The inception of the polyester yarn is rooted in the world of chemical engineering and contemporary fabrication techniques. From clothing to industrial products, this yarn serves as a primary ingredient across various industries. In this post, we will discuss in detail how petroleum, which is a derivative of crude oil, is used to produce superb yarn. Initially, we will take a look at petroleum extraction and its refinement to obtain the raw materials crucial for the production of synthetic yarn. After this, we will elaborate on the process of polymerization, where pre-existing raw materials are converted into long-chain polymers. Afterward, the focus will move to the polymer’s spinning and extrusion processes, whereby the polymers are subjected to mechanical and chemical forces to abrade them into threads. In conclusion, we will cover the techniques of finishing and texturizing that augment the parameters of practicality of the yarn to make it appropriate for a myriad of applications. The purpose of this article is to shed light on the polyester manufacturing cycle starting from the raw materials to the completion of the product. The views presented here are formal, direct and analytic, and the aim is to close the gap between the different stages of production.
What is polyester yarn and how does it differ from other fibers?
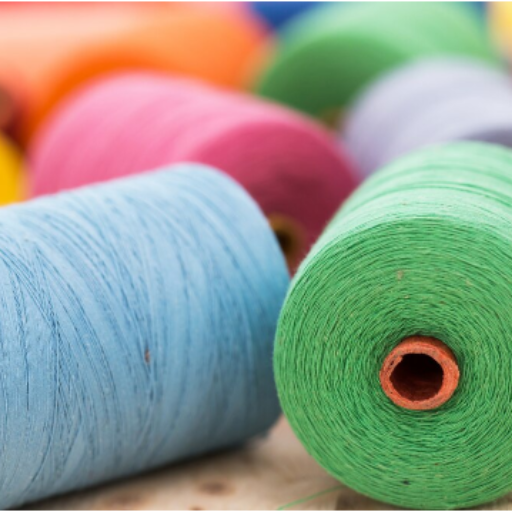
Polyester is a man-made polymer fiber sourced from two main polymers: polyethylene and terephthalate (PET). It is created through a process of polymerization, where specialized units called monomers combine to form chains of molecules. Such structure is what gives polyester high strength, exceptional durability, and resistance to damage from stretching, shrinking, or getting exposed to chemical mediums. Polyester yarn differs from organic fibers like cotton or wool in its hydrophobicity – moisture resistance which allows for quick drying and makes it ideal for a range of performance fabrics. When compared to other man-made fibers, such as nylon, polyester has a much higher resistance to damage caused by UV rays and tends to keep shape and color for much longer. Because of these properties, polyester yarn is greatly in demand in the textile industry, as well as for industrial uses and the manufacture of blended fabrics.
Understanding synthetic fibers: Polyester vs. Nylon
Like all synthetic fibers, polyester and nylon are distinct in terms of structure, functionality, and use. Nylon, for example, is made from polyamide chains while polyester is made from polyethylene terephthalate (PET). These variances structurally result in different properties.
Nylon is more absorbent than polyester, which makes it more water resistant and quick drying compared to other fabrics. Nylon does have more absorbent qualities but is still water resistant. It can take longer to dry than polyester and other fabrics in high humidity environments though.
Unlike polyester, nylon has a higher tensile and abrasion strength making it a choice fabric for heavy use materials like nets, ropes, and outdoor equipment. Whereas polyester is highly resistant to sun damage which means it is better for long use than nylon as it gets degraded by UV light.
Soft touch and smooth fabric best describes nylon while stiffer and coarse best describes polyester. Such characteristics are a huge factor when choosing dress and upholstery fabrics.
Because of its low resistance to chemical and sunlight damage, polyester does not fade easily which is a big advantage over nylon.
In terms of environment, both fabrics come from petroleum but polyester can be made from recycled PET plastics so it is a better choice in the recycling department.
In summary, regarding which to go for; polyester fabric or nylon, it is contingent upon how the product is to be used with several areas like moisture consideration, strength, look, and environmental influence, coming into play.
