Polyester yarn has become a key material in the textile industry, celebrated for its durability, versatility, and wide range of applications. But have you ever wondered how this essential fabric ingredient is created? This article takes a deep dive into the fascinating process of polyester yarn manufacturing, demystifying the intricate steps that transform raw materials into high-quality textiles.
We’ll explore the entire production cycle, beginning with the sourcing and preparation of raw ingredients, such as petrochemicals, and moving through the polymerization and extrusion processes. Next, we’ll examine how the polyester is stretched and transformed into yarn, paying attention to the technical precision that ensures consistent quality. Finally, we’ll discuss how this yarn is utilized in creating finished fabrics and the role it plays in various industries, from fashion to home furnishings.
What Is Polyester and How Is It Made?
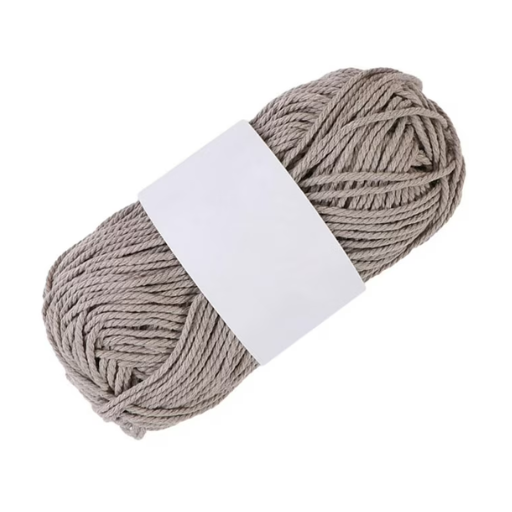
Polyester is a type of synthetic polymer textile that is formed through a reaction known as polymerization. This process entails fusing two compounds, ethylene glycol and terephthalic acid, that are made of hydrocarbons. This gives rise to polyethylene terephthalate (PET), the base material for the fusion. The PET produced is subsequently melted, made into long strands, and cut into chips. These chips are then melted again and extruded through a spinning machine to make fibers that can be woven into yarn. It is impossible to ignore the polyester due to it being inexpensive and immensely useful in multiple disciplines including manufacturing clothing and durable industrial textiles.
Understanding Polyester as a Synthetic Fiber
Polyester, a synthetic fiber, is known for its exceptional versatility and durability. It is hydrophobic, meaning it resists moisture, making it ideal for applications requiring water-repellent properties, such as outdoor gear and rainwear. Its wrinkle resistance, strength, and ability to retain shape have made it a popular choice in the textile industry, especially for clothing and home furnishings like curtains and upholstery. Additionally, polyester is easily blended with natural fibers to enhance their durability and performance.
Beyond textiles, polyester finds widespread use in industrial applications, including tire reinforcements, conveyor belts, and safety belts, due to its high tensile strength and minimal elongation under stress. Modern advances in recycling have also amplified its sustainability, with recycled PET fibers increasingly adopted to reduce environmental impact, demonstrating its adaptability in the face of growing eco-conscious demands.
The Role of Petroleum in Polyester Production
The production of polyester begins with petroleum, serving as the primary raw material in the form of purified terephthalic acid (PTA) or dimethyl terephthalate (DMT) and monoethylene glycol (MEG). These petrochemical derivatives undergo a polymerization process to create polyethylene terephthalate (PET), the base material for polyester fibers. Petroleum’s role is crucial as it provides the hydrocarbons necessary to synthesize the molecular structure of polyester, contributing to its strength, durability, and versatility. However, reliance on petroleum raises concerns regarding environmental impact, as its extraction and processing contribute to greenhouse gas emissions and resource depletion. Advances in technology have enabled partially bio-based alternatives and recycling processes, such as reusing PET from plastic bottles, to reduce dependency on virgin petroleum, offering a more sustainable pathway for polyester production.
