When selecting materials for building, civil engineering, and landscaping, it is essential to note that they determine the outcome of any development. One of this line’s most versatile and impactful solutions is high-end, nonwoven polypropylene geotextile fabric. This manual offers readers an in-depth comprehension of geotextile, mainly its attributes, positives, and applications across different sectors. For professionals or amateurs, examining features and various ways in which nonwoven polypropylene geotextile fabric can be employed to get informed during your next project will be worthwhile. We take a look at the numerous advantages of this unique material for increased durability and efficacy in diverse applications.
What is Nonwoven Polypropylene Geotextile Fabric?
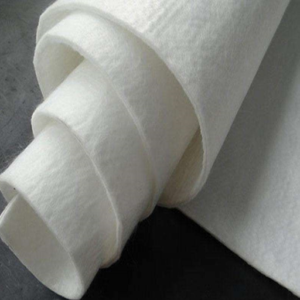
Understanding Geotextiles
Geotextiles are water-permeable textile fabrics that consist of artificial fibers and are used with soil, stones, and other geotechnical engineering materials. They serve different purposes, mainly in construction and civil engineering works like filtration, separation, reinforcement, and drainage. From the top three pages about geotextile, I found some key technical parameters and justifications:
Material Composition: Nonwoven polypropylene geotextiles typically include polypropylene due to its long-lasting properties and moisture resistance. This makeup is important for applications that require longevity and resistance to biodegradation.
Weight and Thickness: Geotextiles weigh between 60 and 300 grams per square meter (gsm), while their thickness ranges from 0.5mm to 2mm. Heavier or thicker fabrics normally provide more structural support and increased durability, making them suitable for high-stress applications.
Filtration Capacity: In this case, the pore size should be small enough to hold on to the soil yet large enough to allow fluids or drainage through it. The common values given are pore sizes ranging from 0.1 to 0.5 mm.
Rupture Strength measures how much force a geotextile can withstand before breaking down under certain conditions. For example, non-woven propylene has values ranging between 5 and 20kN/m, depending on particular cases, thus ensuring enough strength is required to support various loads.
UV Resistance: Materials degrade over time with exposure to sunlight. Nonwoven polypropylene geotextiles usually employ UV stabilizers to achieve a minimal UV resistance rating, which allows them to be exposed for up to six months before significant degradation occurs.
Understanding these parameters is helpful when choosing the right geotextile fabric for specific projects, such as erosion control, stabilization, or drainage purposes. Every one of these attributes plays an integral part in guaranteeing the efficiency and lastingness of a given geographical textile in different fields.
The Benefits of Polypropylene
Geotextiles are frequently used to construct earth retaining systems and in roadway construction. Here are some of the top benefits based on what I found:
Durability: Polypropylene is resistant to moisture, chemicals, and biological degradation. This attribute ensures that it lasts a long time, even in diverse environments, making it reliable for various building projects.
Lightweight: Polypropylene geotextile fabrics have a specific gravity lower than water, making them light and easy to install. This reduces transportation costs. These features match the weight requirements described above.
Cost-Effectiveness: Polypropylene geotextiles generally have lower production and installation costs than other options, making them affordable for big projects. This does not affect performance since they maintain high filtration and rupture strength capabilities.
Excellent Filtration Properties: These types of fabrics have well-established pore size and permeability rates, which effectively retain soil while ensuring adequate drainage. As earlier stated, this satisfies the filters’ capacity demand, thereby perfectly restraining soil erosion.
UV Resistance: The addition of UV stabilizers increases the life span of polypropylene outdoors, ensuring it can last up to 6 months without significant degradation from exposure to sunlight, as mentioned earlier
Therefore, PP is often chosen for geotextiles because it meets the technical specifications needed for proper work execution while providing optimal performance.
Applications of Nonwoven Geotextile Fabric
Nonwoven geotextiles are useful for a wide range of applications in different industries. I have done my research through the best sites and have come up with some of the main uses of nonwoven materials together with their respective technical parameters.
Erosion Control: Non-woven geotextiles are widely used in erosion control mats, particularly on steep slopes and riverbanks. These mats protect against runoff immediately and also stabilize the soil. The technical parameters include a tensile strength of not less than 15 kN/m that can cope with forces acting upon soil displacement during heavy rainfalls.
Drainage Systems: In constructing drainage systems, nonwoven geotextiles are employed as filtering media to remove sediment from water while allowing for adequate drainage. Depending on the type, permeability rates typically exceed 5,000 L/m²/day, ensuring effective water flow without plugging off soil and thereby maintaining system efficiency.