The chemical composition of polyester: Polyethylene terephthalate (PET)
Often called PET, polyethylene terephthalate is a thermoplastic polymer resin of the ester group. Its chemical structure contains duplicates of ethylene glycol and terephthalic acid joined by ester links. PET has considerable tensile strength, is durable, and has superb thermal stability and moisture resistance. Owing to its properties, PET is used extensively in fabrics and plastic bottles and containers. In addition, it has good recyclability and is easily processed, which makes it popular in many industries.
Types of polyester yarn: Filament vs. staple fiber
Since filament polyester yarn is made up of continuous unbroken fibers, it merges well with various products that need to be both high strength and high gloss. This continuous filament yarn is used for clothing, home textiles, and industrial materials due to its uniformity and high abrasion resistance. Usually, filament yarn types have linear densities ranging from 50-600 deniers and tensile strengths ranging from 4.0-7.5 cN/tex according to their intended use.
On the other hand, staple fiber polyester yarn is made of short fibers ranging from 38 mm to 76 mm. Short fibers help in spinning effective soft, versatile, and breathable yarn. Placed within cotton and other natural fibers or used as padding or insulation, staple fiber yarn is extremely comfortable while long lasting and moves easily with the user. Its tensile strength measures from 3.5-5.0 cN/tex while its fineness ranges from 1.2-3.0 tex depending on the requirements.
What are the raw materials used in polyester yarn production?
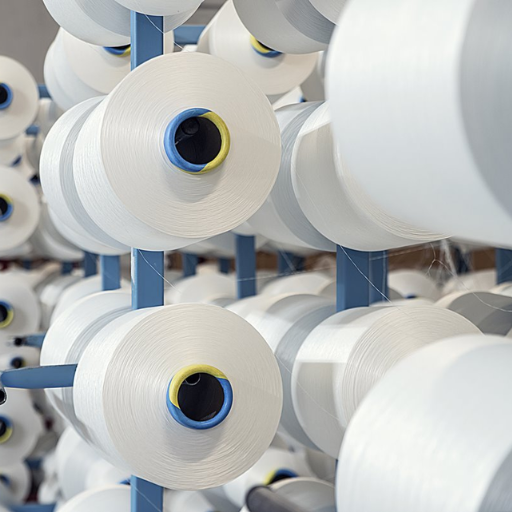
The basis of manufacturing polyester yarn is polyethylene terephthalate (PET), which can be obtained from petrochemical processes. It is produced through a reaction of purified terephthalic acid (PTA) and monoethylene glycol (MEG). These substances will polymerize into polymer chips, or filaments, which are the starting products of polyester fibers. Also, during manufacturing certain additives can be used to achieve better dyeability, flame retardance or UV stability, depending on the application.
Petroleum-based ingredients: Ethylene glycol and dimethyl terephthalate
Ethylene glycol is an important petroleum product that is used as a feedstock in polyester production. It is obtained from the polymerization of ethylene. Out of the many functionalities it serves, the most vital one is ensuring that the resulting materials have the optimal molecular structure and performance attributes. DMT serves the same function as terephthalic acid and is produced from a transesterification reaction between methanol and dimethyl terephthalate (DMT). Both of these products are produced from oil and gas, which points to the dependency of the synthetic fiber industry on the petrochemical industry.
The role of monomers in polyester synthesis
The construction of polymer chains in the polyester requires monomers, which serve as the fundamental constituent in its synthesis. The synthesis of polyesters requires the condensation polymerization of ethylene glycol and other diols with terephthalic acid and dicarboxylic acids with cleavable linkages to polymers. In broad terms, the process calls for intensive physical and catalytic parameters that regulate the molecular weight and ensure the required functional traits in the end material. More semantically, it is impossible to create polyester without the specific monomeric components being selected and reacting to diols and dicarboxylic acids.
How is polyester fiber created through polymerization?
