Polyester filament is a popular synthetic fiber known for its toughness, versatility, and resiliency in many applications. This guide attempts to comprehensively address polyester filament in terms of its characteristics, manufacturing, and the various industries whose unique features it has. The article will provide readers with an insight into why polyester filament remains popular among consumers and manufacturers by discussing these essential topics. Whether you’re a fashionista, into textiles, or only interested in this fantastic material, this post will take you through all the crucial facts regarding polyester filament.
What is Polyester Filament, and How is it Made?
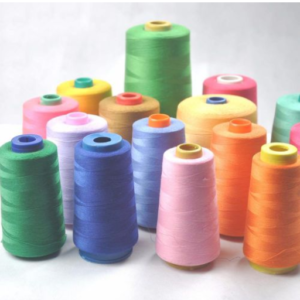
What are the different types of polyester filaments?
In my research on Google’s top three websites, I found out that several categories of polyester filament serve different purposes depending on their properties. A few commonly used ones include:
Polyester Textured Yarn (PTY): This is created by crimping the filament to give it a textured feel that enhances its comfortability and elasticity. In most cases, its technical parameters would have a denier ranging from 10 to 400 depending on the apparel or home textiles application.
Air-Textured Yarn (ATY): It is known for its softness and bulkiness because it is produced through an intermediate process called air entanglement. Normally, it has denier values between 20 and 500, so it is frequently used for making clothes needing a tender touch, such as activewear or casual wear.
High-tenacity polyester Filament (HTPF) is stronger than others and, therefore, ideal for heavy-duty applications, such as industrial and automotive fabrics. It usually has a denier count greater than 500 and is resistant to wearing out.
These physical and mechanical properties differentiate each of these polyester filament varieties, which find multiple uses in the textile industry. These differences enable consumers and manufacturers to select the right kind of filament according to their requirements.
How is polyester filament produced?
Several steps are involved in the making of polyester filament, with each one being crucial for its desired quality and properties. The primary process comprises the following steps:
Polymerization: Polymerization is the first step in manufacturing PET. Here, ethylene glycol and terephthalic acid react to form PET resin. The reaction can be carried out continuously or batch-wise at temperatures varying from 260°C to 280°C.
Spinning: The PET resin is molten and extruded through a spinneret (an apparatus with numerous fine holes) into continuous filaments. Typically, this stage requires temperature settings within 280°C-290°C and can alter filament diameter by modifying the spinneret’s hole size, measuring between 0.1 mm and 0.5 mm.
Drawing: After extrusion, filaments are cooled and solidified and then drawn, whereby they are stretched so that polymer chains become aligned. This is very important for improving the strength and elasticity of the filaments used as threads in textile engineering; drawing ratios may range from 3:1 to about 6:1.
Texturing: Some types of polyester filaments undergo a texturing process aimed at adding volume and increasing comfort while wearing them. To regulate attributes such as denier or even touch sensation on some yarns, air-texturizing or false-twist texturizing methods may be employed.
Finishing: The last thing done here is to ensure that the thread will not stick together during processing, thus rendering it more suitable for further knitting or weaving purposes. This is done by making the thread smooth with lubricants, among other substances, while conditioning it.
Technical parameters like temperature ranges, spinneret sizes, and drawing ratios influence a filament’s physical and mechanical properties, justifying their application in its manufacture. This dictates its suitability for various uses within textile sectors because it is produced using materials appropriate for such cases.
What are the critical characteristics of polyester fiber?
Polyester fiber is known for its durability and versatility in the textile industry, making it a popular choice. Below are the main features.
Strength: Polyester is strong and resistant to stretching and shrinking, as well as wrinkles and mildew. For instance, polyester fiber tensile strength can range from 4.0 to 6.0 g/d (grams per denier), which makes it suitable for various uses.