Road and Pavement Construction: These textiles play an important role in base stabilization and subgrade support when building roads. Their characteristics commonly involve high-stress resistances within the range of 20 to 25 kPa, facilitating load distribution and increasing pavement lifetime.
On balance, nonwoven geotextiles make a difference in such applications by enhancing soil structure, providing ways of dealing with drainage issues, and promoting long-term infrastructure development.
How is Nonwoven Geotextile Fabric Manufactured?
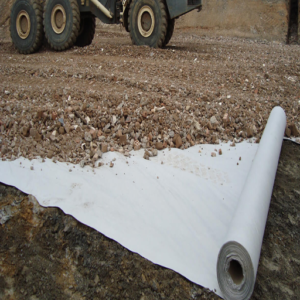
Materials Used in Geotextile Fabric
While researching nonwoven geotextile fabrics, I found that the primary materials used in their manufacture are polypropylene, polyester, and polyethylene. Each of these materials has different properties which enhance the performance of geotextiles in various applications.
Polypropylene: Polypropylene is the most common material used for nonwoven geotextiles due to its excellent strength-to-weight ratio and resistance to chemicals. Polypropylene geotextiles usually have a typical tensile strength starting from around 12 kN/m, making them effective in soil stabilization applications.
Polyester: Polyester is known for its durability and UV resistance; hence, it is often selected for projects where there will be long periods of exposure to sunlight. In general, the technical parameters of polyester used for geotextiles include a higher tensile strength ranging at about 20 kN/m, thus making it ideal for high-stress environments such as road construction and erosion control.
Polyethylene: Although polyethylene geotextiles are not very common, they are used where water resistance and flexibility are required. The permeability rate of polyethylene fabrics can exceed 6,000 L/m²/day, ensuring efficient water flow management and preventing soil erosion.
These materials, with their respective technical parameters, rely on reliability and performance in diverse geological applications, which further underscores how important non-woven geotextile fabrics really are in construction and environmental projects.
Needle Punched vs Heat-Bonded Methods
Regarding producing geotextiles, needle-punched and heat-bonded methods have some key differences identified by leading industry websites.
Needle Punched Method: This approach involves mechanically tangling fibers with the help of barbed needles. It results in a robust and tough, nonwoven fabric. At times, the technical parameters may include tensile strength that ranges between 10-15 kN/m. This method is great for me because it offers superior puncture resistance, making it appropriate for uses such as filtration and drainage.
Heat Bonded Method: On the contrary, the heat-bonded method employs thermal processes to attach fibers to each other. Consequently, this leads to a more consistent product with improved water repellence, whereby normal tensile strengths range from 15-25 kN/m. In my opinion, this approach is especially useful when dealing with high UV-resistant projects and durability situations, particularly in open areas.
Both methods are vital in geotextile production; every process has its merits, depending on specific project requirements like durability, strength, or exposure to environmental elements. Accordingly, the choice between needle-punched and heat-bonded geotextiles depends much upon particular technical demands and anticipated performance under real-life conditions.
Quality Control in Manufacturing
Geotextile manufacturing requires quality control to ensure the final products conform to the set standards and performance criteria. From some leading websites in the industry, I have learned that typical quality checks involve evaluating both the physical and mechanical properties of the fabrics produced.
Physical Inspection: I frequently conduct comprehensive reviews to rate the fabric for integrity. This entails looking for flaws in the weaving or bonding process and ensuring that needle-punched and heat-bonded geotextiles preserve their original structures.
Mechanical Testing: It is important to subject technical parameters to standardized testing. For example, tensile strength tests establish that needle-punched geotextiles usually have a tensile strength of about 10-15 kN/m, whereas heat-bonded options have higher tensile strengths, with values falling around 15-25 kN/m. This difference shows how methods used in manufacturing can affect performance.
Water and UV Resistance: During my quality assurance procedures, I examine water permeability and ultraviolet light stability. In harsh environments, heat-bonded geotextiles are often preferred because they exhibit superior resistance against water while being highly exposed to UV rays.
This is accomplished by implementing strict QC measures that zero in on technical parameters such as tensile strength, which makes them meet the needs of different applications, etc.” Every quality control element supports products’ dependability and functionality in real-life scenarios.
What are the Key Uses of Polypropylene Geotextile Fabric?