Key Raw Materials in Polyester Yarn Manufacturing
The primary raw material used in polyester yarn manufacturing is polyethylene terephthalate (PET), a polymer derived from petroleum-based resources. PET is synthesized through the polymerization of two key ingredients—terephthalic acid (TPA) or its derivative dimethyl terephthalate (DMT) and monoethylene glycol (MEG). These components are essential to creating the strong and durable properties that polyester is known for.
Additionally, catalysts such as antimony, titanium, or cobalt compounds are often used during the manufacturing process to facilitate the polymerization reaction. Another emerging raw material includes bio-based alternatives like bioethylene glycol, which is derived from plant-based feedstocks, marking a step towards more sustainable production practices. Water and energy also play important roles in the process, ensuring the polymerization and spinning stages operate efficiently.
These raw materials, alongside innovations in recycling technologies that enable the reuse of PET from recycled plastics, contribute to the growing diversity and adaptability of polyester yarn production methods.
How Does the Polyester Yarn Manufacturing Process Work?
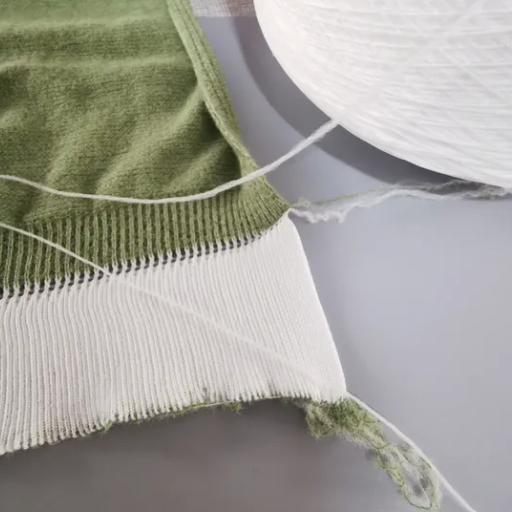
The polyester yarn manufacturing process involves several key stages. First, raw materials such as purified terephthalic acid (PTA) and monoethylene glycol (MEG), or their plant-based equivalents, undergo polymerization to create polyethylene terephthalate (PET). The PET is then melted and extruded through spinnerets to form continuous filaments, which are rapidly cooled and solidified. These filaments are stretched and oriented to enhance their strength and elasticity, resulting in yarn with desirable properties. Finally, the yarn is wound onto spools, ready for further processing like dyeing or weaving. Advances in recycling technologies now allow PET from recycled plastics to be reintegrated into this process, promoting sustainability.
Step-by-Step Breakdown of Polyester Yarn Production
Polymerization
The process begins with the creation of polyethylene terephthalate (PET) through a polymerization reaction. This involves combining terephthalic acid (TPA) and ethylene glycol (EG) under controlled heat and pressure to form the polymer chain, PET.
Drying and Melting
The resulting PET is dried to remove moisture and then heated until it melts. This step ensures the polymer achieves the proper consistency for extrusion into fibers.
Extrusion
The molten PET is pushed through spinnerets—metal plates with tiny holes—creating continuous filaments. The size, shape, and quantity of these holes determine the properties of the resulting yarn.
Cooling and Solidification
The extruded fibers are cooled rapidly using a flow of cold air, solidifying them into filaments. This step is critical for stabilizing the structure of the fibers.
Drawing and Stretching
The filaments are drawn and stretched to align the polymer chains, which enhances the fiber’s tensile strength, elasticity, and overall durability. This step is essential to achieve high-quality polyester yarn.
Winding
Finally, the stretched filaments are wound onto spools, resulting in continuous yarn that is ready for subsequent processes such as dyeing, texturing, or weaving into fabrics.
Sustainability in Polyester Yarn Production
Modern advancements have introduced recycling methods that allow post-consumer PET plastics, like bottles, to be broken down and reintegrated into the process. This innovation reduces waste and energy usage, making polyester production more sustainable while maintaining the material’s desirable qualities.