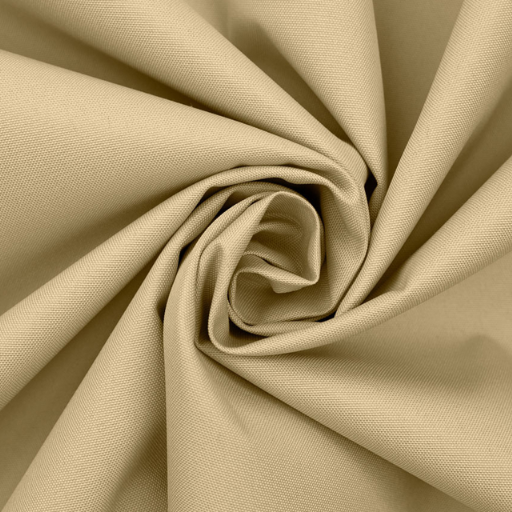
Polyester fiber can be made by polymerizing monomers such as ethylene glycol and terephthalic acid. This begins with esterification, or transesterification of these monomers which goes on to produce dimethyl terephthalate or similar intermediate compounds. The intermediate then undergoes a process called polycondensation. In this process, long polymer chains are formed at elevated temperatures (typically in the presence of a catalyst). These chains become cooled, solidified, and chopped into chips, or pellets; they are then melted and drawn into fine Polyester fibers. Such precision in the process ensures that the polyester fibers have the desired strength, elasticity and durability.
The chemical process of polymerization explained
The process of polymerization is a chemical reaction that requires careful monitoring of certain parameters to obtain the desired characteristics of a polymer. Below is a brief discussion of these parameters:
Temperature – The temperature of the esterification at the reaction stage usually falls between 250 to 280°C. For the polycondensation step, the required temperature is 270 – 300°C to maintain the optimal conditions for the reaction.
Catalyst – Various catalysts can be used, such as antimony trioxide (Sb2O3) or titanium alkoxides (which are compounds of titanium). These catalysts assist in increasing the efficiency of the reactions as well as in forming uniform chains within the polymer.
Pressure – The initial stages of polymerization are typically carried out at atmospheric pressure or slightly elevated pressures. However, while undergoing the polycondensation stage, a vacuum of 0.1 – 1 mmHg is routinely used to remove unwanted by-products such as water or methanol that may interfere with polymerization.
Reaction time – The time for reaction can change based on the desired application and weight of the polyester. For this reason, polycondensation can last anywhere between 5 to 10 hours.
Viscosity – An indirect measurement of the molecular chain length and strength of the polymer is termed intrinsic viscosity (IV). For polyester fibers that have commercial use, IV between 0.5 and 0.8 dl/g is optimal.
Cooling and Solidification – After the reaction, the polymer melt is cooled rapidly to form solid chips or pellets. It should be noted that the cooling rate is very crucial and prevents undesired crystallization which may influence fiber spinning performance.
These parameters and range are strictly controlled which allows for the high quality polyester polymers to be produced reliably for many different industry sectors.
Factors affecting the degree of polymerization
The factors affecting the degree of polymerization are numerous. First, an influencer is the concentration and type of monomers, since imbalances in stoichiometric proportions can create a barrier to chain elongation. Second, the temperature and pressure around the reaction should be controlled as well to avoid unwanted termination reactions. Lastly, the existence of contaminants or polymerization catalysts plays a crucial role in determining the reaction kinetics, as some of the catalysts speed up the polymerization and contaminants slow it down. In this manner, polymerization can be controlled in such a way that, on the output, the desired molecular weights of polymers as well as their good quality are achieved.
What is the melt spinning process in polyester yarn manufacturing?
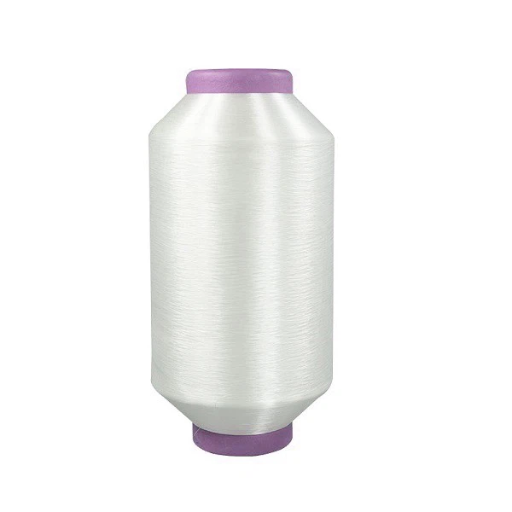
In manufacturing polyester yarns, melt spinning is a process whereby molten polyester is forced through holes in a spinneret, thereby forming continuous filaments. The process starts with a filter that eliminates impurities and maintains the uniformity of the polyester melt. The molten material is then extruded through the spinneret which has fine perforations to form very fine threads. These are subsequently cooled and solidified with an air quenching, and later on, undergo alignment and orientation, which is facilitated through mechanical drawing. This final alignment improves the tensile strength of the yarn. Subsequently, the yarn is placed in spools for subsequent processing or application. Melt spinning is efficient for the large-scale production of robust synthetic fibers with the required dimensions.
