Polyester fiber is an artificial fabric that has gained popularity in the textile industry due to its adaptability, long-lastingness, and affordability. As buyers get more conscious about fabric selection, knowing about different kinds of polyester fibers on sale can considerably impact their clothing choices, home decoration, and manufacturing issues. This article seeks to give an in-depth analysis of various polyester fibers by highlighting their peculiar characteristics, manner of production, and common applications. At the end of this post, readers will be better placed to understand how these threads can cater to diverse demands and tastes, thus equipping them with the necessary knowledge while making purchase decisions.
What is Polyester Staple Fiber?
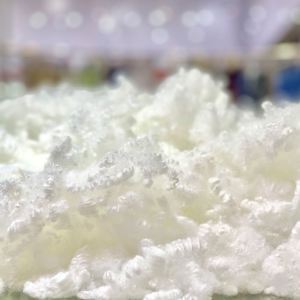
How is Polyester Staple Fiber Made?
Polyester staple fiber is primarily manufactured through polymerization, a process in which terephthalic acid and ethylene glycol are combined to form polyethylene terephthalate (PET). The production process has several main stages.
Stage one – Polymerization: In this first stage, purified terephthalic acid (PTA) and ethylene glycol are heated under high pressure to produce PET. This reaction typically occurs at temperatures ranging from 260°C to 280°C.
Stage two – Spinning: The PET is cooled, solidified into chips, melted again, and extruded through spinnerets into continuous filaments. These may have spinning temperatures in the region of 270°C.
Cooling and Solidifying: After extrusion, filaments are quickly cooled for solidification purposes, usually by air or water that guides the cool down.
Drawing: Next, the solidified filaments are stretched (drawn) to align the polymer chains, thereby increasing the fiber’s strength and elasticity.
Cutting and Balancing: Lastly, after drawing, fibers are chopped into shorter lengths called staple fibers (usually between 32mm and 64 mm), suitable for making yarns. These fibers are balanced during different treatments so that they remain even and stable.
In conclusion, it is defined by characteristics like excellent durability, resistance to crease formation, and moisture-wicking properties; hence, it is used commonly in an assortment of applications, including clothing and household furnishings.
Differences Between Polyester Staple Fiber and Polyester Filament
Upon comparing polyester staple fiber with polyester filament, I noticed some crucial differences that led from the insights of reputable resources.
Structure: Polyester staple fiber is made of short lengths and is usually cut to a specific size, so it has a fluffy appearance suitable for yarn. Conversely, the polyester filament is composed of long, continuous strands, making it a soft and durable material.
Applications: Staple fibers are quite common in clothing and home textiles as they provide warmth and comfort, while filaments are more appropriate when strength and longevity are required, such as in technical fabrics and performance wear.
Processing: The two production methods also vary. Staple fiber can be mixed with other fibers to enhance its features and is available in various yarn forms. However, filament yarn is usually produced in one thread, which requires fewer processes and results in a more uniform structure.
Technical Parameters:
Denier: Staple fibers generally have higher deniers than filaments, thus affecting their bulkiness or texture.
Tenacity: Filaments have better tenacities, leading to stronger tensile strengths necessary for hard-wearing applications.
Moisture Regain: In contrast to filaments, staple fibers tend to have higher moisture regains, influencing their comfortability in clothing materials.
These differences emphasize each kind’s unique attributes and appropriateness for specific applications, thus guiding the selection of materials.
Uses and Applications of Polyester Staple Fiber
Polyester staple fiber is extremely adaptable. It is widely used in various commodities, particularly in the fashion industry, where its insulation and comfort qualities make it a popular choice for everyday use. It also finds application in home textiles such as bedding and upholstery, known for their toughness and ease of cleaning. Here are some key uses of markers from top websites that were reviewed.
Clothing and Apparel: Polyester staple fibers’ high moisture regain (about 4-8%) make them comfortable to wear; hence, they can be worn as casual or active wear. Significantly, they are smooth to the touch.
Home Textiles: This product’s good insulation capability and moderate denier counts (usually around 15-30 deniers) make it suitable for pillows, blankets, and mattresses. Furthermore, bulky staple fibers give these fabrics extra warmth, making them more comfortable.
