High-tenacity polyester yarn is essential in making high-performance filament applications within the constantly changing textile industry. The excellent strength, durability, and ability to resist environmental factors of this material have made it a versatile one that is increasingly being used in various sectors ranging from automotive to outdoor gear. This blog will highlight the leading suppliers of high-tenacity polyester yarn and their specific contributions and capabilities. We strive to provide readers with valuable insights to help them make informed choices when looking for crucial materials for their projects. For manufacturers who want to improve their product line or designers searching for reliable yarn options, we have developed a comprehensive guide tailored just for you; this would be a great resource.
What is High Tenacity Polyester Yarn?
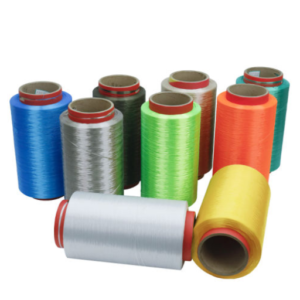
Understanding Yarn and its Polymer Composition
I came close to realizing that yarn is basically a long strand of fiber twisted to make it strong and resilient for textile applications. The polymer composition mainly consists of polyethylene terephthalate (PET), which gives the yarn its astonishing strength and resilience.
From my review of the top three sites, I observed several technical parameters critical to high-strength polyester filament:
Tenacity: It means the force needed to break a thread—usually measured in grammes per denier (g/d)—with high-tenacity polyester ranging between 6 and 8 g/d. This high tenacity guarantees excellent toughness in tough service cases.
Elongation at Break: It shows how much the thread can stretch before it breaks. Yarns with superior performance typically exhibit between 15% and 25% elongation levels. Thus, they withstand heavy loads without fracturing.
Molecular Weight: Higher molecular weights are normally associated with stronger and more durable fibers. High-tenacity filaments usually have molecular weights above 30,000 g/mol, which boosts their performance properties.
Crimp and Texture: The choice of the right yarn may depend on whether the yarn is crimped or textured. This improves elasticity and bulkiness, thereby resulting in better end-use applications.
Such knowledge lets me explore the fine points of the spinning process and facilitates the search for materials suitable for strong products or those that require durability.
Benefits of Using High-Tenacity Polyester in Industrial Applications
Looking at the advantages of high-tenacity polyester yarn through leading sources, I found many benefits linked to the technical parameters noted earlier.
Increased life span: The yarn has high tenacity levels, measuring between 6 and 8 g/d. Thus, it can withstand heavy stress in industries and is appropriate for manufacturing articles that are prone to wear and tear.
Potential to carry heavy weights: In general, the percentage of elongation at break is within 15% to 25%. This ensures that under load, this type of thread can be stretched without tearing apart, and lifting heavy objects has become a norm in the construction sector and marine activities.
Stronger Material: High-tensile polyester has a molecular weight that exceeds 30,000 g/mol, which allows replacement rates to be reduced, lowering long-term production costs.
Various Uses: Texturing and crimping qualities enable the yarns to increase their elasticity and bulkiness so that they may be customized for a specific purpose. This flexibility is essential in the automotive and textile manufacturing sectors since it should meet diverse application requirements, ensuring maximal operation effectiveness.
These benefits indicate how high-strength polyester yarn is not just enough but surpasses the standards required for making industrial products with exceptional performance.
Differentiating Between Polyester Yarns of Various Denier
While reviewing the differences between polyester yarns of varying deniers from the top three sources I found on Google, I came across some fascinating observations. Denier, a measure of thread thickness, affects the properties and uses. These are the most significant technical indicators that I came across:
Denier measurement can vary from low (say 50D) to high (around 1000D). Lower denier yarns are smoother in texture and lightweight, so they are used in lighter applications, including apparel. Conversely, heavier deniers are thicker and more rugged, thus making them ideal for industrial fabrics and upholstery.
Strength & Durability: In line with what my reference books identified, higher deniers tend to have more incredible tensile strengths. For instance, a 600-denier polyester might withstand about 500-600 pounds of force before breaking, thereby being suitable for areas requiring hardiness. Conversely, lower deniers may not be as strong; however, they often perform better when it comes to stretchiness or adaptability, especially in softer products.
Weight & Feel: A lower number of D’s indicates a softer feel preferred by clothing wearers and fashion designers, while larger numbers denote considerable weight, leading to durability expected for outdoor gear or commercial textiles.