The Importance of the Melt Spinning Process
Due to it’s adaptability, melt spinning is quite essential in the manufacturing process of synthetic fibers such as polyester yarn. It refers to heating a polymer until it turns into a liquid, using a spinneret to create filaments, and then cooling down the fiber to solidify it. It’s popular because of the high-quality fibers it produces from textiles and even industrial materials. Fibers produced through melt spinning have uniformity, strength, and can be tailored for thickness and a plethora of other attributes. Additionally, its flexibility to be integrated with recycled components emphasizes its contribution towards eco-friendly endeavors in the textile industry.
Transforming Molten Polyester into Filament Yarn
The process of melt spinning features the remarkable efficiency and accuracy required to convert molten polyester into filament yarn. To begin, polyester chips or recycled polyester materials need to be melted and heated to a molten state. The molten material is extruded into a spinneret, which consists of multiple small holes, producing continuous filaments. Upon emerging as filaments, they are cooled rapidly to solidify their structure along with the desired characteristics. This technique guarantees the quality of fiber is not compromised, enables the thickness and strength of filament to be altered, and supports high speeds of production.
The advantages melt spinning offer makes it highly useful throughout all facets of the textile and industrial sectors. The ability for it to be utilized with recycled polyester greatly enhances sustainability by minimizing waste and advancing the circular economy. Innovations continue to make melt spinning more efficient, proving its place as one of the best methods in fiber production technology that manufacturers utilize to produce high-quality eco-friendly filament yarns.
What Are the Different Types of Polyester Used in Textiles?
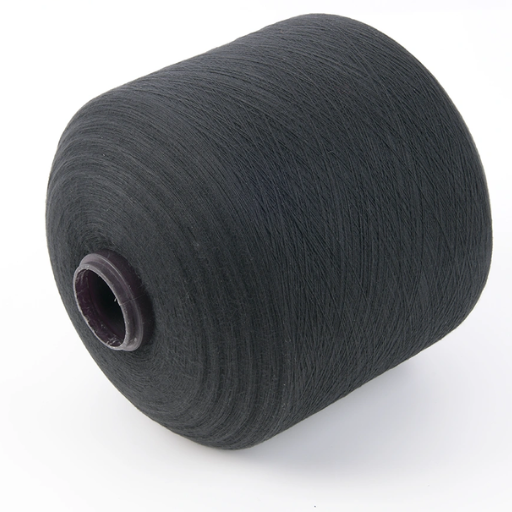
Polyester used in textiles can be categorized into several types, each with distinct properties and applications. The most common types include PET (Polyethylene Terephthalate), which is widely used due to its durability and versatility; PCDT (Poly-1,4-Cyclohexylene Dimethylene Terephthalate), known for its elasticity and resilience; and recycled polyester, which is made from post-consumer plastic like PET bottles, promoting sustainability. Additionally, microfibers, a subset of polyester, are used to produce lightweight, soft, and high-performance fabrics. These variations make polyester adaptable for everything from apparel to upholstery, offering solutions for virtually every textile need.
Exploring Various Forms of Polyester Fiber
Polyester fibers come in numerous forms, each tailored to meet specific demands within the textile industry. Staple fibers, for example, are cut into short lengths and resemble natural fibers like cotton or wool, making them ideal for blending with other materials. Filament fibers, on the other hand, are continuous and smooth, often giving fabrics a silk-like quality that is perfect for sleek and durable garments. Hollow fibers provide insulation and lightweight properties, making them common in outerwear and bedding. Beyond these types, textured polyester fibers are engineered to enhance elasticity and bulk, creating more versatile and comfortable fabrics. Each form of polyester fiber offers unique functionality, ensuring its relevance in a wide range of applications, from activewear to industrial use.
Polyester Filament vs. Polyester Staple Fiber
Polyester filament and polyester staple fibers differ primarily in their structure, applications, and properties. Polyester filament is a continuous fiber, offering a smooth, glossy texture and excellent strength. It is widely used in applications such as upholstery, sewing threads, and technical textiles. Its consistent structure allows for superior durability and resistance to abrasion.
