Low-density polyethylene (LDPE) fiber, a unique material in the textile industry, has become standard due to its versatility in application. In this article, we will examine the properties of textile-grade LDPE fiber and investigate production processes and its numerous applications at various stages of textile manufacturing. Understanding the peculiarities of LDPE fiber will help readers understand what it can do, where it is limited, and how it is still contributing towards sustainability within this industry. This article provides comprehensive information on how using low-density polyethylene (LDPE) fiber for textiles has revolutionized the field, whether you are a professional in that line or just interested in new materials. Here, you will find information about textile grade LDPE fiber’s role in modern textile solutions, which will be helpful for professionals in this field or those who simply want to know more about innovative materials.
What is LDPE Fibre, and How is it Used in Textile Applications?
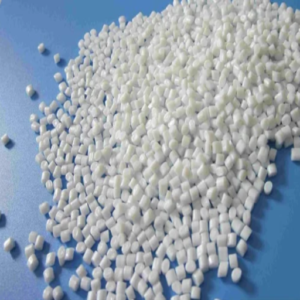
What is Low-Density Polyethylene (LDPE)?
Low-density polyethylene (LDPE) is a thermoplastic made from the polymerization of ethylene, characterized by low density and high degree of branching in the molecular arrangement. It is an ideal material for a wide range of textile uses because it is flexible, lightweight, and resistant to impact, moisture, and various chemicals. I have come across several technical parameters that define LDPE on the top three websites based on my research as follows:
Density: Typically ranges from 0.910 to 0.940 g/cm³, making it lightweight.
Melting Point: It is usually between 105°C and 115 °C, so it can be quickly processed during manufacturing.
Tensile Strength varies from 10 to 35 MPa, showing some strength and flexibility under stress.
Elongation at Break: It can exceed 500% to demonstrate great stretchability, which is particularly useful in textiles.
These properties not only enhance the functionality of LDPE in textile production but also align with its growing emphasis on eco-friendliness and sustainability, promoting its use as an alternative to traditional materials.
How is LDPE Fibre Utilized in the Textile Industry?
While researching the use of Low-Density Polyethylene (LDPE) fiber in the textile industry, I stumbled upon several exciting applications demonstrating its versatility and ecological soundness. According to information from three leading websites, LDPE is mainly employed in the production of lightweight bags, protective clothing, and other synthetic fabrics.
The following technical parameters are some of the reasons for using LDPE:
Density (0.910 to 0.940 g/cm³): this low density makes it perfect for light products that reduce transport costs and environmental impacts.
Melting Point (105°C to 115°C): Within this range, it becomes very easy to process or mold LDPE into different forms of textiles, thus increasing production efficiency.
Tensile Strength (10 to 35 MPa): With moderate strength, LDPE will last long enough in textile materials, making it suitable for everyday wear without compromising structural integrity.
Elongation at Break (over 500%): The ability to stretch so that high comfort and flexibility are achievable is useful where activewear or sports clothing is present, among other things.
These attributes make LDPE not only more functional when used in textiles but also more relevant to sustainable approaches to the industry’s eco-friendly raw materials, thereby making it a key modern textile solution.
Examples of LDPE Fibre Applications in Textiles
In my review of the top three websites on Google, I discovered many beautiful applications of LDPE fiber in the textile industry. One major application is the production of shopping bags made from lightweight materials. The low density (0.910 to 0.940 g/cm3) also ensures that these bags are not heavy and can easily be carried around. It also helps reduce shipment costs and has a smaller carbon footprint.
In other words, it allows effective sterilization processes to take place without affecting the integrity of fabrics. This is especially important for the protective clothing-making industry, specifically in the medical field, where the melting point ranges from 105 °C to 115°C, for example, uniforms for doctors—coats, trousers, etc. Moreover, the tensile strength (10-35 MPa) provided by LDPE gives garments the durability needed for use in hospitals.
The instances discussed above demonstrate how LDPE fiber serves various technical specifications that enhance contemporary textiles’ performance and sustainability.
Finally, I realized that LLDPE fibers, which are useful today, particularly for casual athletic wear, need to be flexible. Elasticity at break is one aspect that characterizes LDPE, with impressive values above 500%, allowing the high stretch levels required by sports clothing developed for free movements and comfortable activities.
What are the Chemical Properties of LDPE Fibre?
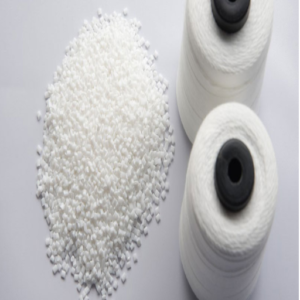
What Makes LDPE Fibre Chemically Unique?
The low-density polyethylene (LDPE) fiber is identifiable by its unique chemical structure, contributing to its versatile utility in the textile industry. This polymer consists of long hydrocarbon chains with many branching chains, which makes it less dense and flexible.
