Although threads are important in sewing and textile production, they are rarely given the needed consideration. This article discusses some of the arguments that sewing factories consider before sourcing sewing threads, like choosing the appropriate thread for strength and quality. Threads used in sewing vary in appearance, walkability, and usage, and as such many sewing factories do have local and International suppliers with whom they can meet all their production requirements. Also discussed is how thread cost, quality, and accessibility affect the decision-making process. Readers will appreciate and understand how critical thread sourcing is within the sewing industry after familiarizing themselves with the complex supply chain and management strategies threads hinge on.
How Do Sewing Factories Source Their Sewing Thread?
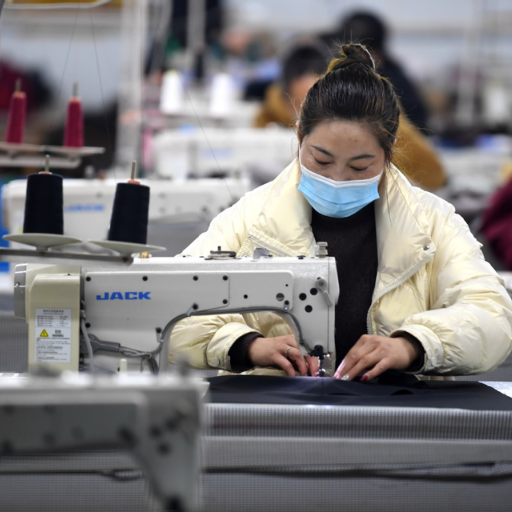
Sewing factories evaluate their prospective suppliers for the sewing threads based on quality, efficiency, and reliability which serve as their key factors. The standard procedure starts by looking for suppliers who can provide a specific thread type alongside matching the required tensile strength and color consistency. Factories work alongside domestic and foreign manufacturers to establish the cost, lead times, and bounded stability of the supply chain. In addition, the durability of the threads is evaluated through a standardized testing process to determine their performance during different sewing conditions. Putting in great effort in regulating suppliers led to the stringent quality control sewing factories have to meet the demands of their threading materials for their production processes.
What Types of Threads Are Commonly Used?
Sewers primarily chose polyester, cotton, and nylon threads because of their wide range of applications and many other qualities. Polyester threads are popular because they are strong, durable, and mildew-resistant, making them ideal for heavy-duty stitching. Unlike polyester, cotton threads are naturally composed and smooth in finish which is why they are preferred in quilting and lightweight softer fabrics. Nylon threads, on the other hand, are preferred in segments where durability is critical due to their high tensile strength and elasticity. These threads are most often used in upholstery, leather goods, or anything industrial. These threads are produced in various weights, finishes, and constructions to meet the needs of different sewing projects including spun, core-spun, or filament.
How Is Thread Production Organized?
The production of a thread is a meticulous process that is broken down into steps. Every step guarantees quality and uniformity. It starts from raw material selection that can either be natural fibers like cotton or synthetic fibers such as polyester and nylon. These raw materials go through a cleaning and combing stage to transform them into filaments which are then twisted together to form individual yarns. This twisting process is conducted in a very calculative way to achieve the appropriate texture, elasticity, and strength. Later on, the thread is subjected to advanced colorfastness and uniformity techniques to allow the dye to soak in. After that, the threads are waxed or lubricated to boost their performance during the sewing stage. In the final stages, the threads are wound onto cones or spools and are thoroughly examined for signs of defects before being packaged for supply to numerous industries. By breaking down the thread manufacturing process into these steps, reliable threads are produced for any application.
What Role Does Thread Size Play in Sourcing?
Thread size affects sourcing because it influences the strength, look, and use of the end product. Finer-sized threads like denier, Tex, or ticket numbers are used in softer fabrics like silks and lightweight garments since delicate seams are needed. Larger thread sizes are meant for heavy-duty uses like sewing upholstery or denim. The size of the thread also determines the needle, machine, and tension settings during sewing to help maintain smooth processes and avoid ruining the materials. Effective sourcing needs consideration of the end-use application, fabric type, and production processes such as optimization of performance and aesthetics. All of this culminates to ensure that the right amount of thread size is guaranteed for the project.
