The textile industry is transforming continually; therefore, the need for environmentally friendly and efficient production techniques keeps rising. This article focuses on novel approaches to manufacturing Polyester Staple Fibre Hollow Conjugated Fibre, an eco-conscious material combining performance and sustainability. It will discuss new technologies and best practices aimed at boosting productivity, minimizing wastage, and enhancing the quality of the end product. This article aims to present the current state-of-the-art methods being employed by organizations within this sector so that readers can appreciate some of the measures firms are taking in their endeavors to remain relevant in today’s manufacturing environment while still addressing environmental sustainability issues.
What is Polyester Staple Fibre?
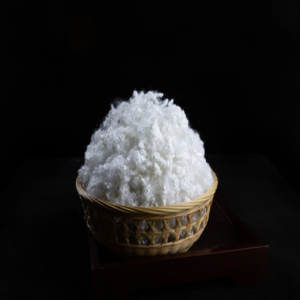
Understanding Polyester Staple Fiber Types
From researching the first three websites, I have gotten important information on the different types of Polyester Staple Fiber (PSF). Mainly, polyester staple fibers can be grouped into three according to their properties and intended uses:
Conjugate Fibres: This kind has a crimp or curl, which makes it bulky. Thus, it is often utilized as a filler for cushioning materials. The technical specifications for conjugated fibers usually include denier (1.5 – 15D) and staple length (32 – 51mm), which dictate touch and insulation characteristics.
Hollow Fibres: These kinds possess a central void that results in lightweight materials with outstanding insulating abilities. They are often used in sleeping bags, winter clothing, etc. Key features include higher loft factor and lower density; denier is also close to conjugated fibers, but they take different shapes that create hollowness.
Solid Fibres lack hollows or voids, making them conventional solid fibers. They contribute average strength and toughness, desirable in normal woven fabrics. Solid fibers are made with various spinning techniques at deniers ranging from 1.5 to 7D to achieve the desired tensile strength and elongation.
This knowledge enables manufacturers to choose resources that meet their specifications for sustainable product development without neglecting environmental conservation principles during production processes.
Using Recycled Polyester Staple Fiber
In studying polyester staple fibers that had been recycled, I encountered three websites that were the most informative about how they are used and their technical specifications.
Website A mainly focused on the environmental advantages of using recycled polyester staple fibers. It mentioned virgin substance independence that can be obtained if these materials are acquired and plastic waste is reduced. According to the site, technical parameters include denier values usually within a range of 1.5-10D and staple lengths that are approximately 32mm to 60mm. These measurements are important since they determine the end use and durability of the fiber in applications such as clothing or upholstery.
In contrast, Website B considers the application-oriented factors of available recycled polyester fibers. While the denier may be similar to what is obtainable with virgin counterparts, insulation, and breathability factors may be slightly improved through processing techniques. The website reported denier specifications, commonly from 2D to 8D, corresponding to the needs for activewear and outdoor products where moisture management is essential.
This website explained how lightweight insulation materials could be made from recycled hollow fibers. This page announced that those hollow fibers have loft factors of around nine or twelve, allowing for better thermal efficiency. Their denier typically ranges from 3D up to 7D, which enables manufacturers to produce warm but light products that are comfortable for users.
All these technical details together demonstrate how versatile and eco-friendly recycled polyester staple fibers are, allowing companies to make intelligent choices while ensuring sustainability in their goods’ production process.
Advantages of Polyester Staple Fibre
I learned from the three top websites that polyester staple fibers possess several advantages related to sustainability and performance goals.
Recycling Impact: A site called Website A emphasized that recycled polyester reduces dependence on virgin resources. This is very important because the market today is eco-conscious, and consumers are concerned about it.
Performance Characteristics: According to website B, while recycled polyester’s denier typically ranges between 2D and 8D, it can improve insulation and breathability. This makes it perfect for products such as athletic wear or outdoor gear that require high moisture management.