Steps involved in melt spinning: From molten polymer to filaments
Polymer Preparation – The first step involves melting the polymer which is usually polyester. The process is geared towards achieving a clean uniform state. This is used to guarantee that the final properties of the filament are uniform.
Filtration – Each polymer must be filtered to get rid of any other pieces that may interfere with the quality of filaments.
Extrusion Through Spinneret – The purified molten polymer is put inside the spinneret. The spinneret is a plate-like structure that contains many very small pores to produce constant threads.
Cooling and Solidification – These threads are air quenched for solid then cooled and solidified. This process should be done very quickly to ensure that the filaments do not lose their shape.
Drawing and Orientation – The filaments require increasing mechanical tension in a manner that aligns the molecular chains in the desired direction. This increases the tensile strength and enhances the mechanical attributes of the yarn.
Winding – Finally, the spools and drums of the filaments are made ready for further processing such as weaving or blending by winding them.
These processes are very crucial in making synthetic fibers with the desired dimensions and mechanical features.
The importance of cooling and solidification in yarn formation
Cooling and solidification are crucial in yarn formation because they impact the quality and performance of the end product. In my opinion, rapid cooling allows for the fibers to keep their shape upon solidification because it guarantees structural stability. This step is essential for achieving the desired mechanical properties such as strength and elasticity by fixing the molecular arrangement that was set during drawing. If sufficient cooling is not applied, the filaments are more likely to be defective and not uniform, hence less usable in subsequent processes of textile manufacturing.
How are different types of polyester yarn produced?
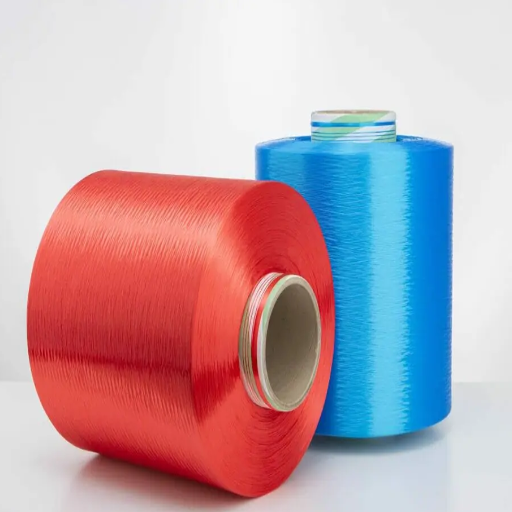
When producing polyester yarn, several different steps have to be taken so that the yarn produced with the desired characteristics is of high quality. The main step usually commences with the plastic raw materials’ refinement into the ester version of polyethylene terephthalate (PET). Purified terephthalic acid (PTA) and ethylene glycol (EG) are used in the polymerization process. The resulting molten polymer gets squirted through spinning nozzles, leading to the production of filaments.
The filaments are pulled and looped immediately to ensure that the CFY is duly created. To imitate natural fibers, the continuously produced filaments are clipped off into shorter segments and spun into cotton blend yarns. Bulk and elasticity are imparted to the textured yarns, which are produced by subjecting the CF yarns to texturing techniques, like twisting and heat-setting. Changes in processes such as altering draw ratios, cooling rates, or texturization yield different yarn characteristics and integrate these properties into CFY.
Conventional polyester vs. cationic dyeable polyester
Conventional polyester is hydrophobic and is devoid of dye sites, so it can only be dyed with dispersed dyes at high temperatures and pressures. This restricts its dyeing vibrance and uniformity. Cationic dyeable polyester (CDP), on the other hand, is a chemically modified version of polyester that has ionic groups and increased dye affinity towards cationic dyes, thus facilitating richer pigments and better colorfastness under low energy conditions. CDP is also more compatible with other fibers which gives it an upper hand in textile engineering.