What Materials Are Used in Garment Threads?

Threads used in garment production are typically made from a variety of natural, synthetic, and blended materials. Common natural materials include cotton, which is valued for its softness and versatility, and silk, known for its strength and smooth finish. Synthetic options, such as polyester and nylon, are favored for their durability, elasticity, and resistance to wear and tear, making them suitable for high-performance or heavy-use applications. Blended threads, which combine natural and synthetic fibers, offer a balance of strength, flexibility, and aesthetic appeal, meeting diverse manufacturing needs. The choice of material depends on the desired qualities of the finished product, including strength, appearance, and durability.
How Is Polyester Thread Produced?
The initial stages of polyester thread production involve the synthesis of polyester polymer mainly through polymerization. This process entails the reaction of purified terephthalic acid (PTA), or dimethyl terephthalate (DMT), with monoethylene glycol (MEG) while applying heat and pressure. After the polymer formation, the mixture is melted and forced through spinnerets to form continuous filaments. These filaments are then cooled to solidify. The cooled filaments are then stretched to draw them which realigns the molecular structure and increases strength and elasticity. The drawn filaments intended for thread making may be twisted and colored before being treated to further enhance their abrasion and UV resistance. The spools are finally switched for various textile applications.
Why Is Nylon a Popular Choice?
Nylon fabrics are well known for their strength, durability, and versatility, which are some of the reasons they are popular today. Nylon has a high resistance to abrasion, chemicals, and moisture which makes it ideal for harsh environments. While nylon fibers are lightweight, they are also resilient, allowing for superior elongation and recovery, thus increasing flexibility. Moreover, nylon being easy to dye provides a vast range of color choices. Because of the low moisture absorption, dimensional stability is ensured in changing conditions. These factors, along with cost-effectiveness and adaptability to different manufacturing processes, have made nylon the primary choice in many industries, from engineering to textiles.
Understanding the Benefits of Corespun Thread
Corespun thread is created by taking staple fibers like cotton or polyester and wrapping them around a filament core (commonly made from polyester or nylon). This construction combines the durability of the core filament with the flexibility and softness of the outer fibers. Corespun threads have several constructive advantages over sewing thread including the ability to withstand higher stress without breaking. Corespun threads also offer high abrasion resistance. These characteristics make sure seams remain intact on high-wear applications. Their superior elasticity maintains the seam integrity of stretch fabrics by reducing puckering and improving seam appearance. Moreover, core-spun threads excel in high-speed sewing, thanks to their minimal core thread breakage. These threads are high-performing, compatible with most bases, and increase production efficiency which is why they are commonly used in apparel and upholstery manufacture.
What Are the Steps in Thread Manufacturing?
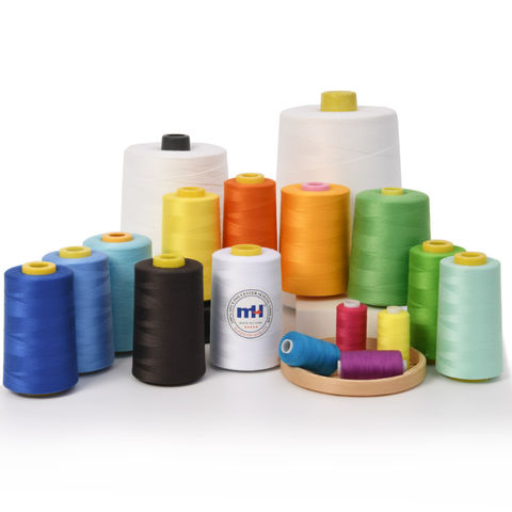
- Fiber Selection and Preparation: Raw fibers, such as cotton, polyester, or nylon, are carefully selected based on the desired thread properties. These fibers are then cleaned and processed to ensure uniformity and quality.
