Known for unlike rods used industrially, in textiles or even in design, monofilament yarn is revered for its strength, adaptability and durability. Crafted from a single-strand of thread that goes through an extrusion process, this material is unique. This guide will assist users on how monofilament yarn works, its makeup and the production techniques incorporated to manufacture the yarn. As one progresses along the guide, they will learn the reason monofilament is preferred over traditional multifilament and why it is a commendable choice for critical high-performanced uses. With us, you will explore the science and versatility of yarn monofilament along with its scope and potential.
What is Monofilament Yarn?
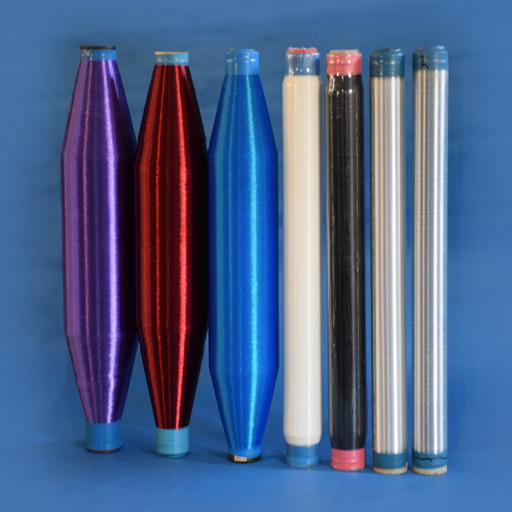
A monofilament yarn is simply a singular strand of synthetic fiber. Fabricated from materials such as nylon, polyester, or polypropylene, monofilament yarn differs from multifilament yarn as it is singular rather than composed of multiple smaller fibers intertwined together. It is more smooth, uniform, and more tough than multifilament yarn. Because of it’s sutures, industrial fabrics, and even fishing lines, monofilament yarn is best known for being strong, tough, and having excellent resilient properties against any form of abrasions that may try to damage it. The simplicity of it’s structure gives it great adaptability across various high-performing sets of work.
Definition and Characteristics of Monofilament
A monofilament is made of one continuous strand of a single material, generally consisting of synthetic polymers like nylon, polyester and polypropylene. Its creation involves a meticulously controlled extrusion process where melted polymers are forced through a spinneret to create a uniform fibre. The process of manufacturing it into a product that has a uniform diameter adds to its precision and reliability in more specialized applications.
Monofilament tape is highly hydrophobic, providing further exposure to extended moisture and sunlight. Such properties make monofilament tape highly reliable around demanding environments. Other than being highly hydrophobic, it also exceeds in tensile strength surpassing 5.5 grams per denier alongside UV resistance. Such feats can be attributed to the composition and processing techniques implemented during manufacturing the tape. Furthermore, monofilament has impressive tensile strength with dimensional stability, further indicating its durability.
Monofilaments are intended to restrict elongation under tension in uses such as surgical sutures, where precision is critical, or fishing lines, where repetitively applied mechanical stress needs undivided attention. Moreover, shifts in polymer engineering has enabled the fabrication of more complex monofilament forms that use additives or specialized coatings to improve other properties such as resistance to abrasion, biocompatibility, or thermal stability for other more demanding industry standards.
Differences Between Monofilament and Multifilament Yarn
Yarn monofilament is made from a single synthetic fiber strand, either nylon, polyester, or polypropylene. Monofilament yarn offers many features because of its structural simplicity including its smooth uniform finish. Monofilament yarn can be instead used in high-performing contexts due to its abrasion and corrosion resistance. This also requires monofilament yarn to have strength, resilience and other features. Monofilament offers a high degree of versatility due to its simplistic structure. Its durability comes from a lack of flexibility and high tensile strength while simultaneously offering lower flexibility and higher durability.
On the flip side, multifilament yarn is made up of several thin filaments that are either twisted or bundled together. This multi-thread arrangement increases bendability, softness, and elasticity. Its finer structure allows multifilament yarn to be an advantage in textile applications, providing comfort and a fine quality finish to fabrics. Multifilament yarn is also good for making parts like ropes and nets which need to be strong and flexible. Also, the superior surface area-to volume ratio of multifilament yarn increases its compatibility with different coatings or treatments.