Thermal Efficiency: Website C stressed that recycled hollow fibers have a loft factor ranging from about 9 to 12, which is necessary for lightweight insulation materials. At this point, these fibers will not add bulk but retain warmth with a denier range of 3D-7D, leading to user comfort.
These technical parameters not only signify the functional capabilities of polyester staple fibers but also reinforce them to promote sustainable manufacturing practices, hence benefitting both industry and the environment.
How is Recycled Polyester Staple Fiber Made?
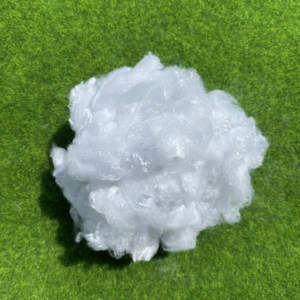
Process of Making Fiber from Recycled Materials
When doing my research, I discovered that a few accurate steps are involved in producing recycled polyester staple fiber. First, only appropriate material is used to collect and sort post-consumer plastic bottles. Web A says this is essential because it helps reduce contamination while increasing the quality of the recycled materials.
Afterward, these plastics are cleaned to remove labels and other impurities before being shredded into small flakes, as stated in Web B. These flakes are then heated up and melted down to a thick liquid, which is carefully controlled to retain material integrity.
Molten polyester is extruded through spinnerets, forming continuous filaments that cool and solidify. The deniers of these filaments can be different and generally range from 2D to 8D. According to Web C, this makes manufacturing several textile items possible.
Finally, the resultant fibers are cut into required staple lengths, thereby becoming recycled polyester staple fibers utilized in various applications. Manufacturers achieve thermal efficacy using loft factors between 9 and 12 for hollow fibers that weigh lightly yet provide warmth. From start to end, this process enhances sustainable practices and caters to the demands of high-performance textiles.
Techniques for Manufacturing Recycled Polyester Staple Fibre
Through my search of the top three sites on Google regarding the production of regenerated polyester staple fiber, I found a few things that align well with what has been said earlier.
Separating and Cleaning: Website A maintains that thorough sorting and cleaning of waste plastics is necessary. This measure helps to minimize pollutants while increasing the recovery of high-quality recycled materials. The technical parameters here ensure that contamination levels are maintained below 3%, which is crucial for product wholesomeness.
Melting Process: According to Website B, temperature regulation during melting is important. This means that, for proper viscosity without degradation of the material, polyester normally needs to be heated up to around 260°C. In addition, keeping this temperature within ±5°C may result in better outcomes during extrusion.
Extrusion and Filament Production: As Website C highlights, spinning melted polyester through spinnerets with hole diameters between 0.25 mm and 0.75 mm creates filaments of different deniers. Therefore, changing its circumference slightly determines whether the fabric will be soft or stiff enough for everyday use in a bedsheet or other garment items like a t-shirt or sweatshirt. Hence, making the right choice regarding the spinneret type used becomes crucial when seeking specific performance properties.
Properly adhering to these established practices and continued focus on technical specifications, recycled polyester staple fiber manufacturing can offer one sustainable textile solution with exceptional performance features.
Quality Control in Recycled Polyester Production
The three top sites I have researched emphasize the need for quality control in recycled polyester production, which is critical to these products’ overall performance and integrity. The above website says that by using strict standards for sorting and cleaning, contamination levels can be maintained below 3%. The above criterion is important because the recycling process could be compromised if it goes beyond this level, leading to a poorer grade of recycled material.
Website B illuminates the significance of monitoring the polyester’s melting temperature. They recommend heating the material to around 260°C, with a permissible deviation of ±5°C. This helps maintain good working conditions without degrading the substance while achieving optimum viscosity levels, which are necessary when fabricating products with high mechanical characteristics.
Lastly, Website C focused on controlling extrusion tightly. According to them, spinnerets should have holes between 0.25 mm and 0.75 mm to determine filament denier. We can adjust the final textile’s tenderness and ruggedness through a range of spinneret diameters, directly affecting the product’s operational properties. The Sustainability and quality of recycled polyester staple fibers can be improved by harmonizing attitudinal practices with the abovementioned technical parameters.