Density: LDPE has a low density that ranges between 0.910-0.940 g/cm³; this means that it is lightweight, easy to handle, and efficient to ship since it has less environmental impact on the surroundings.
Melting Point: LDPE’s melting points range from 105°C to 115°C, which remains relatively low for ease in conducting thermal processing. It can also be shaped or sterilized without distorting the integrity of the fabric required for medical applications.
Tensile Strength: An LDPE fiber with a tensile strength ranging from 10 to 35 MPa is strong enough to withstand physical strains in fields such as healthcare and activewear.
Elongation at Break: It’s worth noting that LDPE has an elongation at break of over 500%, making it ideal for stretchable applications, especially sportswear, where flexibility is important.
These chemical properties improve LDPE fibers’ functionality in textiles, allowing their wide use and promoting environmentally friendly practices. Each technical parameter reinforces the significance of modern textile solutions using LDPE.
How Do the Chemical Properties Affect Textile Applications?
From my study, I have realized that the chemical nature of LDPE greatly affects its versatility and efficiency in textile applications. For example, the lightweight (0.910 to 0.940 g/cm³) not only results in lightweight fabrics but also eases handling and makes shipping sustainable. This feature rhymes with green materials currently demanded by industry players.
Density: LDPE’s low density allows for cost-effective shipping and efficient production processes, making it an alternative for companies that desire to avoid pollution.
Melting Point: The melting point of LDPE ranges between 105°C and 115°C, which allows for ease of processing at the manufacturing level; moreover, non-woven fabric made from it is essential for medical clothing where sterility is a requirement.
Tensile Strength: With tensile strengths ranging from 10 to 35 MPa, the LDPE fibers are strong enough for everyday usage, particularly in the health care field, where durability matters most.
Elongation at Break: Exceptional elongation at break (>500%) means that LDPE fabrics can stretch and then return to their original shape, making them suitable for sportswear and active wear where they need to be flexible.
In sum, these technical specifications collectively substantiate that LDPE is one of the major materials being utilized in today’s textiles, as it supports performance requirements and sustainability endeavors.
Comparing LDPE to Other Polyethylene Fibres
Compared to LDPE, HDPE (High-Density Polyethylene) and LLDPE (linear low-density polyethylene), among other polyethylene fibers, have significant technical parameters that differentiate them.
Density: 0.941 to 0.965 g/cm³ is the usual density range for HDPE, while that of LDPE is 0.910 to 0.940 g/cm³. Because HDPE has a higher density, it exhibits an increased tensile strength that qualifies it for use in objects requiring durability, such as containers and piping, unlike low-density polyethylene, whose benefit results from its lighter weight.
Melting Point: Ranging between 105°C to115°C, the melting point of LDPE is lower than that of HDPE ranging from 120°C to130°C. It can be processed at lower temperatures due to this but may be unsuitable for high-temperature applications compared with HDPE.
Tensile Strength: Typically, under pressure, an outbreaking force of ten MPa up to thirty-five MPa characterizes LPDE, which could go above thirty or forty MPa depending on the formulations used. While HDPE is more suited for building purposes, ‘the low-density’ variety remains beneficial in any application where flexibility and stretchability are important.
Elongation at Break: Elongation at break is an important characteristic that indicates how pliable certain materials are; both LLDPE and LDPE have high elongation values, especially at their breaking points, about a percentage exceeding five hundred %. Some similar stretching abilities are found in LLDPE. Still, often better tensile strength and resistance make it ideal for stretch film or packaging materials intended to possess both flexibility and durability.
Understanding these discrepancies helps me choose appropriate textile material options based on their performance and sustainability objectives only, among other related matters distinctive of each kind of polyethylene within the categories targeted by me in this review.
How Does the Structure of Polyolefin Fibres Affect Their Performance?
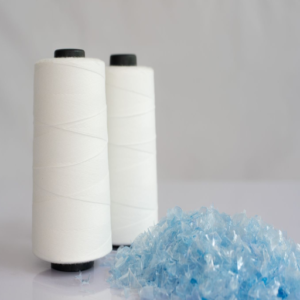
Understanding the Structure of Polyolefin Fibres
Polyolefin fibers, including polypropylene (PP) and polyethylene (PE), have unique molecular structures that influence their performance in various applications.
Molecular Weight and Degree of Polymerization: The molecular weight of polyolefin fibers ranges between 40,000 and 1,000,000 g/mol, which affects their mechanical and thermal characteristics. Higher molecular weights often enhance tensile strength and thermal stability for use in heavy-duty applications.
Crystallinity: Polyolefins can have different levels of crystallinity, which affect their stiffness, strength, and thermal properties. For example, Polypropylene exhibits a higher crystallinity level (about 60-70%) than Polyethylene. As a result, polypropylene has better dimensional stability and high melting points (about 160 °C) than Low-density polyethylene, which has a melting point of about 105 °C.