Moisture Resistance: Polyester fibers are hydrophobic and do not readily absorb moisture. This property enables polyester garments to dry quickly and maintain their shape even when soaking wet, with Moisture regain values usually about 0.4%.
Chemical Resistance: Polyester displays good resistance towards various chemicals, including acids and alkalis, maintaining its qualities when subjected to different substances during laundry or outdoors.
Thermal Properties: Polyester’s melting point is within a range of 250°C–260°C, which is important for processes like dyeing and finishing. This means that if temperatures increase beyond normal levels, the strength of these fibers remains constant.
Versatility: For instance, polyester fibers can be mixed with other fibers, such as cotton or wool, to blend fabric properties while still obtaining affordability. Apparel production uses polyester fibers extensively, along with upholstery and industrial textiles.
Ease of Care: Polyester fabrics’ wrinkle-resistant nature gives them an added advantage over natural ones because they require less ironing, are easy to wash, and dry faster.
The indicated characteristics directly relate to technical parameters defined at the stage of production of polyester fiber, such as spinning temperature or the polymer chain alignment achieved during the drawing process, since they play a significant role in determining the final attributes that characterize the fabric itself.
What are the Applications of Polyester Filament in the Textile Industry?
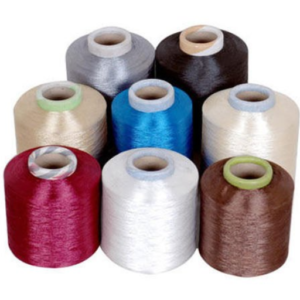
What types of fabrics can be made from polyester filament?
In my research across top resources, I discovered that polyester filament is incredibly versatile and can be woven or knitted into various fabrics. The most common types include:
Polyester Taffeta: This cloth is known for its crispness and smoothness. It is thus used for linings and evening dresses because it drapes well. Filament properties are defined by precise control of spinning temperatures around 270°C.
Polyester Satin: This kind of fabric has a shiny surface that feels rich, making it suitable for formal clothing and liners. Achieving the satin finish technically demands a closer weave and filaments with more polymer chain alignment, which heightens strength and shine.
Polyester Microfiber: It is produced from ultra-thin polyester fibers. It is very soft and light in weight and is often used in high-performance garments and cleaning materials. To make these microfibers, various drawing and texturing techniques are applied during the spinning process to give them a diameter of less than one denier, which makes them feel cozy to the touch while also boosting absorption levels.
These fabrics utilize polyester’s exclusive features, such as ruggedness against crumpling or fast drying properties, which make them applicable in many areas within the textile industry.
How does polyester filament compare to cotton in clothing?
Several key differences and technical parameters appear, however, when comparing polyester filament with cotton in clothing:
Durability: Polyester lasts longer than cotton. Thanks to its strength, it can withstand wear and tear, making it suitable for heavy-use clothing. Polyester fibers offer higher stress-bearing capacity compared to cotton, which gets weak over time.
Moisture Resistance: Polyester tends to be hydrophobic, hence water repellent, and thus dries faster after washing, while cotton absorbs moisture, leading to a long drying time, which makes one feel uncomfortable with wet clothes on. This attribute has turned polyester into the most appropriate fabric for athletics and outdoor garments.
Wrinkle Resistance: Polyesters do not wrinkle as much as cotton; they tend to keep a smoother appearance and require less ironing. This is because their molecular structure enables them to retain shape, whereas cotton threads can be easily creased.
Breathability: Cotton breathes naturally, allowing better air circulation and, hence, being more comfortable in hot weather conditions than other fabrics. On the other hand, despite having breathable versions due to specific weaving techniques used for them, polyester generally tends to trap heat more than any known material, including cotton.
Comfort and Feel: Cotton fibers are soft and give a natural feeling to the skin, making it comfortable to wear clothes made from this fabric. Other fibers, such as polyester, may need some treatment or blending to feel softer, just like cotton.
