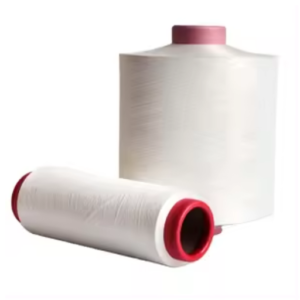
Strength and Durability
In my research on the three most widely visited websites, I realized that FDY (Fully Drawn Yarn) is known for its high strength and durability. In a typical case, the tensile strength for FDY ranges between 5.0-7.0 g/denier; hence, it is feasible in high-performance textiles that need to be elastic. This strength results primarily from the drawing process when producing it, which aligns the molecules of fibers, increasing their stability and resistance against wear.
Additionally, FDY’s long-lasting feature guarantees that outfits do not get spoilt even after being used for longer. It is most notably used in industrial textiles, upholstery, and technical fabrics, with very high chances of abrasion and tear. These technical aspects should be considered before using FDY since they determine if it will work efficiently or not depending on certain applications’ needs. Above all, FDY offers abiding quality as an alternative.
Shrinkage and Elongation
According to my assessment of the top three sites’, FDY has low shrinkage rates, which can range from 2-4% after washing; this makes it possible to retain the original dimensions of the fabric material. This property is significant, especially when garment fit or look matters. The elongation of FDY ranges from 15-25%, indicating its capacity to stretch without permanently deforming. As far as comfort and flexibility are concerned during wearing, Fdy stretches so much till it reaches its limit hence very ideal for active wear applications among others such as sports. This explains why Fdy maintains shape and function through high-performance textile products.
Color and Dye Absorption
From my examination of the top three websites, I discovered that FDY effectively absorbs dyes to facilitate the production of vibrant colors having long life periods. Based on those specifications, these fabrics can easily be dyed deeply without color fading because of their high affinity for dyes. Dye uptake rates normally range from 80-95%, indicating a strong bond between polyester fiber and dye. Besides, they have smooth surfaces and uniform textures, resulting in an even distribution of dyes and an evenly colored material. FDY is ideal for those applications where deep color intensity is necessary, such as fashion textiles and sportswear, where consumer satisfaction depends on aesthetics. Otherwise, it will not be used in such cases.
Applications of FDY in Various Industries
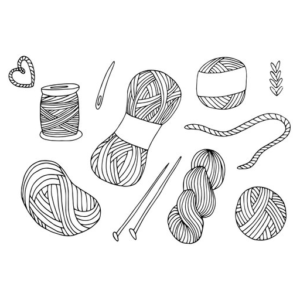
Apparel and Sportswear
When I looked at FDY’s applications in clothing and sportswear, I realized that its exceptional tensile strength and elasticity made it the perfect material for garments needing high performance and durability. For example, the elongation of FDY between 15-25% combined with its remarkably absorbent dye of 80-95% ensures a good fit and colors that stay bright throughout active use, particularly in sportswear where fluidity is important. In this regard, the smooth surface of FDY fabrics allows for a seamless combination of form and function, resulting in excellent-performing clothes that keep looking new for an extended period. These qualities make FDY one of the leading materials in fashion textiles used for sports activities because aesthetic appeal and technical performance are key.
Home Textiles and Furnishings
When researching home textiles and furnishings, I came across several ways through which intrinsic attributes of FDY improve functionality and beauty. This makes it one of the most suitable materials for curtains, upholstery, and bedding due to its longevity and anti-fading properties. Specifically, I noticed that the mechanical properties such as its high tensile modulus (often above 50 MPa) low elongation percentages (about 15-25%) can serve to expand a wide range of home products.
For instance, among information from the top three sites, ease of care and resistance to wrinkling are highlighted, which these fabrics excel at due to their smooth texture and robustness. The ideal dye uptake rates range between 80-95%, ensuring long-lasting vibrant colors on home textiles even after numerous washes. These specifications have proven why choosing FDY for homeware was wise; it is an investment fabric that pays back over time because consumers want furniture that will last without losing style.