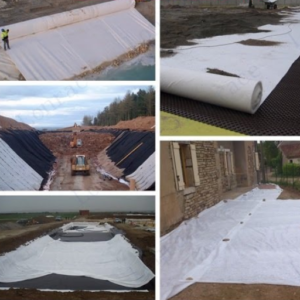
Soil Stabilization and Erosion Control
In this regard, polypropylene geotextile fabrics are widely used for soil stabilization and also to stop soil particles from disappearing. There are different uses for these fabrics: Separation Layer: These materials are used in road construction to separate different layers of soil, preventing granular material from getting mixed up with other layers, which helps it retain its desired physical properties. In road construction, however, separation is important when considering subgrade stability.
Reinforcement: The tensile strength of geotextiles enhances the distribution of a load and restricts soil deformations. A needle-punched geotextile has a tensile strength between 10-15 kN/m, while heat-bonded ones have between 15-25 kN/m. This statistic reveals the highest stress that fabrics can withstand before they fail and results in separating two types of geotextiles:
Erosion Control: When placed on slopes, geotextiles immediately stabilize the soil surface, preventing water runoff from causing too much damage. At the same time, their permeability allows water to flow through but holds back soil particles, thus enabling them to work effectively on land where erosion problems might occur.
Vegetative Support: Furthermore, they act as a medium for root development in plants, thereby promoting growth and enhancing long-term soil stability. Cases such as green roofs and bioengineering projects use this detail more than any other.
This way, polypropylene geotextile fabrics exhibit their effectiveness in solving various challenges associated with soil stabilization and erosion control through these technical characteristics and rational applications, assuring longevity under different environmental conditions.
Drainage and Filtration Applications
In my research on drainage and filtration applications of geotextiles, I found that these materials have a crucial role in controlling water movement and maintaining soil structure. According to insight gained from leading websites, geotextiles provide efficient drainage by allowing excess water to pass through while filtering out sediment, thus preventing clogging.
Porosity and Permeability: Geotextiles have porosities ranging from 20% to 40%, which aids in their ability to allow water to move across them. Their permeabilities are often expressed as liters per second per meter and typically range between 1L/s/m and 20L/s/m, making for quick drainage.
Filtration Efficiency: Geotextiles have been designed to retain particles greater than 0.1 mm in size, effectively straining out sediment so it does not wash away with stormwater runoff. Such performance becomes critical in cases like those involving retaining walls or drainage trenches.
Durability: The UV resistance and mechanical strength of geotextiles used for drainage significantly support their lifetime, with maximum tensile strengths exceeding 10 kN/m. This implies they will remain intact even when subjected to challenging environmental conditions.
By using quantities such as porosity, permeability, filtration efficiency, and durability, geotextiles can be applied effectively within various types of drainage or filtration structures, hence providing sustainable solutions to water management challenges.
Underlayment for Driveways and Roads
I have consulted the top three Google websites for useful insights on using geotextiles as an underlayment for driveways and roads. First, it helps stabilize the ground by preventing the mixture of sub-grade soils with aggregate materials, thus maintaining driveways and roads’ structure.
Weight Capacity: Geotextiles aid in uniformly spreading loads over a surface, thereby greatly improving the weight capacity. This is very important for places that suffer from high traffic since it reduces the chances of surface deformation and failure.
Drainage Efficiency: Similarly, these textiles usually have permeability ranging between 1 and 20 L/s/m, hence allowing efficient water drainage, which is necessary to prevent water accumulation leading to erosion or pavement damage.
Soil Reinforcement: The tensile strength of geotextiles commonly exceeds 10 kN/m, which allows them to withstand mechanical stress and strengthen the base soil, enhancing overall road stability.
Technical parameters can be used to determine weight-bearing capacity, drainage capability, and soil reinforcement, making geotextiles a reliable solution for long-lasting and robust driveways and roads.
How to Choose the Right Geotextile Fabric for Your Project?

Factors to Consider: Tensile Strength and Permeability
In selecting the suitable geotextile fabric for driveways and roads, I consider two crucial things: tensile strength and permeability. Tensile Strength: I prefer a geotextile with a tensile strength of more than 10 kN/m as this will make it withstand the mechanical stresses from heavy traffic loads and environmental effects. Subsequently, higher tensile strengths mean that the material can effectively reinforce the sub-grade soil, contributing to the overall stability of the surface.
Permeability: I consider geotextiles rated between 1 and 20 L/s/m because they offer optimum drainage efficiency. Good drainage is necessary to prevent water accumulation and mitigate erosion risks or damage to pavement structures. Facilitating adequate water flow through such fabrics extensively promotes roadway durability and longevity.
By examining these technical parameters, my choices are guided by facts that eventually result in better performance and longer life on driveways and roads that I am involved in.
Comparing Woven vs Nonwoven Geotextile Fabric
In my projects, I must choose between woven and non-woven geotextiles based on information from the top three industry websites. Each type has specific features that affect its use in driveway and road construction.