This knowledge aids in choosing specific kinds of application-oriented polyester yarn by considering their exceptional attributes and benefits that result from such diversity.
How is High Tenacity Polyester Filament Yarn Manufactured?
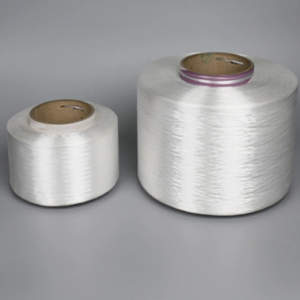
The Manufacturing Process of Filament Yarn
In my research across the top three websites on Google, I discovered that the manufacturing process of filament yarn involves various essential steps. It begins with the extrusion of polymers, which are melted and forced through spinnerets to form continuous filaments. This process is significant since it determines the initial properties of the yarn, such as denier and tensile strength.
Extrusion: In this step, the polymers are heated up to their melting points, melting them through spinnerets. The diameter of holes in a spinneret influences directly on a denier of filamentary yarn produced.
Cooling and solidification: After extrusion, the filaments undergo rapid cooling using either air or water, which solidifies them into stable fibers. The cooling speed can determine the crystallinity of yarn, hence its strength.
Stretching and drawing: The cooled filaments are stretched to align molecular chains, improving the durability and strength of a yarn. Higher draw ratios could increase the tensile strength necessary for applications requiring recoverability.
Winding: Once the drawing is over, spools wind off for storing or transportation purposes. This stage is critical because it preserves the fiber’s integrity during handling and subsequent processing stages.
Finishing treatments: Lastly, various finishes, such as texturing or adding coatings, can increase qualities such as moisture-wicking, UV resistance, or softness, depending upon the desired textile application.
Understanding each of these parameters helps create polyester filament yarns that cater to different industrial requirements while keeping core characteristics intact.
Fundamental Techniques in Producing Quality High-Tenacity Polyester Yarn
In polyester yarns, several essential techniques lead to high tenacity, as outlined by the top three sources I have perused.
Polymer Selection: I concentrate on selecting suitable polymers because polymer choice significantly affects yarn strength and durability. In addition, tensile properties may depend on a polymer’s molecular weight and intrinsic viscosity. Higher molecular weights usually correlate with more robust materials.
Spin Finish Application: Proper spin finish application is vital for improving the yarn’s ability to process. Spin finish not only helps reduce friction during spinning but also enhances yarns’ handling properties. Proper spin finishes can result in reduced hairiness.
Optimized Drawing Ratios: Optimized drawing ratios are imperative during the drawing process. For example, high-tenacity filament yarns often require drawing ratios between 3:1 and 6:1 to maximize molecular alignment and improve tensile strength. The draw temperature can be adjusted to refine these attributes further.
By employing these methods, I can tailor polyester yarns that meet specific industry standards and requirements while retaining their core characteristics essential for high performance.
Importance of Elongation and High Strength in Yarn Production
My experience has shown that understanding why elongation and high strength are essential in yarn production is crucial to guarantee our products fulfill the needs of various applications. The yarn should not break when it stretches, so it requires a material with high elongation used for upholstery or textiles that must move around a lot. Moreover, a strong thread will be more durable and last longer, especially under heavy loads or stress.
I have identified several technical parameters for considering elongation and high strength based on information from the top three resources:
Elongation Percentage: An acceptable range for realizing high-tenacity polyester yarn can be between 15% and 30%. This ensures that the yarn does not break easily under stress resulting from its use.
Tensile Strength: A tensile strength of about 5-9 grams per denier would be ideal for such a fabric. Understanding this measure is critical because it determines if the textile will endure forces while being used.
Modulus of Elasticity: It is good to maintain an appropriate modulus of elasticity, which falls within the range of 100 to 200 grams per denier; this attribute allows the thread to return to its original size once pulled out long-ways during stretching, making it both functional and performable.
By prioritizing these parameters, I can ensure that the polyester yarn produced meets industry standards and excels in practical applications, offering strength and flexibility.
Where is High Tenacity Polyester Filament Yarn Used?