On the other hand, polyester staple fiber is cut into short lengths, mimicking the properties of natural fibers like cotton or wool. These shorter fibers are often blended with other materials to create soft, breathable fabrics commonly used in apparel, home furnishings, and non-woven applications such as insulation and filters.
While polyester filament is ideal for products requiring strength and uniformity, polyester staple fiber excels in providing a natural feel and adaptability in a variety of uses. Both fibers serve essential roles across industries, each tailored to distinct needs and functionalities.
How Different Types of Polyester Impact Fabric Quality
Polyester impacts fabric quality in several ways, depending on the type used and its specific characteristics. Polyester filament fiber enhances durability, wrinkle resistance, and smoothness, making it suitable for high-performance fabrics such as activewear and outdoor gear. Its uniformity provides a sleek finish, improving the overall aesthetic and endurance of the material. On the other hand, polyester staple fiber contributes to a softer, more natural texture, blending well with fibers like cotton or wool for added breathability and comfort. This adaptability makes it ideal for casual wear, upholstery, and applications prioritizing a cozy feel. Additionally, advancements such as recycled polyester offer eco-friendly options without compromising on functionality, ensuring sustainability aligns with quality demands.
Why Is Polyester Yarn a Popular Choice in the Textile Industry?

Polyester yarn is a popular choice in the textile industry due to its versatility, durability, and cost-effectiveness. It excels in strength, resisting wear and tear, while maintaining its shape over time, making it ideal for a variety of applications. Polyester yarn is also resistant to shrinking, stretching, and wrinkles, ensuring longevity and ease of care. Additionally, its adaptability allows for blending with other fibers, enhancing functionality and meeting diverse needs such as comfort, breathability, and aesthetic appeal. These qualities, combined with advancements in sustainable production methods, make polyester yarn a reliable and innovative option for modern textiles.
Advantages of Using Polyester in Fabric Production
Polyester is widely regarded as a versatile and reliable fabric choice due to its numerous advantages. Its durability ensures resistance to abrasions, tears, and weathering, making it suitable for both everyday and industrial use. The fabric’s quick-drying properties and moisture-wicking capabilities make it ideal for sportswear, as it helps to keep the wearer dry and comfortable during physical activities. Polyester is also lightweight, retains its shape well, and resists shrinking or stretching, providing lasting wearability over time. Furthermore, it is easy to dye, allowing for vibrant and fade-resistant colors in textile production.
Sustainability is another factor driving polyester’s prominence. As recycling technologies advance, recycled polyester—often derived from plastic bottles or post-consumer waste—is becoming a popular eco-friendly alternative, supporting circular economies and reducing environmental impact. Combined with affordability and adaptability for use in blends, polyester remains a dominant choice in fabric production globally.
Comparing Polyester with Natural Fibers
Polyester and natural fibers like cotton and wool differ significantly in their properties, uses, and environmental impacts. Polyester, a synthetic fiber, is prized for its durability, moisture resistance, and resilience. Unlike natural fibers, it is less prone to wrinkling, shrinking, or stretching, making it a low-maintenance option for garments and textiles. Additionally, its quick-drying properties and tensile strength make polyester ideal for activewear and outdoor gear.
Natural fibers, on the other hand, stand out for their breathability, softness, and biodegradability. Cotton offers superior comfort and absorbency, making it suitable for everyday wear, while wool provides natural insulation, keeping users warm in colder climates. However, natural fibers require more care, as they are more likely to shrink, wrinkle, and degrade over time when compared to polyester.
Environmental considerations also differentiate the two. While natural fibers are biodegradable, their production—especially cotton—requires significant water, pesticides, and land use. Polyester production relies on fossil fuels but has seen advancements in sustainability through the use of recycled materials. Both fiber types have unique strengths and trade-offs, with their suitability often depending on the specific application and consumer priorities.