- Blending and Spinning: Fibers may be blended for specific characteristics, such as strength or elasticity. The blended fibers are spun into yarns through processes like ring spinning or open-end spinning.
- Core Formation (if corespun): For corespun threads, a continuous filament core is introduced during the spinning process, around which staple fibers are wrapped.
- Twisting: Single yarns are twisted together to achieve the required thread thickness and strength. This process can vary depending on whether the thread is two-ply, three-ply, or more.
- Finishing: The thread undergoes various finishing treatments, such as singing, lubricating, or dyeing, to improve performance, appearance, and compatibility with specific applications.
- Winding and Packaging: The finished thread is wound onto spools or cones and inspected for quality before being packaged for distribution.
These steps ensure the production of high-quality threads that meet the technical requirements of various applications.
How Does the Spin Process Affect Quality?
The spin process significantly impacts thread quality by influencing key characteristics such as strength, uniformity, and texture. Methods like ring spinning tend to produce stronger and finer threads with better elasticity, making them ideal for high-end applications. Conversely, open-end spinning is faster and cost-effective but may result in coarser and less robust threads due to reduced fiber alignment. The twist applied during spinning also plays a critical role, affecting the thread’s tensile strength and its resistance to abrasion or breakage. Furthermore, factors such as spinning speed, fiber length, and blending techniques directly correlate with the thread’s performance consistency, highlighting the importance of precision during the spin process to meet specific quality standards.
The Importance of the Twist in Threads
The twist in threads is a critical determinant of their mechanical and functional properties. Twist refers to the spiral arrangement of fibers in a thread, which directly influences strength, durability, and elasticity. A higher twist level typically enhances tensile strength, as fibers are bound more tightly, reducing the chance of breakage under tension. However, excessive twisting can make the thread stiffer and less flexible, which may limit its suitability for certain applications.
Conversely, a lower twist level results in softer and more pliable threads, which are favored for comfort-oriented uses like fabrics for clothing but may compromise tensile strength and abrasion resistance. The twist also contributes to the thread’s appearance and functionality, as uniform twisting ensures smoother surfaces, reducing lint formation and providing a more consistent texture. Optimizing twist parameters—such as twist per inch (TPI) and twist direction (S-twist or Z-twist)—is essential to balance these properties, ensuring the thread meets its intended application requirements.
How Is Dye Applied to Thread?
Dye application onto threads is a methodical process that guarantees the intended color quality and performance. The typical procedure of dyeing involves soaking threads in a water solution containing dyeing agents and some fixing additives. The process starts with pre-treatment steps like scouring or bleaching which remove contaminant residues from the fibers for optimal dye seated.
When threads are ready, they are dunked in the dye bath that is controlled in temperature, pH, and Turbulence Type for saturation level. High-temperature or pressure dyeing techniques can be utilized to ensure proper dye binding on synthetic fibers. Following dyeing, the threads are subjected to post-treatment steps like rinsing to the unfixed dye and fixing for better color panting over-vigorous washing, friction, and UV light.
Modern methods of dyeing are inclusive of continuous dyeing where threads are dyed in motion while passing through the dye pads and fixing chambers or space dyeing which is used for multi color patterns. Each method of dyeing varies depending on the thread material, its probable use, and the color qualities that are needed.
How Do Industrial Sewing Threads Differ?