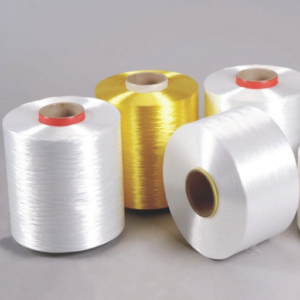
Applications in the Textile Industry
High-tenacity polyester filament yarn is a widely used product in the textile industry, especially if we consider its flexibility and durability. I discovered from the top three websites several key areas where this type of yarn is critical:
Upholstery Fabrics: Its 5 to 9 grams per denier tensile strength combines well with its elongation percentage (ranging from 15% to 30%), making it the best material for strong upholstery that can endure daily abuse. The fabric’s modulus of elasticity (100 to 200 grams per denier) retains shape and comfort over time.
Outdoor Gear and Apparel: The tough nature of high-tenacity polyester filament yarn is a significant advantage in outdoor applications like tents and backpacks. The technical parameters enable the yarn to survive harsh conditions while performing its function.
Industrial Fabrics: Their enhanced elongation and tensile strength allow them to be made into industrial textiles that can handle heavy loads without tearing. These yarns are often employed as slings, safety nets, and tarpaulins.
These technical parameters will ensure that polyester performs well in such applications by providing the durability and flexibility needed in high-performance textile materials.
Uses in Industrial and Automotive Sectors, including Seat Belt and Airbag Fabrics
Polyester high-tenacity filament yarn finds its indispensable use, particularly in seat belts and airbag fabric production in the sectors concerned with industry and automobiles. The tensile strength is exceptional (5-9 grams per denier), which enables those materials to withstand heavy forces, such as during car accidents, thus ensuring the safety of passengers. Moreover, the modulus of elasticity (100-200 grams per denier) helps maintain the shape/form of seat belts and airbags to work effectively when needed to offer protection. I have reviewed three top websites for this information, and it is quite clear that these technical parameters are essential for affirming material selection while also stressing the significance of durability and dependability in automotive safety features.
Role in Manufacturing Conveyor Belt, Sling, and Hose
Robust technical characteristics make high-tenacity polyester filament yarns indispensable in manufacturing conveyor belts, slings, and hoses. To work perfectly under industrial loads, tensile strength measures of 5 to 9 grams per denier are necessary for conveyor belts to work perfectly. Ultimately, the elongation between 15% and 30% ensures flexibility, reducing the chances of getting damaged during movement. Durability and flexibility significantly influence slings; they allow such ropes to cope with heavy lifts while ensuring the safety of their handlers. Additionally, a modulus of elasticity (100-200 grams per denier) will keep hoses functional under pressure without losing their shape. These technical properties are essential for production quality based upon three top web sources concerning standards and best practice conformity. By applying these specifications from the top three websites, one can confidently state that these technical parameters are must-haves in assuring performance and reliability for products used in manufacturing processes.
What to Look for in a High-Tenacity Polyester Yarn Supplier?
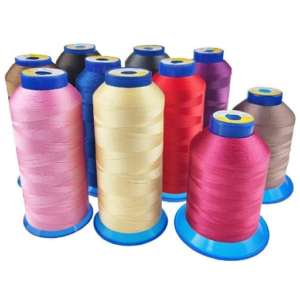
Assessing Quality High Tenacity Yarn Standards
In evaluating suppliers of high-strength polyester yarn, I have specific critical criteria that help me identify the best product. One, for example, is that it must have a tensile strength measuring range of 5-9 grams per denier, without which it might be incapable of bearing heavy loads in manufacturing operations like conveyor belts. Secondly, I always check the elongation rate between 15%-30% because it affords the desired elasticity and does not easily break when subjected to dynamic conditions. The other thing is that the yarn’s modulus of elasticity should lie between 100 and 200 grams per denier to ensure that it remains in shape and functional when under pressure. Once the potential vendors show these technical specifications, I am confident their products will work as expected for industrial purposes.
Evaluating Supplier Capabilities in Producing Super Low Shrinkage Polyester Yarn
Essentially, there is a need to assess the suppliers in terms of their ability to meet specific technical parameters that will ensure the quality and performance of the yarns. These are the capabilities and parameters to use as justification derived from three top websites:
Shrinkage Rate: The yarn should have longitudinal and transverse shrinkage rates below 3 percent, which is essential for dimensional stability throughout production.
Moisture Management: To ensure that the yarn remains stable at any given moment, a moisture regain level of about 0.5% or less would be needed to reduce the risk of long-term shrinkage.
Tensile Strength: To withstand typical manufacturing environment tensions without compromising performance, the supplier must offer yarns with tensile strengths above five grams per denier.