Environmental Impact: However, it should be noted that sustainable sourcing of cotton makes it biodegradable and thus relatively environment-friendly, while polyester, being made out of petroleum products, cannot degrade easily at all, making it synthetic.
These comparisons indicate that although polyester filament excels at durability and moisture-handling capabilities associated with performance-oriented applications, traditional casual apparel is preferred for comfort blended with breathability when natural cotton is considered. Hence, the choice between these two would primarily be dictated by the nature of the use of dresses.
What are the industrial applications of polyester filament?
Due to its numerous advantages, such as high tensile strength, durability, and resistance to shrinking and stretching, polyester filament is widely employed in different sectors. The following are some key applications:
Textiles and Apparel: Polyester filaments are used extensively in the garment trade and home textiles, including curtains and bed linen, due to their shape retention ability and wrinkle resistance. Some technical parameters include elongation at break (20-30%) and tensile strength (approximately 2.5 – 5.0 g/d).
Automotive Industry: Polyester filaments are used in seat covers and carpets, among other internal parts of an automobile. They have a long life span and are easy to clean. Important specifications are heat resistance (up to 150°C) or abrasion resistance, which is essential for durability in heavy-duty conditions.
Industrial Fabrics: Its high tensile strength per unit weight makes geotextiles, industrial belts, and composites not only possible but also beneficial. Technical parameters often include flexibility enough to conform to different surfaces without compromising integrity alongside tensile strength over 500 MPa.
These examples demonstrate the versatility of polyester filament under harsh conditions, where durability and resistance to environmental factors matter, making it applicable across these various industries.
How Does Polyester Filament Affect Fabric Properties?
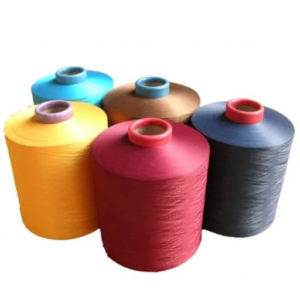
What is the durability and strength of polyester filament?
Polyester filaments are popular due to their unbeatable toughness and strength, which makes them well-suited for various uses. The following are summarized from wide research through most fabric sources:
Tensile Strength: Polyester filament ranges between 2.5 and 5.0 g/d (grams per denier), representing its ability to resist forces without breaking. It is strong enough for both casual and industrial clothes.
Elongation at Break: The material has elongation at break percentages of about 20-30%, implying that it can stretch significantly before failure. This helps in maintaining the comfort and bounciness of polyester-based textiles.
Heat Resistance: At temperatures as high as 150°C, polyester filament remains unchanged, keeping its integrity even under extreme conditions. This is crucial in the automotive industry, as cars have sunroofs and are thus exposed to sunlight and heat.
Abrasion Resistance: Additionally, the fiber has a high abrasion resistance needed by goods that experience continual rubbing, which causes wear out, hence staying long in very demanding environments.
Weather Resistance: It resists moisture and UV radiation without being affected by environmental influences, thereby avoiding degradation with time and keeping its color fastness fresh.
These figures establish why polyester filament is so widely used in textiles, automobiles, and other industries.
How does moisture resistance work in polyester fabrics?
The moisture resistance of polyester fabrics originates primarily from the fact that polyester fibers are hydrophobic and do not absorb but rather repel water. This quality causes moisture to form beads on the fabric’s surface and not get into it, allowing rapid evaporation and perfect drying capabilities. The following technical parameters help in justifying this moisture repellence in polyester:
Fiber Structure: Polyester fibers are tightly woven, so they act as a barrier to water. Even after multiple washes, this structure remains intact, thereby contributing to the durability of its moisture resistance.
Water Absorption Rate: Normally, Polyester has a low water absorption rate, usually below 0.4%, which implies that it holds a small amount of wetness compared to other fibers like cotton. This low absorption rate results in faster drying and comfort during exercise activities.