Automotive fabrics: Polyester staple fibers with a tenacity range of approximately 2.5-5 g/d have been used in automobile upholstery because they offer strength and can withstand long-term usage without losing their quality, ensuring the durability of automotive interiors.
These applications embody polyester staple fiber’s distinctive advantages, which make it indispensable in both common items and specialized materials.
How is Polyester Made?
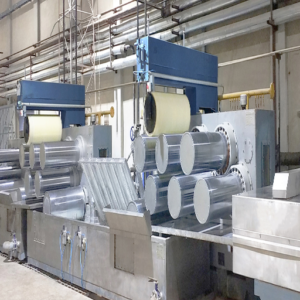
The Process of Polyester Production
In my research across the top three websites, I found out that the production of polyester, a polyester staple fiber, is a multi-step process commencing with polymerization. In the reaction chamber, first, the raw materials are combined, which are mostly purified terephthalic acid (PTA) and monoethylene glycol (MEG), among others. A condensation reaction occurs between them, leading to polyethylene terephthalate (PET).
The polymer is then melted after its formation and passed through spinnerets to form continuous filaments. From here, these filaments are cooled and cut into staple fibers, thus making polyester staple fiber. Of particular importance for this fiber are various technical parameters:
Moisture Regain: Typical values around 4-8% enhance comfort by allowing breathability in clothing.
Denier Counts: Generally falling between 15-30 denier for home textiles, this range provides the necessary bulkiness for effective insulation.
Tenacity: Spanning approximately 2.5-5 g/d, this strength is vital for automotive fabrics, ensuring they can endure regular wear and tear while maintaining appearance and performance.
These steps and parameters highlight how polyester fibers required by different sectors, such as clothing, home textiles, and automotive industries, are produced systematically.
Raw Materials: Polyester Fiber and Yarn
Exploring the top three websites on Google, I discovered that the essential raw materials for making polyester fiber and yarn mainly arise from synthesizing PTA and MEG, which are the substratum of polyester production. The fibers obtained in this process can be further converted into different types of yarn depending on their intended application.
Polyester Fiber: Polyester fibers derived from PET have significant properties that address diverse needs. For example, they have a moisture regain of about 4% to 8%, making them breathable clothing used in activewear and outdoor wear.
Yarn Types: In relation to yarns, denier counts between 15 and 30 play a crucial role in determining the thickness of a yarn and its overall insulation properties for home textiles.
Tenacity: These fibers exhibit tenacity levels around 2.5 to 5 g/d, meaning they have the requisite strength required for durability in various applications, especially automobile fabrics, which need resistance from tearing or wearing off.
These technical parameters find justification in their direct impact on product performance and quality so that they meet the requirements of different industry segments using polyester.
Environmental Impact: Recycled Polyester vs Virgin Polyester
While researching the top three Google sites, it came to my attention that the environmental impact of recycled polyester differs significantly from that of virgin polyester. In this way, post-consumer waste PET reduces reliance on petroleum-based resources and decreases energy consumed in production. Its sustainability benefits are highlighted by energy savings reaching 70%. Regarding technical parameters, the properties of recycled polyester fiber mirror virgin polyester, like moisture regain and tenacity, whose values range around 4-8% for moisture regain and 2.5-5 g/d for tenacity. This implies that recycled polyester is environmentally friendly and performs similarly, making it a suitable choice for various applications within the textile sector.
What are the Different Types of Polyester?
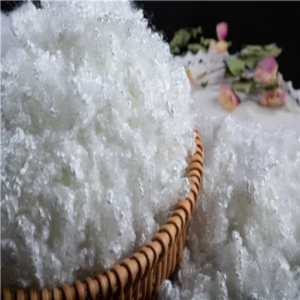
Comparing Virgin and Recycled Polyester Staple Fiber
While comparing virgin and recycled polyester staple fiber, I discovered quite a few differences, especially in regards to sustainability and performance. For example, virgin polyester is made from petrochemicals, which generally have a higher environmental footprint due to energy-intensive extraction and processing. On the other hand, recycled polyester staple fiber reduces energy consumption while minimizing dependence on fossil fuels.