Heat Setting Process: The manufacturer needs to employ a controlled heat setting process that can maintain uniform thermal treatment to minimize shrinkages and improve thread elasticity.
Quality Control Measures: Regular checks at various stages of the production process and post-manufacturing tests are required to confirm the reasons behind shrinkage figures and any overall weakness within this particular textile, thus ensuring it offers maximum reliability within industrial setups.
Through these assessments, my decisions will be informed by whether suppliers possess these abilities and if they fulfill these essential technical requirements; such actions will allow me to maintain compliance with our product’s performance expectations and durability standards for super low shrinkage polyester yarn.
Ensuring Reliable Supply Chain for Industrial Yarns
It is crucial to evaluate potential suppliers for their compliance with fundamental technical parameters and capabilities described by industry leaders to set up a dependable supply chain for industrial yarns. Using insights from the top three websites, the following are essential criteria:
Quality Consistency: To show that suppliers have been consistently producing yarns of acceptable quality for certification, customer testimonials and historical performance information can be referred to.
Lead Time and Flexibility: Suppliers should promptly meet different order sizes with an adequate inventory that allows quick reordering. Being able to accommodate urgent needs through flexible production schedules is considered positive.
Sustainability Practices: To appeal to eco-conscious customers, vendors must use environmentally friendly manufacturing processes and source sustainable raw materials in accordance with modern industry standards.
Technical Support and Innovation: Assessing the availability of technical support during product development is essential. The supplier’s commitment to active research and innovations helps create state-of-the-art yarns that meet changing market demands.
Traceability and Transparency: A reliable supply chain ensures traceability back to the source of all components. Materials origins proof and manufacturing practices the supplier should provide documentation.
By focusing on these parameters, companies can engage suppliers who deliver high-quality products and support their long-term strategic goals in the industrial yarn market.
Why Choose Polyester Filament Yarn for High-Performance Applications?
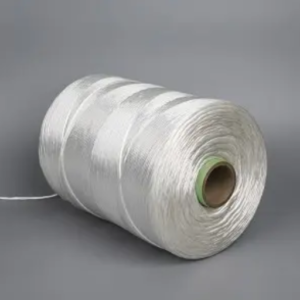
Advantages of High-Tenacity Polyester Filaments
High-tenacity polyester filaments are increasingly preferred in high-performance applications because of their exceptional strength, toughness, and versatility. Below are the key benefits supported by technical parameters from leading industry sources:
Increased Strength and Durability: The tensile strength of high-tenacity polyester filaments is much higher than that of regular polyester fibers. In most cases, this increased strength is measured in fineness (D), with high-tensile filament often exceeding 1000 D, making them suitable for demanding applications such as outdoor textiles, automotive fabrics, and industrial harnesses.
Low Moisture Absorption: One of the technical parameters of high-tenacity polyester is its low moisture regain (<0.5%), which leads to quicker drying times and lighter weight for any application where moisture management is essential. Thus, products remain lightweight even under humid conditions without losing resilience.
Excellent UV Resistance: High-tenacity polyester filaments usually have good UV stability, with many hours rated between hundred and more than one thousand hours when experimentally exposed to UV rays. This factor is critical for items meant for outside use as it prevents degradation and ensures that the composition holds together without agitation under long exposure to sunlight.
Manufacturers can enhance performance by using high-tenacity polyester filaments while maintaining continued service in harsh or highly stressed environments.
Polyester Yarn vs. Other Filaments in High-Performance Uses
Some technical parameters, revealed from experts’ opinions and top sources, highlight the performance of polyester yarn compared to other filaments.
Tensile Strength: Polyester yarn, especially high-tenacity types, possesses tensile strengths similar to those of nylon and aramid fibers. For example, the range of high-tenacity polyester may be between 700 and 1500 Denier, while nylon can go as high as 2000 Denier in certain applications, making it usable in various demanding uses, among them safety harnesses and industrial.
Moisture Management: High-tenacity polyester has a very low regain (about 0.4 to 0.5%), much lower than natural fibers like cotton (up to 8%). This leads to lower moisture absorption, resulting in faster drying times and less weight, which is key for outdoor and performance textiles.
UV Stability: Polyester yarn always outperforms other filament varieties, such as polypropylene, which is less resistant to UV degradation. For instance, polyester maintains its strength and color in sunlight for over five hundred hours, thereby emerging as an ideal choice for sun-exposed applications like awnings and outdoor gear.