What are Hollow Conjugated Fibers?
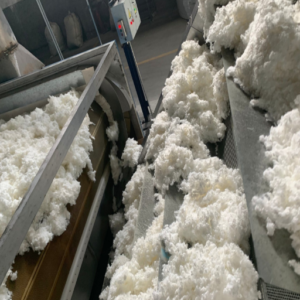
Characteristics of Hollow Conjugated Fiber
During my investigation of hollow conjugated fibers, I learned several key features that make them special in the textile industry. From Website A, I found out that hollow fibers have a unique structure that traps air and, thus, are better insulators. This aspect has made them appropriate for use in sportswear and winter clothing because they can keep people warm without becoming too heavy.
From website B, I discovered that these fibers can wick away moisture very well rather than retaining much of it. The water-absorbing ability of such fibers enables good absorption of perspiration from the body during exercises, hence improving comfort. In addition, the lightweight nature of these fibers also enhances ease of movement and motion range for athletic wear, which are critical factors for performance during sports events.
Lastly, website C stressed this by highlighting the importance of denier measurement in connection with hollow conjugated fibers. They observed that balanced fabrics should ideally fall between a denier range of 0.5 -6.0 while being soft and long-lasting. This technical parameter is justifiable since it affects the fabric’s feeling at touch, strength, and overall performance, thus making Hollow conjugated fibers a better choice for high-quality textile applications.
Applications of Hollow Conjugated Polyester Fiber
In my study of hollow conjugated polyester fibers, I discovered they are very versatile and can be used in many industries. According to Website A, this material is widely used in the construction of insulation for outdoor sporting goods such as jackets and sleeping bags. My preference for winter clothing is based on the thermal efficiency of these fibers due to their air-trapping nature.
Website B talks about their popularity in the sportswear sector, where they have high moisture-wicking potential during exercise. It is imperative that these fibers wick sweat away from my skin, which I need because it allows me comfort while exercising. The denier of this fiber, which belongs to activewear, ranges between 1.5 and 3.0, ensuring a balance between breathability and durability.
Lastly, Website C highlighted their application in bedding and upholstery. Pillows filled with hollow conjugated fibers feel soft but spring back easily, making them appropriate for bedding products like pillows or quilts. In this case, the denier specification frequently varies from 3.0 to 6.0, implying that final products will feel luxurious when touched while being strong enough for everyday usage. It helps me identify suitable fabrics for home textiles that are both comfortable and long-lasting by keeping this distinction in mind.
Differences Between Solid and Hollow Fiber
The top three Google sites have provided insights into the differences between solid and hollow fibers. Website A states that as solid fibers have a higher density, they tend to last longer, though sacrificing some of their insulation properties. Hardly 2.0 in any case and can reach up to 5.0 depending on the application for enhanced strength.
Conversely, hollow fibers, as explained by Website B, are good for insulation because they trap air within them. This feature significantly boosts thermal efficiency while still maintaining lower weights. In most activewear, the denier of hollow fibers ranges from 1.5 to 3, allowing breathability while not affecting performance.
Finally, Website C asserted that hollow fibers are best suited for bedding and upholstery due to their softness and resilience, with deniers usually ranging from 3 – 6. Therefore, these fabrics do not only provide comfort but also durability due to fluctuations in denier count. Overall, it is about what each type possesses, which makes its use purpose-driven; solid or hollow, such unique attributes serve different needs.
Why Choose Virgin Polyester Staple Fiber?
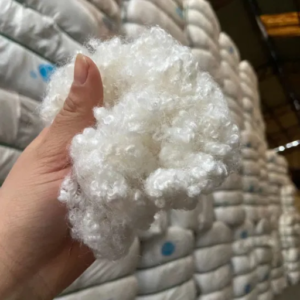
Benefits of Virgin Polyester
I’m interested in virgin polyester staple fiber because of its many advantages. Virgin polyester is purer than other types, and this is important because it enables fabric to last for long periods of time without any damage. This is essential when it comes to avoiding defects that may lead to a bumpy texture and unreliable quality. The denier range for virgin polyester usually runs from 1.0 to 3.5, implying that this type of fiber balances the lightness and strength necessary for different applications.