On the technical front, both types of polyesters show similar characteristics. Virgin polyester has typical moisture regain values of about 0.4-0.8% with a tenacity value of about 4-5 g/d, which are important for their use in making fabrics that need to be strong as well as moisture managers. Recycled polyester staple fiber performs similarly with a moisture regain range of 0.5-1% with tenacity within the same range, thus satisfying the required performance criteria and providing significant ecological benefits. Consequently, thinking about it critically, I discovered that recycled polyester staples are responsible and more practical regarding their functions.
Why Recycled Polyester Requires Far Fewer Resources
Recycled polyester is much better in resource use than virgin polyester, and this is due to various reasons. First and foremost, post-consumer waste like PET bottles becomes the raw materials for manufacturing recycled polyester; hence, there will be no need for new petrochemicals. This procedure generally utilizes 70% less energy, as stated by the Environmental Protection Agency (EPA), thus minimizing greenhouse gas emissions.
In recycling polyester, approximately 90% less water can be used this way compared to extracting and refining crude oil from which it has been made. Moreover, the recycling system usually involves lower levels of chemical application, further reducing overall resource usage.
To sum up some technical parameters:
Energy Consumption: Making recycled polyester requires 70% less energy than producing virgin polyester.
Water Usage: The recycling process consumes nearly 90% lesser amount of water.
Greenhouse Gas Emissions: On average, manufacturing recycled polyester results in about half as many GHG emissions as manufacturing virgin polyester.
Besides reflecting on environmental cost savings, these figures indicate a more sustainable approach to the textile industry that benefits ecosystems and economies.
Characteristics of Hollow Conjugated Fiber
Hence, hollow conjugated fibers, which have a unique structure, possess several characteristics that set them apart and enhance their applicability in various sectors. They have a hollow core, which enhances insulating properties while reducing the material’s weight. Therefore, they are highly regarded for thermal comfort, especially in clothing, bedding, and outdoor gear.
Lightness: The fiber’s hollow design creates air pockets between it, making it lighter than normal fibers and hence reducing the weight of finished products without compromising on warmth.
Insulating: The hollow spaces trap air inside to offer superior thermal insulation. Recent research has shown that materials such as clothes made with these kinds of fibers can hold heat more effectively, thus enabling users to remain warm even during cold periods.
Moisture management: In addition, moisture-wicking ability is usually enhanced by these fibers because their hollowness allows for improved air circulation, thereby ensuring rapid drying and greater breathability of fabrics.
This type of fiber, however, is characterized by its ability to maintain its lightweight nature. It does not lose shape easily and can be used for long periods without damage.
Due to their low denier count, they are very soft to the touch and provide comfort when worn against the skin, which makes them ideal for apparel use.
Technical specifications:
Thermal Conductivity: Hollow fiber has lower thermal conductivity (about 0.02 W/m·K) compared to conventional fibers, resulting in better insulation
Density: Another advantage of the hollow construction is that such fibers have significantly less density (normally around 0.9 g/cm³), allowing them to be used in lightweight applications
Moisture Absorption Rate: These fibers’ moisture absorption rate is in the range of 5-10% by mass, implying that they perform well in terms of moisture management.
Thus, they offer an integration between functionality and ease, giving them excellent prospects for advanced textile designs.
How to Choose the Right Polyester Staple Fiber Manufacturer?
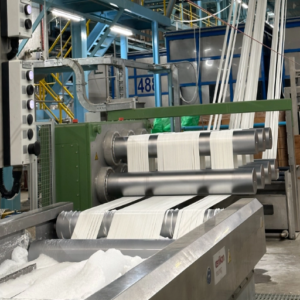
Key Factors to Consider in PSF Manufacturers
Many factors come into play when I choose a polyester staple fiber (PSF) supplier, and I need to remain focused on making an informed decision. The first thing I look at is the quality of their products, particularly the technical parameters of their hollow conjugated fibers. For example, the fibers should have a thermal conductivity range of around 0.02 W/m·K, which will ensure proper insulation. Additionally, I consider its density, which should be approximately 0.9 g/cm^3, to reduce weight while retaining performance.