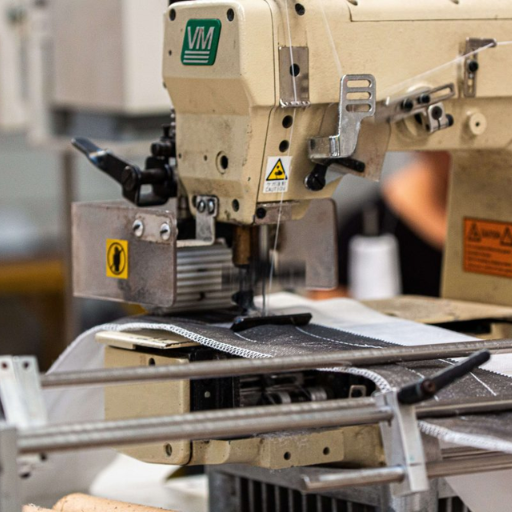
Because of their strength and durability, industrial sewing threads are distinct from regular threads. Tailored for high specific demand applications, these threads are made from synthetic materials like polyester, nylon, or aramid which have greater tensile strength and are resistant to abrasion, chemicals, and extreme heat. Unlike standard threads, industrial threads are treated with coatings or finishes to enhance lubricity and reduce friction during sewing at very high speeds. Moreover, industrial threads have a uniform cross-section with controlled elongation so accurate stitches can be made in critical places in automotive upholstery and protective clothing. Their performance is tailored to satisfy the functional and aesthetic needs of mass production.
What Makes a Good Sewing Thread?
Strongness, consistency, and compatibility with intended materials stem from the essence of application threads. This is similar to other industrial sewing threads where they have a critical characteristic blend of high tensile strength, uniform thickness, and minimal lint. The most lavished threads consist of just the right percentage of elasticity which grants the thread flexibility, without breaking or puckering the fabric. Resistance to moisture, UV rays, and chemicals are also crucial, especially for outdoor or industrial applications. Lastly, even dying helps ensure color fastness and guarantees zero discoloration with time. These qualities are essential for efficiency, durability, and aesthetic uniformity in sewing projects.
Understanding Sewing Performance Requirements
The boundary sewing performance basics include the intertwining of the yarn, the fabric, and the sewing process. For example, essential considerations include the thread’s ratio of strength to its worm and watching the relief of forces acting upon whim during the processes of creation. The type of thread fiber is important too; while polyester threads are used due to the fact the threads are strong and flexible, cotton threads achieve softer looks and more natural looks and finishes. The formation of control stitches is dependent upon a certain thread tension level and sewing machine acceptance which reduces the amount of stitch skips and guarantees the thread commits the remaining seam quality index. The fabric’s nature also the cover have to require separate sizes of needles and kinds of threads according to the intended usage industrial, family, and even artistic. Thread lubricating also improves the performance of sewing machines by lowering friction and abrasion. Complying with these requirements makes it possible to produce reasonable, reliable, high-quality stitches in different sewing conditions.
Exploring the Thread Market for Industry Use
Given the global demand for enhanced performance and sustainability, the thread market is continuously developing. The local polyester thread market is the most significant due to its strength and elasticity, along with its resistance to chemicals, making it useful in industrial sewing and outdoor textiles. For industries that require aesthetics along with eco-friendly production practices, cotton retains its importance. The current innovations focus on threads such as Kevlar and Nomex, which are important for industrial sewing in the aerospace, automotive, and protective clothing industries because of their heat and abrasion resistance.
Sustainability is the growing concern among consumers alongside manufacturers. Eco-friendly and biodegradable threads are gaining popularity globally. The increasing incorporation of PET threads and organic cotton from GOTS certified agencies are an example of this.
The Asia-Pacific region produces the most threads because of their vast textile production capacity and cheaper labor. At the same time, Europe and North America focus on more specialty and sustainable thread solutions. There has been increasing emphasis on customizability from everyone’s own specific application, for example, healthcare textiles that require antimicrobial treatments as well as water-repellent threads for outdoor gear. All of these, together with modern advancements such as computer-aided thread behavior modeling, highlight the thread market’s continuous innovation and strategic alignment with the industry.
How Does Thread Size Impact Sewing Machine Efficiency?