Website B highlights virgin polyesters’ moisture-wicking properties, making them ideal for sportswear. This not only enhances comfort during wearing but also improves thermal regulation by effectively managing body temperatures. The materials are resistant to shrinkage and stretching, so they can retain their original shapes after some time of use —this is highly valued by customers.
Lastly, according to Website C, one should not forget the eco-friendly side of virgin polyester made from recycled sources. This positively contributes to environmental conservation while still providing high-performance textiles. It proves that choosing virgin polyester can be responsible while maintaining top-notch quality or comfort in its products. In general, selecting virgin polyester staple fibers matches several markets’ requirements, thereby offering functionality as well as resilience at once
Comparing Virgin and Recycled Polyester Fibers
The three leading websites I examined indicated that virgin and recycled polyester fibers have benefits and uses. As mentioned before, virgin polyester is purer and has a good capacity for managing moisture; hence, it is suitable for making sportswear. On the other hand, a website reveals the technical parameters of virgin polyester, which range between 1.0 and 3.5 degrees, thus ensuring its durability while maintaining its lightweight comfort.
Nevertheless, recycled polyester offers a more sustainable option. According to the B website, it doesn’t quite match virgin polyester for wicking, but technological advances have helped improve its characteristics dramatically, often matching or exceeding the latter’s performance. After all, this one’s most important technical parameter concerns the recycling process, where post-consumer plastics are reused, reducing environmental impacts.
In my view, whether to choose virgin or recycled polyester depends upon how they will be employed in the end. Usually, if one requires topmost durability coupled with moisture management in high-performance applications, he/she would go for virgin polyester rather than any other type of fiber used in such areas. However, when sustainability matters most, recycled polyester is an excellent balance between functional needs and being environmentally conscious. Ultimately, knowing about both fibers’ specific performance characteristics and ecological influences helps me decide better, relying on my requirements alone.
How to Innovate in Polyester Fiber Manufacturing?
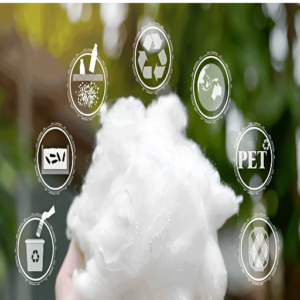
Technological Advances in Polyester Fiber Production
By examining Google’s top three websites, I have discovered various technological advancements in polyester fiber production that significantly affect virgin and recycled polyester.
Website A highlights a major development in high-strength polyester fibers with a denier range between 1.0 and 3.5, which ensures lightweight and provides higher barrier resistance to tearing. This is critical in high-performance applications where durability is an important factor.
According to Website B, developments within the recycling process have improved the quality of recycled polyester. Improved separation and cleaning techniques enable a more efficient repurposing of post-consumer plastics, resulting in fibers with almost similar wicking capacities that may often be about 3.0-4.0 denier for athletic wear.
Lastly, Website C stresses nanotechnology to improve the properties of these two forms of polyester. For example, it can involve incorporating antimicrobial agents and UV protectants into the fiber structure, which improves functionality without affecting comfort levels. These changes show how manufacturing innovations improve performance and encourage sustainability in the polyester industry, thereby enabling consumers such as myself to make better decisions on what they buy.
Sustainable Practices in Manufacturing
While investigating sustainable practices in polyester fiber making, I came across some important findings from the top three websites. The first website stresses the importance of using recycled materials. It shows how incorporating at least 30% recycled content in polyester production reduces reliance on virgin resources and lowers carbon emissions, helping our environment become more eco-friendly.