Applications of Polyester Yarn in Various Textiles
Because of its strength, adaptability, and economical pricing, polyester yarn is useful in combination with the majority of textiles. One such textile Polyester blended with natural fibers, particularly cotton, is highly preferred in the clothing and apparel industries, because it adds strength while reducing the wrinkles and permanently enhances resilience. With such qualities, it has become the number one choice for activewear, casual, outerwear, and workout apparel.
In addition, polyester is commonly used in home textiles like curtains, beddings, and upholstery. These fabrics benefit from polyestyer’s superior stain-resistance, fading, and stretching. In addition, nurses and paramedics appreciate the durability of polyester non-woven fabrics used in scrubs. Industrial textiles like safety ropes, conveyor belts, and safety harnesses also utilize polyester yarn, due to its high durability and resistance to environmental conditions, such as moisture or abrasion.
Polyester is also widely used in technical textiles, such as non-wovens for medical or hygiene products, geotextiles, and packaging. Because of the perpetual innovation in the field of recycled polyester, polyester became more dominated in more conventional and novel textile industries, solving the issues of consumers while protecting the nature.
How Is Polyester Fabric Produced from Polyester Yarn?
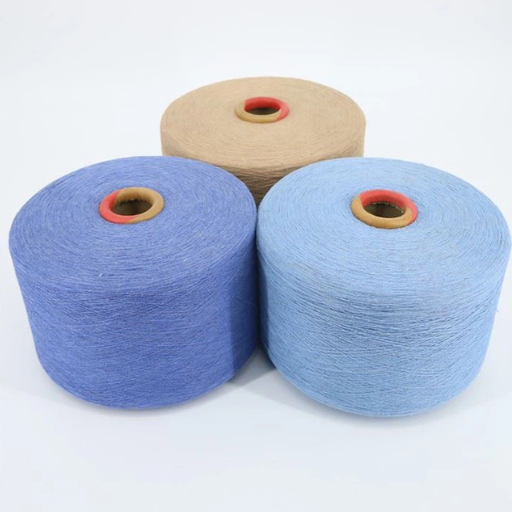
Producing polyester fabric from yarn entails combining either weaving or knitting processes. In most cases, the polyester yarn is prepped by twisting or texturizing which provides the yarn with better strength, elasticity, or aesthetic appeal. Once preparation is done, the yarn is woven into fabric by either interlacing the threads at right angles or using the looping method in knitting. After finishing, the fabric can be dyed, heat-set, or coated to provide color, durability, or water-resistance. Altogether, these are quick methods of creating the multi-purpose and high performance polyester fabrics designed for numerous uses.
Processes Involved in Converting Yarn to Fabric
There are several steps involved in transforming yarn into fabric, each of which is designated for the production of a specific textile. The following is a brief description of the elementary steps involved.
Preliminary Steps: Spinning, twisting, and texturing are only a few of the processes implemented when preparing the yarn. These processes ensure that the particular yarn is feasible in regards to strength, texture, and elasticity. Such a step is an essential contributor towards provision of a durable and uniform base in fabric in the future.
Weaving/Knitting: The yarns are either knitted or woven, depending on the requirement of the fabric. Weaving is the procedure that incorporates the intertwining of vertical and horizontal threads using a loom. This technique is the most effective in terms of producing hard-wearing and structured fabric. Knitting, in contrast, incorporates the looping of yarns to produce softer, more stretchable fabrics usually seen in garments, or other flexible textiles.
Finishing Treatment: A fabric has to be subjected to various processes so that it can attain certain functional and aesthetic qualities. This phase includes dyeing for a vibrant color, heat setting for stability and absence of wrinkles, and coating for water-resistance and stain resistance among other specific traits.
With such workflows, accuracy and flexibility are achieved, resulting in the production of fabrics catering to several domains like fashion and industrial applications. The development of technology has also made these processes simpler and more efficient when it comes to fabric production.