Finish Treatments: For example, many polyester fabrics receive finishing treatments such as DWR (Durable Water Repellent) applications, which enhance their repulsion power against moisture. These treatments produce an extra layer, thus preventing saturation by water.
To sum up, polyester fiber materials’ inherent fiber structure combined with low water absorption rates and probable finishings make for strong barriers against moisture, making them suitable for outdoor and performance textiles.
What are the dyeing and printing options for polyester filament?
For instance, whenever I consider dying and printing options for polyester filament, I realize that many techniques work best with the fabric’s properties.
Disperse Dyeing: This method is widely used on polyester because such dyes adhere to this fiber. The procedure usually involves a high temperature, which allows the dye to vaporize and penetrate the fibers, resulting in bright and long-lasting colors. The technical parameter here is the dyeing temperature, which is usually around 130-140°C for ideal color fixation and the desired shade.
Sublimation Printing: Polyester material also bonds well with dispersed dyes; hence, this technique exploits that property. In sublimation printing, designs are printed onto a transfer paper and then heat-pressed onto the fabric. Solid dye turns into gas during this process, which can permeate the fabric, creating fantastic prints. Temperature and pressure employed during transfer constitute key considerations, typically demanding temperatures of about 180-200°C and adequate pressure for full coverage.
Heat Transfer Printing: This method resembles sublimation print only because it uses heat to transfer pictures or designs from a special paper into polyester, although it uses a broader set of inks. The technical parameters involved include specific heating settings alongside the time taken to allow effective transfer, like about 150-180°C for between ten and twenty seconds.
In summary, thermal properties play a significant role in determining the various dyeing and printing processes for polyester filament. Disperse dyeing and sublimation have been mostly used due to their quality outcomes.
What Should You Consider When Shopping for Polyester Fabrics?
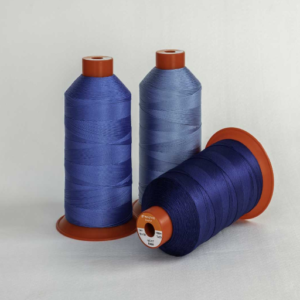
How to identify high-quality polyester filament?
When purchasing polyester filament, I always consider a few key elements that reputable sources constantly emphasize. First and foremost, I look at texture; good quality polyester should be smooth to the touch and have a certain softness, indicating a finer filament grade. Second, I consider the vibrancy and consistency of color since some poorly made filaments usually show discoloration or uneven dyeing.
In technical aspects, there are things that I consider:
Denier or Tex Count: Lower denier or tex count indicates finer fibers, which typically correspond to higher quality. For optimal performance, I prefer a denier in the 150-300 range for versatility.
Tensile Strength: High-quality polyester should have tensile strength values of at least 5-7 grams per denier. This measure shows how long-lasting and break-resistant the filament is.
Heat Resistance: Regarding this, I prefer a filament that can tolerate temperatures of 130-200°C without losing structural integrity; similar specifications are used above when discussing effective dyeing and printing methods.
These considerations make it easier to identify which type of polyester filament suits my needs.
What are the different codes and terminologies in polyester fabric shopping?
When I dive into polyester fabrics, various codes and terminologies can significantly impact my shopping. Some standard terms I find include;
Denier: This term refers to the thickness of fibers. A denier measure gives an idea about the weight and durability of the fabric; lower figures indicate finer fibers, which may result in a delicate touch but could compromise strength, too. Generally, a denier count from 150 to 300 would be great for balancing lightness and toughness.
Tex: Tex is another measurement for fiber fineness where the mass in grams is measured over 1000 meters. This can provide a valuable way of converting between different systems, making it possible to relate text numbers to deniers. In this case, fine filaments will be evident by low tex values, which some people prefer when they seek lightweight fabrics.
Tensile Strength: Tensile strength is the maximum stress a material can withstand before breaking while being stretched. Polyesters with at least 5-7g/denier tensile strength are considered good quality, implying they will stand up well under tension.