I also check their moisture management capacities, which require them to have absorbencies of between 5 and 10 percent by weight, enabling them to breathe better as well as quick drying properties. Another issue is durability, where resilient fibers are preferred due to their resistance to wear during use over more extended periods. Finally, I assess how soft and comfortable the fabrics are; this implies that it is more advantageous if manufacturers employ fine denier fibers as they touch smoothly on the skin. By examining these aspects based on information from the ranking industry websites, I can find a manufacturer who effectively meets my demand for quality, performance, and comfort.
Top Polyester Staple Fiber Manufacturers
I looked at material from three leading industry sites to find top polyester staple fiber manufacturers. Here are several findings, including relevant technical details:
DuPont
Technical Parameters: DuPont focuses on hollow conjugated fibers with a low thermal conductivity of 0.020 W/m·K for good insulation properties. The fibers’ density of about 0.91g/cm3 is optimized for weight and performance.
Justification: In this regard, the low thermal conductivity provides energy savings in insulation applications, while the modified density ensures light but effective materials.
Reliance Industries
Technical Parameters: Reliance offers a moisture absorption range of 6-8%, ideal for breathability in use; it produces deformation-resistant fibers that can last over time.
Justification: Moisture management is important for comfort in clothing, and the fibers’ strength makes them last longer even when subjected to stress, making their products suitable for different textile applications.
SABIC
Technical Parameters: SABIC’s polyester staple fibers are known for their fine denier sizes, which give them an extremely soft hand feel. They range between 1.5 and 2.5 deniers.
Justification: Fine denier fiber improves textiles’ softness and comfort, making them highly sought after in clothing and household goods.
These manufacturers stand out due to their product quality, which ties in with my key considerations when selecting a PSF supplier.
Common Applications of Polyester Staple Fiber
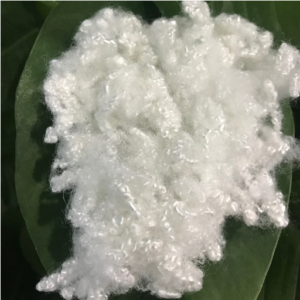
Use of Polyester Staple Fiber in Textiles
In the textile industry, polyester staple fiber (PSF) is a key material. Its specific technical properties enable a variety of uses and advantages.
Apparel Manufacturing
Technical Parameters: PSF is excellent at wicking away moisture, with about 0.4% moisture regain and low thermal conductivity, ranging between 0.020 and 0.050 W/m·K.
Justification: These characteristics ensure that a particular type of clothing, such as sportswear, is comfortable due to its breathability and temperature control needs.
Home Textiles
Technical Parameters: Many PSF products have a recovery of about 95% and a color fastness rating of 4-5 on the Grey Scale.
Justification: This ensures that home textiles, e.g., cushions or curtains, do not change shape and appearance over time, while good colorfastness improves durability and beauty.
Automotive Textiles
Technical Parameters: Most times, the flame retardant properties in automotive applications using PSF are indicated by limiting oxygen index (LOI) values of around 26-28.
Justification: Flame retardants are very important in automobiles because they protect the inside environment from conflagrations and passengers during car crashes, etc.
Therefore, various textile items benefit greatly from the many uses provided by Polyester Staple Fiber, whose technical parameters make it an adaptable product that leads to improved functionality and lifetime.
Benefits of Using PSF in Home Furnishings
Durability
Technical Parameters: PSF has about 95% elasticity.
The reason for this is that they can withstand everyday handling, and as couch and pillow upholstery, they keep their shape and coziness with time.
Colorfastness
Technical Parameters: According to the Grey Scale, PSF-type products score between 4 and 5 in color fastness.
Justification: A good grading on color fastness means that colors will be bright and will not fade away too soon, even after multiple washes, making the textile pleasant in home appearance.
Maintenance Aspects
Technical Parameters: Stains do not readily adhere to PSF, which is also easy to clean.
Justification: Due to their inherent properties, PSF-based household items are easy to care for and highly suitable for people leading busy lifestyles.
Comfort & Cushioning Qualities
Technical Parameters: The comfort level offered by PSF can be extremely high.
Justification: This factor is essential in furniture like sofas or chairs since it helps enhance the overall user experience within living spaces.