Common Uses of Monofilament Yarn
As fishing lines require strands of smooth yarn with minimal knots that can withstand substantial amounts of stress, the fishing industry was one of the first to use monofilament yarn. Due to the yarn’s superb particle bond resistance to water, monofilament has also been deemed ideal in marine conditions. Being suitable for multiple industries, monofilament is also used to fabricate sutures in the medical sector. With minimal impact on the tissues hurt and needing to heal, their body is able to sustain faster healing while also being biocompatible, making monofilament yarn more preferable for sutures than others.
Not only that, but adjustable belt clip researchers undergoing industrial test filtration claim monofilament to be the best synthetic material because of its rigid structure partnered with high enduring withstand to abrasive stress, will stand up to being warped, thus providing exact precision when filtering in harsh positions like chemically processing or filtering wastewater.
Monofilament yarn also finds usage in the agricultural sector. It is employed in forming netting for crop protection which provides a strong yet lightweight net against pests and severe weather. In addition, artificial turf uses monofilament yarn, as it imitates natural grass in both appearance and function while being durable under heavy traffic.
How is Monofilament Yarn Made?
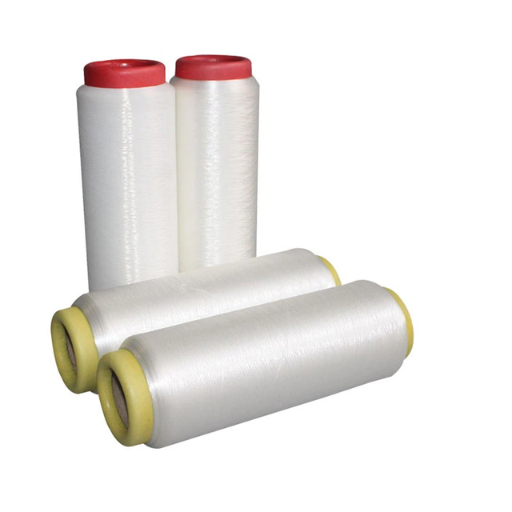
Yarn of this type is monofilament yarn – it is produced by the technique of extrusion. First, constituent thermoplastic materials like nylon, polyester, or polypropylene, are put into a heater so that they can be melted. Afterwards, they are put in spinnerets – tools with small holes which do not allow any other fitting tool to be inserted. Spinnerets aid in forcing the molten material through put in holes to create single and windowed strands which are afterwards cooled and solidified. The yarn formed is elongated post cooling so that its strength and elasticity can be enhanced. The strands are then placed in containers for further use or processing based on its purpose of application. This technique guarantees uniformity and reliability within the final product.
The Extrusion Process Explained
The extrusion process has greatly improved over the past years thanks to strides made in engineering and material science. Now, it can be used in many different sectors. For example, in the production of thermoplastic polymers, the process is streamlined to perfect the texture and diameter of the end product. Modern methods of extrusion can reach up to 1000 meters a minute in production speed, proving how effective they are in mass production.
Moreover, extrusion has been effective in the food processing industry. It is used in producing cereal, pasta, and even snacks. The versatility of the extrusion methods enables the products created to have a desired texture by changing the temperature, moisture, and content of the ingredients.
As with any modern technologies, advancements in the extrusion process incorporate sustainability. For instance, extrusion feeds are now incorporating more recycled materials, including post-consumer plastics, as extrusion waste mitigagtes. Studies show that extruded products with mechanical performance up to 50% recycled content performs sustainably. This can be seen as an advancement in the sustainability of the process.
Role of the Spinneret in Yarn Production
In the manufacture of synthetic fibers, the spinneret stands out as a critical component. It is described as: a device that serves to create filament solutions or melts which are extruded in a continuous way. In general, they are made of stainless steel or platinum for spinneret corrosion and heat resistance, so it is reasonable that the is made from stainless steel or platinum. It has many tiny holes that helps in shaping the molten polymer into threads and casting it in a thread-like configuration. Improvements in the design of the spinneret enables accurate control with filament features like – the diameter, cross-sectional shape and the strength of the filament.