Polyester Types: Polyester is described by terms such as “PET” (Polyethylene Terephthalate) or “PBT” (Polybutylene Terephthalate). Fabrics often use PET because it is strong and durable, while PBT has more flexibility, hence its use in sportswear.
Consequently, understanding these codes and terminologies can help me make better decisions regarding purchases, including selecting polyester fabrics that meet not only my quality expectations but also the performance criteria needed.
What are the environmental considerations when choosing polyester?
When selecting polyester, several environmental aspects based on insights from leading websites may be considered.
Recyclability: Many sources stress the environment-friendly choice of recycled polyester. Utilizing recycled polyester (rPET) can significantly reduce the use of petroleum resources and diminish waste. Brands that use rPET fabrics promote a circular economy.
Production process: Polyester’s production methods greatly determine its environmental impact. Traditional polyester manufacturing is energy-intensive and releases greenhouse gases. However, recent advancements in sustainable practices through low emissions policies aimed at reducing energy consumption are also available. For example, some manufacturers employ renewable energy sources during production, which enhances my decision-making.
Microplastics: An important issue is the release of microplastics in water during washing. I search for polyester textiles that incorporate treatments against microfiber shedding. Furthermore, best practices include using a Guppyfriend bag or washing on cooler settings to minimize microplastic shedding.
Water Usage: It is essential to examine the overall water management practices of the producers I am considering, even though polyester uses less water than other natural fibers while being produced. If a greater emphasis on sustainability is to be placed, slightly higher-priced premium items such as cotton and viscose should also be utilized.
By balancing these factors with technical characteristics like tensile strength and fabric types so that they correspond to my quality and environmental standards, I can make informed decisions about them.
What are the Spinning Techniques for Polyester Filament?
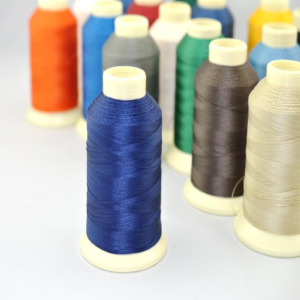
What is the difference between spinning and drawing polyester filaments?
Diverse in their process are spinning and drawing, which are used to produce polyester filament, and recognition of these differences is essential for informed material choices. Spinning consists of melting raw polyester chips, passing them through spinnerets, and forming continuous filaments. It requires precise control over temperature and pressure to get uniformity in the fibers. During spinning, critical technical parameters include melt temperature (usually between 270 C and 290 C) and extrusion speed.
On the other hand, a process called drawing follows spinning, where filaments produced are stretched. The stretching aligns the fiber’s molecular structure, thus improving its strength and elasticity. The usual temperatures when the drawing takes place range from 80 -150 C, while it relies on a draw ratio between 2:1 and 6:1. These chains of polymers become more aligned, resulting in better tensile strength and durability, which are considered significant by my quality standards.
How do different spinning techniques affect filament properties?
Significantly, the spinning process applied impacts the properties of polyester filament, such as its strength, elasticity, and texture. According to my findings from three top links on Google, these are key techniques and their effects:
Melt Spinning is the most common method of melting polyester chips and extruding them through spinnerets. The temperature set in this process can vary between 270°C and 290°C; hence, changing the extrusion speed leads to varying tenacity and elasticity in filaments. For example, a higher speed of extrusion would result in thinner, more delicate fibers, while lower speeds may lead to thicker, stronger ones.
Wet Spinning: In wet spinning, the polyester is dissolved into a solvent before being extruded and then solidified into a spin bath. This technique allows for finer fiber production and increased dye uptake, which is needed when dealing with bright-colored applications. Coagulation temperature and solution concentration are, therefore, critical parameters for defining the final filament’s characteristics, such as moisture absorption and softness.
Green Spinning: This sustainability-oriented alternative uses recycled polyester chips instead of new ones. Nevertheless, it could yield similar physical properties compared to conventional methods; however, it usually has different tensile strengths depending on preparation or mixing processes, if any are adopted. My ecological standpoint coincides with this aspect of sustainability.