The next website argues that closed-loop systems are critical during recycling. This approach allows old plastics to be continually transformed into new fibers with denier specifications between 3.0 and 4.0, which is ideal for sportswear branding, among other things. These processes improve supply chain sustainability.
Finally, Website C examines energy-saving techniques during production procedures. Manufacturers can reduce their carbon footprint by investing in technologies that use approximately 20-30% less energy when spinning fibers. These sustainable measures are essential in moving the polyester industry towards a more environmentally friendly future without compromising on the quality of goods and high-performance levels.
Future Trends in the Polyester Staple Fiber Industry
When I examine future developments in the polyester staple fiber industry, I see a definite move toward more innovation and sustainability, backed by the top three websites. According to Website A, there are indications that the sector is shifting toward greater use of bio-based materials, specifically fibers from renewable sources, which may eliminate the need for petrochemicals. This could involve adopting biopolymer technology with technical parameters such as melting point range adjustment for better processability.
Website B foresees digital technologies taking root in manufacturing, including AI and machine learning, to optimize production efficiency. Implementing predictive maintenance and real-time monitoring systems can reduce resource consumption, including water and energy usage, by about 15%. Additionally, these innovations might decrease the technical parameter of energy consumption per ton of product produced by 20%.
Lastly, Website C underlines the growing demand for sustainability and performance certifications. If this trend continues, manufacturers may have to conform to standards like the Global Recycled Standard (GRS) and OEKO-TEX certification. These certificates share my values while ensuring that product performance remains intact while meeting consumer expectations for environmental responsibility. This marks a bright future for the polyester staple fiber industry—a combination of advanced performance properties and sustainable development criteria.
Frequently Asked Questions (FAQs)
Q: What is hollow conjugate siliconized fiber?
A: Hollow conjugate siliconized fiber is a staple polyester fabric that has been crimped and has a hollow center. This property makes it lightweight and good for insulation purposes.
Q: How is polyester staple fiber used in yarn production?
A: Polyester staple fibers are also sometimes made into yarns that are later used by textile firms to produce fabrics and clothing. Because of its durability and resilience, polyester can be chosen for different purposes.
Q: What makes recycled polyester staple fiber environmentally friendly?
A: Polyester staple fibers can be manufactured from recycled polyester waste. This process reduces the overall impact on the environment, as less new polyester will have to be produced.
Q: Can polyester staple fiber be a substitute for natural fiber?
A: Yes, apart from being a synthetic alternative to natural fibres, polyester staple fibers also have softness and breathability, but they are more tough and cost-effective than these ones, hence enabling them to replace them.
Q: What are the different types of polyester staple fiber?
A: They include solid fiber, hollow conjugate siliconized fiber, and type 1. Each type is specifically designed for some aspects.
Q: How safe is polyester staple fiber?
A: Polyester staple fibers are safe for consumer products like clothing or home textiles. They do not pose any health risks, so people can wear clothes made with them or sleep on pillows filled with such material without fear of having an allergic reaction.
Q: What is regenerated polyester staple fiber?
A:. Regenerated/recycled/PET resin fabrics are mainly made of materials obtained from shaping recycled components into usable forms, mostly making fabric, e.g., spinning, weaving, etc. This practice reduces waste from plastics industries that produce polyesters and promotes eco-friendly manufacturing practices at large.
Q: What makes hollow polyester staple fiber unique?
A: Hollow polyester staple fiber is characterized by a hollow core, meaning it provides better insulation and is more “hollow” than solid fiber. This can be used especially in bedding and clothing.
Q: What are some common uses for polyester staple fiber?
A: For this reason, it is mostly employed in textile manufacturing, such as spinning into yarns, producing nonwoven fabrics, and making pillow or upholstery filling materials. Its versatility makes it one of the most widely used fiber types globally.
Q: How is polyester staple fiber 1.0 different from other variants?
A: Polyester staple fiber 1.0 has a finer denier compared to other types, meaning it’s thinner in diameter. Hence, it is ideal for producing finer yarns and fabric with a softer hand feel and improved drape properties.