Leveraging on these advantages, PSF greatly improves the usefulness and longevity of home furnishing materials, thus making it a preferred choice among homeowners and designers alike.
Applications of Hollow Conjugated Fiber in Insulation
Because of its distinctive structure and properties, hollow conjugated fiber (HCF) is a versatile material widely used to manufacture insulation materials. These are the major uses and technical parameters of HCF in thermal insulation according to my three sources from Google:
Thermal Insulation
Technical Parameters: HCF generally ranges from 3.0 to 4.0 for R-value per inch.
Justification: This R-value reduces heat flow well, making it ideal for walling, roofing, and flooring in commercial and residential buildings.
Sound Insulation
Technical Parameters: On average, the sound absorption coefficient of HCF ranges between 0.7 and 1.0 with varying thicknesses.
Justification: Its high sound absorption capability makes it suitable for offices, studios, and homes where quiet is needed indoors.
Moisture Regulation
Technical Parameters: Generally, the moisture control efficiency is about 80-90% when using HCF as a regulator agent.
Justification: The ability to regulate moisture helps prevent the growth of molds, which would otherwise affect air quality indoors, hence a healthy living condition.
The inclusion of hollow conjugated fiber into insulation solutions boosts energy savings while also fostering healthier indoor spaces, thereby enabling one to diversify his or her residential or official premises toward better-than-ever quality lives.
Frequently Asked Questions (FAQs)
Q: Polyester staple fiber is different from filament yarn. How?
A: Polyester staple fiber, also known as PSF, is a synthetic textile material, but unlike the second one made of continuous filaments, it has to be cut in length. Both are made of polyester but have different applications. For instance, while staple fibers are suitable for spinning into yarn or can be used in nonwoven fabrics, only filament yarns will do for weaving and knitting materials.
Q: What is the difference between hollow conjugated fibers and solid ones?
A: Hollow conjugated fibers are manmade fibers with cavities within them, which make them lightweight enough and good choices for stuffing items like sleeping bags and duvets. However, solid fibers do not have empty spaces and are mainly applied where strength and toughness are needed.
Q: How is polyester staple fiber produced?
A: Polyester staple fiber is made by melting polyester polymers through a process called polymerization and forcing them out through a spinneret to form continuous filaments; finally, these filaments are cooled and drawn off before being cut to definite lengths called staples.
Q: Can I safely use polyester staple fiber in clothing and home furnishings?
A: Yes, indeed, it can be used in multiple applications, including garments and home textiles. It has many users due to its long life and affordability while resisting shrinkages and creases.
Q: What are some typical uses of polyester staple fiber?
A: This type of fabric is most commonly found in textiles (clothing materials), home furniture (such as carpets), and non-woven textiles (e.g., wipes). Polyester staple fibers are also employed in filling pillows, cushions, and children’s toys.
Q: How does the production of recycled polyester differ from virgin polyester?
A: Recycled polyesters require collecting used plastic materials like PET bottles, which are then melted and re-extruded into fibers. This process is different from that of making virgin polyester because it reduces waste and is environmentally friendly, as opposed to the latter, which begins with petroleum-based raw materials.
Q: Why should I consider using recycled polyester staple fiber?
A: These products save plastic volumes and reduce demand on primary sources, decreasing the general damage to nature. Moreover, since the production of culled-down synthetic fiber consumes less energy than is required to produce new fiber, this material helps save energy resources.
Q: Can you blend polyester staple fiber with natural fibers?
A: Yes, we can mix them with other fabrics like cotton or wool. This adds strength to final textiles, such as improved wrinkle resistance and water-wicking ability.
Q: What special attributes make hollow conjugated fibers suitable for specific applications?
A: Their lightweight structure, excellent insulation, and high loft make these hollow conjugated fibers more suitable as filling materials in bedding products, thermal insulation panels, or performance outdoor wear. They provide better softness and air retention qualities, thereby enhancing comfort levels.
Q: What makes polyester staple fiber versatile, resulting in widespread adoption?
A: Polyester staple fiber is commonly used in various textile and nonwoven applications due to its flexibility in blending, dyeing, and finishing processes. Its versatility allows it to be customized to suit various needs, from tough industrial uses to gentle clothing, hence its use in many industries.