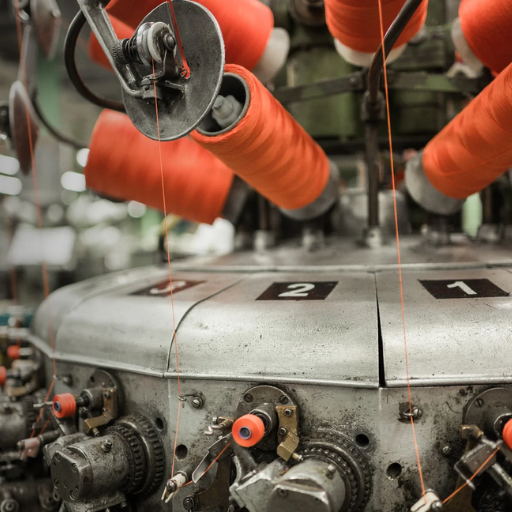
Machining thread sizes and their determinate efficiency parameters on sewing machines, including performance, durability, and stitch quality, is crucial. Typically, larger thread sizes are used in heavy-duty applications as they offer greater strength. However, they require adjustments to tension settings and needle size; otherwise, the machines do not function smoothly. On the other hand, smaller thread sizes work best on lightweight fabrics and intricate stitching, although it is much easier to break them if not handled with absolute care. If the thread size does not match with the machine being used, or the material being utilized, several problems like skipped stitches, uneven tension, and aggravation of wear, on the components of the machine, arise. This underpins the sonic boundaries of selection processes for sewing thread sizes around machine efficiency.
Choosing the Right Needle of the Sewing Machine
A sewing machine’s efficiency, quality of stitches, and wear levels are largely governed by the choice of sewing machine needles. Users should always consider three factors – needle size, type, and compatibility with thread and fabric. Sizes of needles and their corresponding sizes, for example, heavier fabrics such as denim require larger needles size 16/100, while delicate fabrics such as silk require needles size 9/65. Needle types such as universal and ballpoint need to be by the material, for example, sharp needles work for woven fabrics, however, ballpoint needles are more appropriate for knits as they do not easily damage the fabric.
The wider context of needle selection includes the condition of the needle, which is equally as important; for example, a needle fired too much may be worn resulting in skipped stitches and fabric snags or other unforeseen machine problems. It is best practice to replace the needle after every major project or do so regularly. Additionally, referring to your sewing machine manual is advisable to check for proper needle selection as incorrect options can easily induce tension, thread breakage, or damage the machine. Maximizing needle selection based on these factors can help the machine work to the best of its capabilities and improve the quality of stitches produced.
Managing Thread Tension for Optimal Results
Any embroidery or stitching job has to consider thread tension as one of the most crucial factors in the scope of achieving the utmost professionalism. Balanced tension is what makes stitches smooth and effortless, with the top thread and bobbin thread interlocking seamlessly between layers of fabric. On the other hand, incorrect tension can lead to sleeve cuts or breaks of threads, uneven stitches, or puckering.
To modify thread tension, the first step is to check the manual of your sewing machine. Not all models work similarly; some have different mechanisms and tension-altering settings. Usually, lower tension is achieved using a number dial and higher ranges can increase it, which is what most machines operate on. Before making permanent adjustments, always conduct tests on scrap fabric to ensure accuracy. If the stitches appear to show upside-down loops, then I hypothesize that the bobbin rotation has been loosened too much, and vice versa if the holes were covered on the top of the garment stitches.
Alongside the environmental ones like the type of thread being used, the size of the needle, and the texture of the fabric are other factors that determine tension. Bearing the suggestions from the manufacturers will ensure you are using suitable components. Consistency and longevity in machine performance are greatly enhanced by maintaining it through regular cleaning of tension discs and indecently wound bobbins. For optimal output and uninterrupted workflow, tension should be adequately managed.