Characteristics of Fabric Made from Polyester Yarn
The fabric created from polyester yarn is tough and can be used for a range of purposes. For everyday clothing and sturdy pieces, polyester is ideal because it is stretchable, does not shrink, and is wrinkle resistant. Its ability to quickly moisture-wick and dry further increases comfort, especially for active and outdoor wear. In addition, this fabric’s resistance to most chemicals and abrasion adds to its use in industrial textiles, contributing to its widespread use. Additionally, polyester yarn can readily be blended with other fibers, for instance, cotton, which makes it possible to produce fabrics with soft and breathable qualities. These reasons, along with low cost, give an explanation how, and why, polyester based fabrics are so widely diffused both in fashion and functional intertwined contexts.
The Role of Polyester in Modern Textile Manufacturing
Polyester plays a crucial role in modern textile manufacturing due to its exceptional adaptability and cost-effectiveness. Its synthetic origin allows manufacturers to produce it in massive quantities while maintaining consistency in quality. Polyester fibers serve as a backbone in producing lightweight, durable, and versatile fabrics for a wide range of applications, from clothing and upholstery to industrial products. It is often blended with natural fibers like cotton to improve the performance of fabrics, offering enhanced durability, wrinkle resistance, and ease of care. Additionally, polyester supports sustainable textile practices, as it is recyclable and increasingly made from post-consumer materials such as plastic bottles, contributing to waste reduction. Its versatility and widespread availability make polyester an essential material in addressing the demands of innovative and sustainable textile solutions in today’s market.
References
Frequently Asked Questions (FAQ)
Q: How is polyester fabric made?
A: Polyester fabric is made through a chemical reaction involving coal, petroleum, air, and water. The primary raw material, ethylene, is derived from petroleum, which is then polymerized to create polyester polymer. This polymer is melted and extruded to form fibers that are woven or knitted into polyester fabric.
Q: What raw materials are used in the production of polyester yarn?
A: The primary raw materials used in the production of polyester yarn are ethylene derived from petroleum and air and water. The process involves creating polyester polymer through polymerization, which is then melted and extruded to form fibers.
Q: How is polyester yarn produced?
A: Polyester yarn is produced by melting polyester polymer and extruding it through a spinneret to create long fibers. These fibers are then cooled, stretched, and wound into spools of yarn, ready for use in fabric production.
Q: What is the role of PET polyester in fabric manufacturing?
A: PET polyester, or polyethylene terephthalate, is a type of polyester polymer used in the manufacture of polyester fabrics. It is prized for its strength, durability, and resistance to stretching and shrinking, making it ideal for fabric production.
Q: Why is polyester considered a synthetic fiber?
A: Polyester is considered a synthetic fiber because it is made from petrochemical sources through a man-made process. Unlike natural fibers such as cotton or wool, polyester is derived from petroleum and created through chemical reactions.
Q: What are the environmental impacts of polyester production and use?
A: The production and use of polyester contribute to environmental concerns due to its reliance on petroleum, a non-renewable resource. Additionally, the manufacturing process generates emissions, and polyester is not biodegradable, leading to waste management challenges.
Q: How is polyester fabric used in different industries?
A: Polyester fabric is used in thousands of different applications across industries. It is commonly used in apparel, home furnishings, industrial textiles, and automotive upholstery due to its durability, versatility, and cost-effectiveness.
Q: Can polyester be blended with other fibers?
A: Yes, polyester is often blended with natural fibers like cotton to combine the benefits of both materials. Blended fabrics offer improved durability, comfort, and reduced wrinkling compared to materials made from a single fiber type.
Q: What is the significance of the demand for polyester in the textile industry?
A: The demand for polyester is significant in the textile industry due to its durability, affordability, and versatile properties. Polyester is a synthetic fabric that offers a cost-effective solution for producing a wide range of textile products, meeting the needs of various consumers and industries.