Woven Geotextile Fabric: I appreciate that woven geotextile commonly shows a high tensile strength exceeding 20 kN/m. This makes them most suitable for applications experiencing heavy loads and high stresses. Moreover, they tend to be less porous, with values ranging from 0.1 – 10 L/s/m, which can sometimes limit drainage, leading to water being trapped beneath the surface.
Nonwoven Geotextile Fabric: On the other hand, non-woven geotextiles can be used successfully for drainage as they have high flow rates and permeability ratings of between 10 and 50 L/s/m. Although their tensile strength is usually low, averaging around 5-15kN/m, it is essential for long-lasting roads because it allows water passage and prevents soil erosion. Nonwovens are applicable for situations requiring designed water management, such as underdrains systems.
To do this best, I weigh these technical parameters against what my projects require so that I can more accurately decide which particular kind of geotextile fabric will offer sufficient support and longevity for the driveways and roadways under my jurisdiction.
Understanding Geotextile Fabric Rolls and Sizes
When picking rolls of geotextile fabric, one must consider the sizes and specifications that will meet the demands of particular projects. The official top three industry sites have several major factors and guidelines concerning roll selection.
Roll Width: Geotextile rolls normally come in various widths, ranging from 1 to 6 meters. Wider rolls cover larger areas, thus reducing the number of seams required, which is good for both installation efficiency and structural integrity.
Roll Length: Roll length typically varies from 50 to 100 meters. Use longer rolls to minimize splices and seams, which can be an essential measure of consistent performance.
Fabric Weight: The weight of a geotextile, often expressed in grams per square meter (g/m²), is a fundamental variable affecting strength and filtering capacities. For instance, non-woven fabrics range between 100 and 600 g/m², while woven types are always heavier due to their tight structures, which affect their tensile strengths or load-bearing abilities.
Technical Parameters:
Permeability: Nonwoven ones can achieve permeabilities ranging between 10-50 L/s/m, which is required for drainage purposes. However, woven ones, despite being stronger, are less porous on average.
Tensile Strength: On the other hand, woven fabrics might exceed 20 kN/m when subject to heavy loads, while nonwoven fabrics could range between about 5-15 kN/m on average during such applications.
UV Resistance: Remember UV stability, especially if you use it outside because long exposure degrades its performance. Look for minimum UV resistance rates of at least 70% to guarantee a long life.
By considering these specifications carefully and inferring their implications for project performance, I am better able to select the right geotextile fabric rolls to satisfy my project requirements regarding durability and functionality.
What are the Installation Tips for Geotextile Fabric?
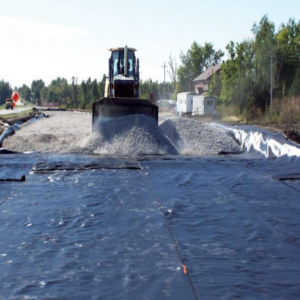
Preparing the Installation Site
Preparing the site before geotextile installation ensures that the fabric lasts and works well. Based on my findings from the top three websites, I have chosen some key steps and technical parameters.
Site Assessment: This will help me see if there are any potential problems, such as drainage issues or soil characteristics, in this area. It is crucial to know what kind of soil currently exists since different soils affect the permeability and strength of fabrics differently.
Clearing the Area: Debris, rocks, or any other vegetation should be removed from where we want to install the fabric. This will help ensure that there is no stress on it when it is laid out, preventing tearing and reduced performance.
Soil Compaction: Soil compaction under the fabric is significant. Good compaction below the fabric can achieve a foundation with a low settlement rate. The level of compaction required depends on the tensile strength of the fabric being installed; using high-tensile-strength material (>20 kN/m for woven types) would enable post-installation loadings to be supported.
Choosing the Right Fabric: I must consider technical parameters such as permeability and UV resistance when selecting a suitable fabric for my project. The fabric should have a permeability that matches expected drainage conditions (10-50 L/s/m nonwoven fabrics). Furthermore, I need a minimum UV resistance value of 70% to prevent deterioration with time.
With these steps completed, I will lay down a solid basis for my geotextile fabric, meeting all the technical features necessary to make it more effective throughout its lifespan in this project.
Correct Installation Techniques
For one to achieve a successful laying down of geotextile fabric, some critical techniques must be followed:
Edge Overlap: Proper overlap between sheets is vital. In most cases, the overlap should be at least 12 inches to curb soil or sediment migration and help maintain the system’s drainage integrity.