Recent developments of spinnerets have increased the evenness of filaments produced while lowering the number of defects associated with their manufacturing. This is very important for industrial use. For instance, changer spinneret holes like trilobites and hollows are designed for better surface texture, dye uptake, and general functionality of the fibers. Studies show that spinnerets containing micro-fabricated profiles are able to manufacture filaments with greater tensile strength, which is crucial for high impact textile uses such as active wear and technical fabric textiles. Also, the developmental use of computational modeling tools has further improved the process of convincing spinneret design from scratch because these tools enable flow dynamics to be simulated and predicted for best fiber characteristics. Advances in this field are likely to increase the cost-effectiveness of polymer use by minimizing waste and addressing the need for quality synthetic fibers.
What are the Applications of Monofilament Yarn?
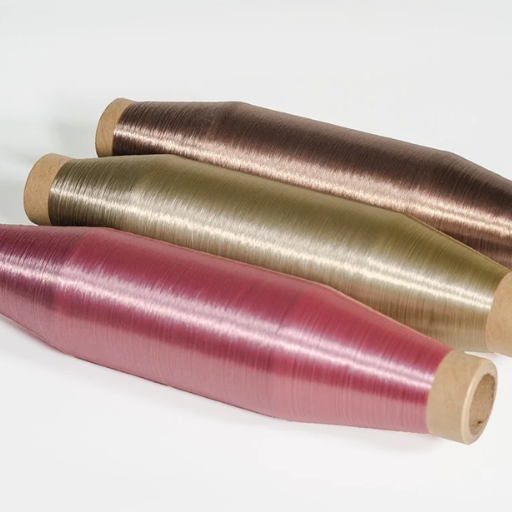
The durability and strength of monofilament yarn makes it useful across many industries. High tensile strength marks its use for fishing lines, ropes, and netting. It’s also used in agriculture for greenhouse shading nets and as crop support systems. Monofilament yarn is also used in textiles, for performance-specific fabrics, such as filtration materials, and industrial screens. It is also adaptable for consumer need as medical sutures, tennis racket strings, and even 3D printing filaments. These examples highlight both consumer and technical applications of monofilament yarn.
Use in Textiles and Apparel
Monofilament yarn is important in modern clothing textiles, especially where there is strenth, flexibility and performance. Monofilament yarns play an important role in the production of activewear, mesh materials, and woven textiles. Functional activewear features moisture-wicking and airflow properties which are even more enhanced by the actions of monofilament yarns.
Now, combining monofilament yarn with other fibers, like polyester or nylon, is being done with high precision in regard to textile engineering. This leads to the creation of lightweight but strong fabrics. This new monofilament fabrics is particularly useful in industrial fire and abrasion resistant uniforms. Monofilament fabrics are also employed where precise thread diameters are needed, such in filtration systems and geotextiles.
In consumer markets, monofilament based textiles are increasing in popularity. The CAGR (Compound Annual Growth Rate) of technical textiles is 5 to 7%. Monofilament yarn is becoming a vital part of modern advanced textile solutions due to the growing demand.
Applications in Filtration and Fishing Lines
The use monofilament yarn in filtration systems is a must because of its unique diameter, strong tensile strength, and resistance to chemicals. This is critical, because its woven and nonwoven pores could precisely filter out particles during industrial processes like water cleansing, food and beverage manufacturing, and air purification. For example, the industrial filtration market is expected to grow from 2023 to 2030 at a CAGR of 6-8%. This shows that there is considerable dependence on complex filtration systems like those using monofilament fabrics to fulfill strict laws and performance standards and requirements.
Diving deeper into the fishing sector, it is clear that the use of monofilament lines is preferred due to their strength, flexibility, and underwater invisibility because of the light refraction. The latest developments in polymer engineering also emerged with new mitigation of abrasions, UV changes, and knot strength in monofilament lines for both commercial and leisure activities. The recreational fishing broadens, in particular, is going to be the main driver with the expected market surpassing $17 billion by 2030. These developments highlight the importance of monofilament materials across different industries.