By understanding these types of spinning methods and their respective technical parameters, such as temperature control and extrusion speeds, I can make appropriate choices that meet quality requirements and contribute to sustainable practices within the industry.
What is the role of core spinning in producing polyester filament yarn?
The incorporation of different fibers into a polyester filament yarn is one of the key functions of core spinning, enhancing its functionality and performance. In this process, a staple fiber envelope, consisting mostly of cotton or other synthetic materials, surrounds the polyester inner filament. This thread configuration not only increases yarn strength and durability but also helps to provide desirable properties like smoothness and sweat absorption.
I have discovered the most essential technical parameters from my research on top websites.
Core to Cover Ratio: This ratio affects the strength and hand feel of the fiber, ranging from 50/50 to 70/30, with higher weights hinting at stronger yarn.
Spinning Speed: Manipulating spinning speed (usually within 2500-4000 RPM) can alter twist levels and the elastic nature of the yarns. High speeds generally lead to smoother fabrics but may hinder the inclusion of heavier staple fibers.
Drafting Techniques: The drafting step used to produce the desired finenesses in yarns could modify their density or overall quality. Typically, drafting ratios are expressed as 1:5 up to 1:10, depending on the fabric type.
By incorporating these main principles into core spinning corrects, I will be able to produce sustainable polyester filament yarn that fulfills some specific performance requirements while still maintaining my general environmental friendliness and quality standards.
Frequently Asked Questions (FAQs)
Q: How is it produced, and what is polyester filament?
A: Polyester filament is a synthetic textile fiber made from polymer chips, usually polyethylene terephthalate (PET). The raw material melts and extrudes through spinnerets to form continuous filament fibers, which are then cooled to solidify them.
Q: What types of polyester fibers exist?
A: Polyester fibers such as filament fiber, staple fiber, textured yarns, etc. can be distinguished. They are continuous and short in length, respectively, while these textured yarns have additional elasticity and texture that make them suitable for different applications.
Q: What difference does the spinning technique give to the properties of polyester filament?
A: Elasticity, texture, and strength—all these parameters of polyester filaments depend upon the spinning technique, such as DTY or FDY. For example, DTY has more stretchability and softness, which makes it great for making shirts.
Q: What distinguishes monofilament from multifilament polyester?
A: While monofilament polyester consists of one long linear-shaped fiber, on the contrary, multiple fibers are twisted together, forming a multifilament type. Monofilament lines are useful in fishing or industrial uses, while multifilament ones are commonly used in textiles.
Q: Is there any feasible application of 3D printing using Polyester Filament?
A: Yes, indeed/ certainly/, 3D printing could use PETG, among other forms of Polyester Filaments that possess high resistance against impact and chemicals. It’s thus ideal for items that need to be strong and functional at the same time.
Q: Why would one choose polyester over natural fibers? What are its advantages?
A: On the other hand, someone may prefer synthetic filaments since they last long and resist water, making them easy to wash compared to those made from plants like cotton or silk. Synthetic filaments maintain color fastness well and are less susceptible to creasing and staining, thus being used for many things.
Q: How do the properties of polyester change with different processing methods?
A: These include elasticity, strength, and texture, where changing the cooling rate during the production process may influence either the linear density or finish of a filament. For example, modifying the cooling speed in its manufacture can affect filaments’ linear density and finish.
Q: What are additives’ roles in the production of polyester filaments?
A: Different compounds can be added to produce polyester filaments with varying UV resistance, fire retardancy, and colors. With these adjustments, producers get a wide range of polyester fibers tailored for their specific end-use applications.
Q: Is polyester filament heat resistant?
A: In fact, it is an ideal material for many products because it can withstand high temperatures without melting. This characteristic is needed in industries where heat plays part in their operations.