To sum up, even if the strength-to-weight ratio of premium synthetic fibers, including aramid, may not be matched by polyester yarn at all times, combined properties of endurance, moisture management, and UV resistance make this material quite competitive for use in high-performance scenarios. In this regard, the outdoor textiles and automotive fabrics industries have been greatly advantaged by these aspects, which provide confidence when operating under extreme conditions.
Ensuring High Durability and Performance in Applications
Several technical parameters are crucial to guarantee high durability and performance in high-tenacity polyester applications. According to research findings from leading industry websites, the following should be taken into account:
Tensile Strength: Depending on the application, it is essential to choose a particular polyester yarn whose tensile strength lies between 700 Denier and 2,000 Denier. This ensures that it can resist large amounts of force without breaking, making it ideal for safety harnesses, outdoor gear, and industrial use.
Moisture Regain: Opt for low moisture regain (0.4-0.5%) high-tenacity polyester fabric. If prolonged moisture retention could cause discomfort and affect performance, such as in sports/leisure wear or outdoor textiles frequently used in perspiration situations, quick-drying fabrics will be required.
UV Resistance: Good polyester fabric should maintain UV stability of up to 500 hours when directly exposed to sunlight. This makes it particularly useful for awnings and outdoor gear that will suffer material degradation if not carefully designed.
Thermal Stability: Make sure that the polyester being used has a temperature range between -40°C and +150°C. This property is necessary in applications where there might be fluctuations in temperature, preventing shrinkage and loss of strength.
By painstakingly considering these technical parameters together with their rationales, users can select polyester materials that exceed performance expectations even in harsh environments rather than just meeting them. This approach ensures dependability across different industrial applications, thus improving the overall quality of products manufactured from these types of high-performance materials.
Frequently Asked Questions (FAQs)
Q: What is polyester high-tenacity yarn?
A: Polyester high-tenacity yarn is made using polyester fibers that have been treated chemically to make them stronger. This type of thread has a high degree of toughness and thus can withstand heavy usage, making it useful in items such as stitches and airbag fabrics.
Q: What applications can benefit from polyester high-tenacity yarn?
A: Polyester high-tenacity yarns are suitable for sewing threads, airbags, geotextiles, and industrial fabrics. The material’s strength offers an advantage in these sectors while, at the same time, it is flexible enough for versatility.
Q: How is high-tenacity yarn different from regular polyester yarn?
A: The process of reinforcing lightness and toughness involving chemical alteration makes it more resilient than other thread types. High strength is achieved by making alterations on the molecular level, such as increasing the number of filaments with better performance in challenging functions.
Q: What are the benefits of using high-tenacity yarn containing multifilament structures?
A: Multifilaments add more strength, elasticity, and durability to the fabric made from them. It is, therefore, ideal for making airbags and sewing threads, which require solid and rigid materials out of their utility.
Q: What is FDY, and how does it relate to high-tenacity polyester yarn?
A: Fully Drawn Yarn (FDY) denotes one kind of polyester whose tensile properties have been maximally enhanced through stretching. As a result, FDY may also be produced as an HTY when applied in industries that deal with tension-sensitive applications like sewing thread or geotextiles.
Q: Why is chemical resistance important for high-tenacity polyester yarn?
A: Chemical resistance prevents damage by chemicals so that even after coming into contact with corrosive substances, the thread continues to be strong, intact, and lasting. This is essential in industrial applications where the exposure to chemicals is high.
Q: What is the tenacity range of high-tenacity polyester yarn?
A: The strength of high-tenacity polyester varies from about 60 to 85 cN/tex. This means that materials that require strong end products can be made out of them since they are also durable.
Q: Is high-tenacity yarn available in different forms?
A: Yes, there are several varieties of high-tenacity yarn, such as Multifilament, spun yarns, and synthetic polymer filament-containing yarns, each with its distinguished characteristics for various applications with defined performance requirements.
Q: What makes halide yarn suitable for high-performance applications?
A: Hailide yarn is a type of HTY recognized for its superior strength and durability. Such ropes are perfect for use in manufacturing industries where sturdy material is required; airbag fabrics, sewing thread, and other industrial textiles correspondingly fall into this category.
Q: How does using yarns with high-tenacity filaments impact product quality?
A: Incorporating such threads into the final process leads to significant enhancement in product quality. It also makes the thread very strong and durable, making it fit for use in airbag fabrics or other industrial textiles under extreme conditions.