What Makes Monofilament a Preferred Choice?
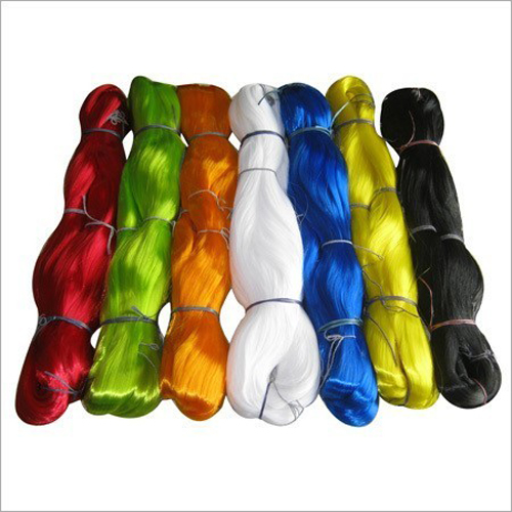
Monofilament is often preferred because of its durability and cost effectiveness. Monofilament also offers versatility in its applications having fabrication within numerous industries owing to its lightweight design. It is also easy to manufacture and can be customized for certain applications quilted against abrasion and enhanced resistance to UV light. Its dexterity and reliability allow it to be freely used in both recreational and commercial purposes throughout the world.
Advantages of Monofilament Yarn Over Other Types
- Superior Tensile Strength
It can be noted that monofilament yarn has better tensile strenght than multifilament and spun yarns. For example, some applications offer load withstanding abilities of over 10 grams per denier (gpd). Such applications working with high-stress environments include surgical sutures, industrial nets, and fishing lines.
- Abrasion Resistance
Monofilament yarn has less friction which increases its abrasion resistance. The smooth and consistent surface allows abrasion protective covering over it compared to other yarn types. This quality is quite advantageous in heavy-duty applications where mechanical wear is frequent.
- Enhanced Durability
Having its design quilted with a single strand offers monofilament yarn better resistance to harsh environments which greatly increases its durability. Withstanding UV rays and moisture decreases chances of ever experiencing degradation, prolonging service life in outdoor or marine conditions.
- Lightweight Properties
Monofilament yarn is, by design, lightweight making it best suited for operations that require lifting a lot of bears such as aerospace components and lightweight textiles.
- Cost-Effectiveness
Cost effective production methods such as extrusion of nylon, polyester or polypropylene monomers yields monofilament yarns. This gives the product uniform structural properties while allowing it to be produced at a large scale.
- Precision and Versatility
In addition to customization in chemical composition and thermal resistance, monofilament yarns can also be made anti-bacterial and chemically resistant. This increases the scope of industries such as medicine, agriculture and automotives where the material can be used.
Monofilament yarns will remain as key components in modern technology because they are able to fulfill the demanding criteria that is associated with new-age applications.
Understanding Tensile Strength and Durability
Tensile strength explains the maximum amount of energy that stress a material can withstand, which is very important when checking the mechanical properties of materials which are heavily used in industries. It is usually measured in units of force per cross-sectional area magnitude that is being measured in megapascals. Materials like steel of high quality can possess tensile strengths of over 1200 and advanced carbon fiber composites can exceed 3500 making them extremely useful for aerospace and advanced commercial sporting goods.
Unlike the above, durability determines the ability of a material to perform its functions and maintain that performance level over time when undergoing physical, chemical or environment related stresses. Corrosion resistance alongside degradation of UV rays and wear-and-tear are important to a materials long-term effectiveness. Studies reveal that polymer based monofilament yarn, improved with UV resistant polymer additives, can achieve up to 50% increased lifespan in outdoor settings, as compared to unprotected counterparts.
Blending the characteristics of tensile strength and durability is particularly important in the materials engineering fields of automotive, construction, and textile manufacturing. Take tire reinforcement materials, for reinforcement to be mechanically effective, it has to possess high tensile strength and enable an exceptional service life throughout operating environment variations. Further developments in material science are constantly enhancing these parameters to best suit the requirements of enduring applications in harsh environments economically and environmentally.