How to Prevent Thread Damage During Sewing
Like any other activity, sewing can be quite delicate as thread damage can occur if one is not educated on the most impactful parts. A higher-level discussion can be had around indicating that thread functionality is associated with integrity. To begin, lower-quality threads, in comparison to higher-quality ones, have a higher likelihood of breakage which alone is why quality threads that are suitable for certain fabric and sewing tasks are imperative. Additionally, be certain of your needle size and type; sharp needles without the correct size or type tend to melt apart and create friction, snapping the thread instead. An important point to mention is making sure that needles on your sewing machine are replaced when need be, as old needles deficit optimal output.
In addition, some considerations need to be addressed. Starting with other threads above or bobbin threads; upper set threads need attention as well. Stresses that lead up to the thread being damaged can arise from places like the tipping over or lead to an imbalance of both. Ensure that lack of tension or tightness unhindered above can lead to support and basic cleaning of one’s sewing machine to take place as well. Finally, from the learned discussion points, there should be more of a consideration of the tension settings placed on the sewing machine. When placed too firmly, breakage is eminent due to the above damage and stress created. One phrase holds, sewing will capture “yay” or “nay” from mishap, and good sewing combined with these well-crafted approaches will mean providing oneself the opportunity to use some stress-free, smooth, and professional sewing.
References
Frequently Asked Questions (FAQ)
Q: Where do sewing factories source their sewing threads?
A: Sewing factories typically source their sewing threads from specialized manufacturers who produce a wide range of threads suitable for different applications. These manufacturers produce a variety of threads, including cotton thread, polyester sewing threads, and nylon sewing threads, which are chosen based on the specific requirements of the garment or product being made.
Q: What types of yarn are commonly used in sewing threads?
A: The types of yarn commonly used in sewing threads include cotton, polyester, and nylon. Each type of yarn offers distinct properties, such as strength, elasticity, and resistance to abrasion, making them suitable for different sewing applications and ensuring good sewing performance.
Q: How does the choice of thread impact the seams in garments?
A: The choice of thread significantly impacts the seams in garments by affecting their strength, flexibility, and durability. A suitable thread must be selected based on the fabric type and end-use to ensure that the seams can withstand the stress and wear of everyday use without breaking or fraying.
Q: Are synthetic threads commonly used in the sewing thread industry?
A: Yes, synthetic threads, such as polyester and nylon, are commonly used in the sewing thread industry. They are valued for their strength, abrasion resistance, and ability to maintain color and integrity through the washing process, making them ideal for various sewing applications.
Q: What is the role of continuous filament in thread production?
A: Continuous filament plays a crucial role in thread production by providing a smooth and consistent thread that is ideal for high-speed sewing and producing fine, even stitches. It is often used in the production of synthetic threads, such as polyester and nylon, to enhance their sewing performance and surface characteristics.
Q: How does the sewing thread protect from abrasion during the sewing process?
A: Sewing thread protects from abrasion during the sewing process through its construction and material properties. Threads made of strong fibers such as polyester or nylon possess high resistance to friction, ensuring that they maintain their integrity and do not fray or break during sewing.
Q: What distinguishes embroidery thread from regular sewing thread?
A: Embroidery thread is distinguished from regular sewing thread by its sheen and softness, which provide a decorative finish to garments and textile products. It is often made from silk, rayon, or high-sheen polyester, and is used specifically for embroidery applications to create intricate designs.
Q: What factors influence the choice of thread for sewing garments?
A: The choice of thread for sewing garments is influenced by factors such as the fabric type, the garment’s end use, and the desired sewing performance. Threads must be chosen to complement the fabric’s weight and texture and to ensure that the finished sewing is durable and aesthetically pleasing.
Q: How is the quality of sewing threads ensured before use in garment production?
A: The quality of sewing threads is ensured through rigorous testing for strength, colorfastness, and abrasion resistance. Manufacturers conduct these tests to verify that the threads meet industry standards and are suitable for their intended sewing applications, thereby ensuring reliable performance in garment production.