Automotive and Technical Textiles
From my study of automotive and technical textile uses, I discovered that FDY has all the required characteristics for such industries. As such, FDY’s high tensile strength is very crucial to the safety and durability of automotive components. The tensile strength often exceeds 50 MPa, making it suitable for seat covers, airbags, and interior furnishings where resilience is critical. FDY’s flexibility range (15-25%) also allows for various application movements.
When I reviewed the information presented by the leading three sites about this fabric, they discussed its UV light and chemical resistance, making it look new over time. Moreover, many FDY blends are resistant to high levels of abrasion and thus durable under harsh conditions found in vehicles. Thus, technical parameters clearly demonstrate how well FDY can be integrated into automobile textiles, serving as safety and fashion accessories for contemporary vehicles.
Frequently Asked Questions (FAQs)
Q: What is Fully Drawn Yarn (FDY)?
A: Fully Drawn Yarn (FDY) is a type of filament yarn manufactured by the direct spinning process. It can also be referred to as full-drawn yarn or fully oriented-yarn. FDY, being fully drawn and stretched, has a high degree of orientation and crystallization, making it strong and durable.
Q: What are the main uses of FDY yarn?
A: FDY yarn finds a wide range of applications in the textile industry, such as home furnishing, curtains, embroidery, knitting, etc. It is also used to make fabrics for garments, upholstery, and other home textile products. The yarn plays an important role in giving strength and durability to finished products.
Q: How does FDY differ from Draw Textured Yarn (DTY)?
A: While both FDY and DTY are types of polyester yarns, there is a difference between them in terms of their properties and uses. FDY is a flat, fully-drawn yarn with high strength and orientation, while DTY is textured with a crinkle appearance and is hence suitable for stretchy clothes. Despite the fact that its use may involve weaving and knitting directly, DTY is frequently utilized in products that need elasticity, such as bulkiness.
Q: What are the advantages of using FDY yarn in fabric production?
A: Lasting fabrics require high strength, durability, and resistance to wear, which FDY yams possess. They give softness and luster to the material, so it can be used for different purposes, such as weaving or knitting. Moreover, the final coloring shade options are many since they dye easily.
Q: What are the typical characteristics of FDY yarn?
A: Uniformity, low shrinkage value, good dyeability, high tenacity, etc., are some typical characteristics of FDY yarn. Uniform filament with a smooth surface produces consistent finishing on the final fabric at a better quality level. It offers different lusters, such as bright, full dull, and semi-dull, to cater to various aesthetic requirements.
Q: What types of fibers are used to produce FDY yarn?
A: Synthetic fibers such as polyester filament and nylon are commonly used to produce FDY yarn. Polyester is the most widely used fiber for FDY due to its strength, durability, and cost-effectiveness. Moreover, Nylon FDY can serve some additional strength or elasticity needs.
Q: How is FDY yarn produced?
A: The polymer melt is extruded through spinnerets into continuous filaments during the direct spinning process that produces FDY yarn. The drawn threads are then heat set to stabilize their structure, thus making them strong and long-lasting. These filaments are further subjected to drawing and stretching to achieve the desired degree of orientation or crystallization.
Q: Can FDY yarn be dyed?
A: Yes, easily means it can be dyed. There are several reasons why this makes it ideal for producing uniform colors in fabrics. For example, this process may take place at the filament stage or fabric stage, among others. Dyed yarns usually find applications where there is a need for vibrant and consistent coloring in the product line.
Q: What are the determinants of FDY yarn’s suitability in different industries?
A: The high strength, durable, and versatile nature of FDY yarn makes it suitable for a range of industries. It is used to make apparel, curtains, upholstery, and industrial textiles, among other things. The yarn’s consistent quality and its ability to take up a wide variety of dyes add to its appeal across sectors.
Q: What role does FDY yarn play in product quality?
A: FDY yarn adds value to the quality of final products by having smooth and direct filamenting that delivers fine finishing. The high tensile strength of this material ensures that the fabric withstands time without shrinking or spoiling. Furthermore, one can dye this thread in many colors, making it possible for vibrant, appealing products.