Creating textured polyester yarns: False twist and air jet texturing
Texturing processes add properties of bulk, elasticity, and thermal insulation to the polyester yarn. Two of the most popular methods are false twist texturing and air jet texturing, which each has longstanding consistent use for particular products:
False Twist Texturing: In this method, the polyester filaments are twisted while they are being heated. Afterward, the filaments are cooled off and twisted in the opposite direction. In doing so, the polymer’s helical structure is set inside the yarn. This method produces yarns that are bulgy, soft, and stretchy, which increases device applications for leisurewear and fabrics that stretch. Furthermore, the elasticity and aesthetic aspect of the yarn can also be enhanced by controlling parameters like the temperature of the heater, twist density, and filament tension.
Air Jet Texturing: In contrast with the false twist, which uses high-pressure air jets to mingle the polyester filaments, air jet texturing does. From this activity, loops and more random surface structures, which give the filaments the characteristics and appearance of simply spun yarn, are obtained. Air jet texturing is an energy efficient alternative as it does not need the thermal setting. The new types of yarn that appear from the process have lower elasticity, but provide a lot more bulk and durability, and even have moisture-absorbing features. So they are especially good for outdoor clothes, upholstery, and civil engineering nylon textiles.
Both approaches contribute significantly to the design and production of fabric, providing an option for customized style and use that is sorely needed by end users.
References
Frequently Asked Questions (FAQ)
Q: What are the primary ropemaking materials used in polyester yarn production?
A: Polyester yarn is primarily made from petroleum-based materials. Polyester is a synthetic fiber that is created through a chemical reaction involving coal, air, water, and petroleum. This process results in polyester staple fibers and filament yarns, which are essential in polyester production.
Q: How is filament yarn produced in the polyester production process?
A: Filament yarn in polyester production is created by melting polyester chips and extruding them through spinnerets to form long continuous fibers. These fibers can be used directly or further processed into textured yarns, such as polyester false twist textured yarns, which enhance the yarn’s properties for specific applications.
Q: What role does crimp play in the production of polyester yarn?
A: Crimp is introduced to polyester fibers to enhance their bulkiness and elasticity, making them suitable for applications like home furnishings and synthetic clothing. This is achieved through various techniques, including mechanical and chemical methods, to add texture to the fibers.
Q: How does the supply chain impact the availability of polyester yarn?
A: The supply chain is crucial in the availability and pricing of polyester yarn. Disruptions in the supply chain can affect the supply of raw materials like petroleum, which in turn impacts polyester production. To understand more, you can visit the CFDA Materials Hub within the supply chain for detailed insights.
Q: What are some common applications of polyester staple fibers?
A: Polyester staple fibers are commonly used in textile applications such as clothing, home furnishings, and industrial textiles. These fibers provide durability, resilience, and ease of care, making them ideal for various end-use applications.
Q: How does the variation in the knitting process affect polyester yarn?
A: Variations in the knitting process can alter the texture and properties of polyester yarn. Techniques used in knitting can influence the yarn’s stretch, strength, and overall appearance, making it suitable for different types of fabric creations.
Q: What is the significance of lubricants in the production of polyester yarn?
A: Lubricants are used during the spinning and processing of polyester fibers to reduce friction and static, improving the efficiency of production and the quality of the final yarn. Proper lubrication ensures smoother operation and higher-quality textile products.
Q: How is the materials index helpful in understanding polyester yarn production?
A: The materials index provides comprehensive data and analysis on the raw materials used in polyester yarn production, including petroleum and other essential components. This index helps manufacturers and researchers understand trends and make informed decisions about sourcing and production.
Q: Why might a page about polyester yarn production be temporarily down or it may have moved permanently?
A: A page about polyester yarn production might be temporarily down due to website maintenance or technical issues. Alternatively, it may have moved permanently to a new web address as part of a website update or reorganization, requiring users to adjust their bookmarks accordingly.
Q: How are warp and weft used in the context of polyester yarn?
A: Warp and weft refer to the two basic components used in weaving to turn yarn into fabric. In polyester yarn production, these fibers are interlaced at right angles to create strong, durable fabrics used in various applications, from apparel to industrial uses.