How to Choose a Supplier for Monofilament Yarn?
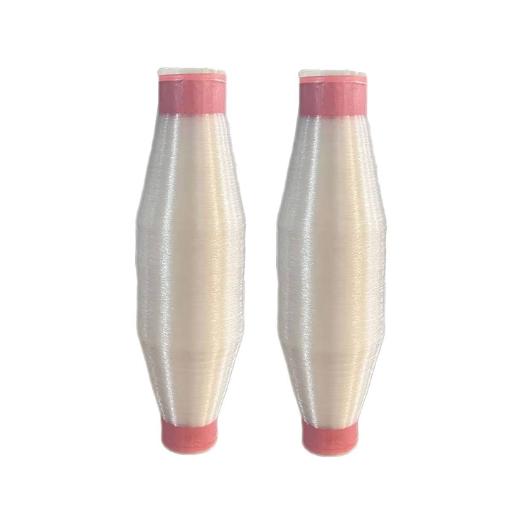
Choosing a supplier for monofilament yarn requires consideration of multiple factors that guarantee optimal quality, reliability, and cost-effectiveness:
- Product Quality: Check that the Supplier has monofilament yarns with an ever-present grade of strength, uniformity, and durability, which meets industry standards.
- Industry Experience: Look for a supplier that has maintained good standing for his or her monofilament yarn production and is specialized in dealing with your particular case since, in most cases, reliability, experience, and expertise go hand in hand.
- Capacity and Scalability: Evaluate the vendor’s ability to produce goods and more importantly if they are able to deliver quantity you need on a regular basis, even at the height of demand.
- Certifications and Compliance: Demand to see if the vendor is compliant with certain quality and environmental policies like holding some ISO certifications as a mark for trust and maintainable products and services.
- Customer Support and Service: Pick for the supplier that has good articulation of the issues, sharp attention to the consumer, and technical assistance pertinent to the product.
- Cost and Delivery: Evaluate the cost presented with the delivery time of the work to make sure the supplier has fair prices, of course, with an agreement on the standards offered to be met.
After evaluating the factors presented above, a supplier that fits the requirements offered will indeed align with the set business operational goals.
Key Factors to Consider When Selecting a Supplier
- Scalability and Capacity: Assess if their business can grow with yours. Research in supply chain management suggests these suppliers possess flexible manufacturing systems. Moreover, those with distributed production facilities tend to respond better to demand changes. For example, suppliers with multiple warehouses or sophisticated inventory systems are capable of rapid order delivery during peak season.
- Certifications and Compliance: Controlling aspects like the defined procedures within a business ensures that the supplier achieves basic operational requirements which includes holding the proper namings like ISO 9001 quilt management or ISO 14001 for environmentally aligned businesses. These suppliers, who are compliant with such requirements, claimed protect operational compliance policies, defend, and employ responsible company frameworks. Recent findings highlight the need to engage alongside vendors who comply with regional and international guidelines to minimize legal risks regarding the reliability of the product and improve the overall legal protection friendly environment we’re in.
- Technological Integration: Suppliers that have modern technologies such as Enterprise Resource Planning (ERP) systems along withdata analytics have higher transparency and efficiency. These systems enable real-time tracking of orders and enhanced communication with the supplier. Businesses utilizing technology-backed suppliers often register improvements in supply chain performance, facing fewer disruptions that are resolved quickly.
Considering these additional aspects together with your detailed business needs will help you develop sustainable optimized relationships with suppliers that are efficient, dependable, and growth focused.
Importance of Quality and Technical Parameters
Maintaining product consistency resulting in customer satisfaction and competition within the market requires a high level of quality and strict compliance with technical parameters. SPC and Six Sigma processes have been proven to reduce variability and improve operational effectiveness. For example, Quantcast system such organizations face up to a 20 percent productivity increase and 15 percent cost savings through the minimization of errors and waste. These figures underscore the benefits of implementing rigorous quality management systems (QMS).