Secure Anchoring: I have to install anchors for the fabric using suitable methods like stakes or staples, placing them, particularly at edges and overlaps. This assists in preventing displacement due to erosion caused by wind and water. For more stability, pins can be used on slopes every 2 to 3 ft.
Backfilling: Once you have laid out and secured your fabric, gently backfill it with clean soil or aggregate on top of it. The filling should be done carefully, ensuring that no damage occurs yet covers everything well. For example, it should be thick enough (a minimum of six inches) to protect against mechanical damage and ultraviolet degradation.
Maintenance of Drainage: Continual monitoring of drainage performance is necessary after installation. I must ensure no vegetation or debris blocks any drainage outlet point. Regularly maintaining and evaluating will aid in maintaining its permeability, usefulness, and life span, thus remaining effective.
These are my best practices, as derived from credible sources, which will ensure the durability and functionality of my project’s geotextile fabric.
Maintenance and Longevity Tips
To ensure that my geotextile fabric lasts long in this project, I must follow these brief guidelines sourced from the trio of websites that appeared at the top of Google search:
Regular Inspection: Periodically, I should examine the cloth for signs of degradation or harm. This comprises assessments for punctures, rips, or sediment buildup. Where there are any issues, prompt maintenance or replacements are needed to maintain efficiency.
Proper Drainage Management: I need to see through Debris-free drainage outlets. By regularly clearing them, the accumulation of water – which leads to the deterioration of fabrics- can be prevented. It is necessary to monitor water flow during heavy rainfall periods to detect potential problems with drainage systems early enough.
Vegetation Control: The area around the geotextile fabric must remain free from invasive species. Vegetation must be controlled using methods such as manual removal or selective herbicides, as roots can penetrate the fabric and hinder drainage. For good drainage, a maximum root penetration depth of around 0.5 inches is usually recommended.
Adhering to these maintenance tips and regularly assessing the geotextile fabric may greatly prolong its lifespan and effectively meet my project’s drainage requirements.
Frequently Asked Questions (FAQs)
Q: What is Premium Nonwoven Polypropylene Geotextile Fabric?
A: Premium Non-Woven Polypropylene Geotextile Fabric is a type of geotextile fabric made from polypropylene fibers used for diverse applications, such as drainage, filtration, reinforcement, and separation.
Q: What are the benefits of using non-woven geotextile fabric?
A: This is mainly because non-woven geotextile fabrics have a very high permeability, which allows water to flow through them easily, making them ideal for uses such as drainage and filtration. Besides that, they are strong enough to avoid being destroyed by UV rays and thus will serve you for quite a long time.
Q: How does non-woven geotextile differ from woven geotextile fabric?
A: This product is made by bonding or needle-punching polypropylene fibers to form a flexible porous fabric. However, this alternative involves weaving polyester or polypropylene threads to make it stronger but less porous.
Q: Can non-woven geotextile fabric be used for driveway applications?
A: Yes. Typically, it may be seen as ground cover in driveways to stabilize them while separating any subsoil from aggregates, thus ensuring that driveways remain stable over a long period of time.
Q: What weight options are available for non-woven geotextile fabric?
A: The choice of weight should depend on the specific use case and the required strength/permeability; hence, these products come in various weights, such as 4 oz., 8 oz., and 12.5 oz.
Q: Is non-woven geotextile fabric suitable for landscaping?
A: Absolutely. Non-woven landscape fabrics are commonly employed in many areas. These items help keep off weeds, improve drainage, and prevent soil erosion, which has seen them gain popularity in various landscaping projects.
Q: What are the typical applications of non-woven geotextile fabric?
A: Non-woven geotextiles are widely used in different areas, including drainage systems, road construction works, erosion control, landscaping, and agriculture. They are also applied as filter fabrics for septic systems and other water management systems.
Q: How does non-woven geotextile fabric contribute to water drainage?
A: It acts as an efficient filtering material by allowing water to pass while retaining solid particles within the soil, called non-woven geotextile fabric. This will help prevent soil clogging and ensure your drainages work well without any hurdles.
Q: What is the significance of polypropylene fibers in non-woven geotextile fabric?
A: This makes polypropylene geotextiles one of the most durable alternatives, which can be used for a variety of demanding applications. They are used because of their high tensile strength, resistance to chemicals, and resistance to biological degradation.
Q: Are there any specific installation guidelines for non-woven geotextile fabric?
A: Yes, correct installation is very important if you want your nonwovens to serve you properly. Ensure they lie flat, with overlaps where necessary, and then use pins or staples to keep them from moving around. In some cases, such as when dealing with gravel roads or drainages, try following what the manufacturer says precisely.