In the aerospace and automotive industries, as well as electronics, high-tech engineering sectors, so-called “from a technical perspective” assurance, ISO Certification for instance, and regulatory compliance are other standards which aid in reliability and interoperability. Material tolerances, design, and performance definitions, as well as others, require incredibly detailed and precise work throughout the full cycle of a product or service. An appropriately managed attention to technical detail not only assists to mitigating risks but also supports optimal incorporation of new technologies down the road, and consequently, keeps companies agile and ready for future challenges.
Businesses adopting these approaches gain customer trust and operational resilience, as well as scale their growth all while sustaining a perpetual balance of technical proficiency and unparalleled quality.
References
-
Influence of Monofilament Yarns on Woven Fabrics’ Stiffness (2023)3:
- Key Findings: This study explored how incorporating monofilament yarns in woven fabrics affects their stiffness. It found that higher proportions of monofilament yarns significantly increased fabric stiffness, especially in the warp direction. Plain weave constructions exhibited the highest stiffness, followed by twill and satin weaves.
- Methodology: Experimental samples were woven with varying proportions of monofilament yarns in different directions (warp and weft). Stiffness was measured using the cantilever test (ASTM D1388).
- Applications: The results suggest potential for industrial applications requiring specific stiffness levels in fabrics.
-
Utilization of PET Waste for Monofilament Yarn Production (2020)4:
- Key Findings: This research demonstrated the feasibility of producing monofilament yarns from recycled PET waste using melt-spinning. Higher winding speeds improved yarn fineness and tensile strength.
- Methodology: PET waste was melted and extruded through a spinneret at varying winding speeds. The physical and mechanical properties of the resulting yarns were analyzed.
- Applications: This approach offers a sustainable solution for recycling PET waste into high-value textile materials.
-
Dry Gel Spinning of Fungal Hydrogels for Renewable Yarns (2024)5:
- Key Findings: A novel dry gel spinning method was developed to produce monofilament yarns from fungal hydrogels derived from bread waste. The process yielded yarns with tensile strengths comparable to natural fibers like wool.
- Methodology: Fungal biomass was cultivated, treated to isolate cell wall material, and spun into monofilaments using a dry gel spinning setup. The process was scaled up using a twin-screw compounder.
- Applications: This method provides an eco-friendly alternative for producing renewable textile materials while addressing food and textile waste.
Frequently Asked Questions (FAQ)
Q: What is polyester monofilament and how is it different from spun yarn?
A: Polyester monofilament is a single filament made from polyester, whereas spun yarn consists of multiple fibers twisted together. Monofilament has unique properties such as high tenacity and chemical resistance, making it suitable for various industrial applications.
Q: Can you explain the production process of polyester filament?
A: The production process of polyester filament involves melting polyethylene terephthalate (PET) and extruding it through spinnerets to create continuous filaments. These filaments are then cooled and wound onto spools for further use.
Q: What are some examples of monofilaments and their applications?
A: Examples of monofilaments include fishing lines, surgical sutures, and bristles for brushes. Their unique properties, such as high breaking strength and chemical resistance, make them ideal for these applications.
Q: How does the elongation at break of nylon and polyester monofilament compare?
A: Nylon typically has higher elongation at break compared to polyester monofilament, which allows it to stretch more before breaking. However, polyester monofilament generally offers superior tenacity and resistance to shrinkage.
Q: What benefits do woven fabrics made from monofilament threads provide?
A: Woven fabrics made from monofilament threads offer durability, excellent strength, and resistance to abrasion. These fabrics are often used in industrial applications where high performance and longevity are required.
Q: Why is high tenacity important in monofilament yarns?
A: High tenacity is important in monofilament yarns because it indicates their strength and ability to withstand heavy loads without breaking. This property is essential for applications like fishing lines and industrial fabrics.
Q: What is the significance of the cross-section in polyester monofilament?
A: The cross-section of polyester monofilament can affect its performance characteristics, such as flexibility and texture. Different shapes can enhance the yarn’s functionality in specific applications, like increasing grip or reducing drag in water.
Q: How does the shrinkage of polyester monofilament compare to nylon monofilament?
A: Polyester monofilament generally exhibits lower shrinkage compared to nylon monofilament, which is beneficial for maintaining the integrity and shape of woven or knit fabrics during use and laundering.