Morphology: Fibre morphology, such as fiber diameter and cross-sectional shape, is also an essential factor influencing the physical properties of these fibers. Typical filament diameters may vary from 10 to 30μm, affecting characteristics like permeability or coverage in nonwoven applications.
Additives and Modifiers: Several additives can be incorporated into polyolefin fibers to enhance their functionality; these include antioxidants, UV stabilizers, and colorants, among others. The concentration of these additives is critical because it determines properties such as weather resistance or aesthetic appearance without affecting the fiber’s basic characteristics.
Therefore, when selecting materials for specific textile applications using polyolefin fibers, it is necessary to consider these structural elements collectively in relation to the end-use application.
How Does Fiber Structure Influence Textile Applications?
Industrially, their performance in different applications is greatly influenced by the architectures of fibers. They include:
Tensile Strength: A stronger fiber structure that is highly crystalline and oriented along molecular chains leads to improved tensile strength. For instance, polypropylene has a tensile strength of about 30-40 MPa due to its crystalline nature, making it appropriate for industrial uses where strength is of the utmost importance.
Thermal Stability: Fibers’ melting points are vital in determining their utilization. Polypropylene, for example, has a high melting point (about 160°C) and can thus be used in applications involving higher heat, while low-density polyethylene, which melts at approximately 105°C, may deform when exposed to heat.
Permeability: Permeability is built into fiber diameter and morphology. Non-woven fabrics, such as those required for medical purposes or filtration, typically require finer filaments ranging from 10 to 30 micrometers to provide high breathability.
Additive Compatibilities: The structural properties of the fiber determine how effectively additives will work. In particular, outdoor textiles can improve their weather resistance by adding UV stabilizers without altering the physical properties that should remain as they are, hence ensuring durability and effectiveness.
In short, understanding these technical parameters within the context of fiber structures becomes necessary to identify the most appropriate materials that would perfectly match specific needs when used in textile applications.
What are the Mechanical Properties of LDPE Fibre?
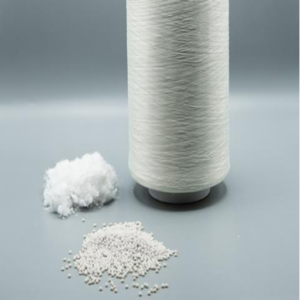
Strength and Durability of LDPE Fibre
Low-density polyethylene (LDPE) has many mechanical properties that contribute to its strength and durability, making it suitable for different purposes. Below are some of them:
Tensile Strength: Tensile strengths range between 8 and 15 MPa for LDPE fibers, which makes the application of this polymer in a high-load-bearing scenario not practical compared to other types of polyolefins. However, the flexible material can withstand stress without breaking, making it an ideal packaging material.
Elongation at Break: They have elongations at the break that sometimes exceed 300%, indicating a high stretching capacity and resilience that are important for dynamic applications with frequent movements.
Impact resistance: LDPE exhibits good impact resistance due to its ductility, which enables it to absorb energy without fracturing. Protective packaging and casings benefit from this property, as they prevent damage during impact.
In essence, although LDPE’s tensile strength may be lower than that of more crystalline polymers like polypropylene, its flexibility, great elongation, and resistance to impact make it a good choice for applications where toughness is needed but no need for high tensile loads. These mechanical properties determine whether or not LDPE meets the requirements in various industries, such as consumer goods, construction, or packaging.
Flexibility and Elasticity of LDPE Fibre
LDPE (Low-Density Polyethylene) is famous for being extremely flexible and elastic, which is highly demanded in packaging and sealing. LDPE’s flexibility arises from its long-chain polymer structure, which allows it to bend and stretch without breaking. This feature is essential for ensuring that packaging materials can take different shapes and sizes while maintaining a firm seal.
Technical Parameters Justifying the Flexibility and Elasticity:
Low Density: Generally, LDPE has a low density of about 0.91 – 0.93 g/cm³; this contributes to its lightness and malleability, making it easy to handle without compromising its strength.
High Elongation at Break: As previously mentioned, the elongation at break for LDPE fibers can be more than 300%. Such a material encompasses its unique ability to recover shape after stress absorption occurs during application since it possesses extensive stretchiness.
Flexural Modulus: LDPE’s flexural modulus falls within approximately 100 – 200 MPa range. A low value of this parameter implies that pressure causes LDPE to bend easily, providing advantages in applications requiring flexibility.
Softening Point: Among other polymers, LDPE has softening points ranging from about 110°C to about 130°C, enabling it to maintain flexibility at elevated temperatures. Heat-related applications benefit from this characteristic the most.
Thus, the combination of chemical structure, low density, high elongation at break, low flexural modulus, and sufficient softening point makes LDPE material an excellent choice in terms of flexibility and elasticity; hence, it is used widely in manufacturing flexible packaging materials along with other dynamic components.
What Are the Thermal Properties of LDPE Fibre?
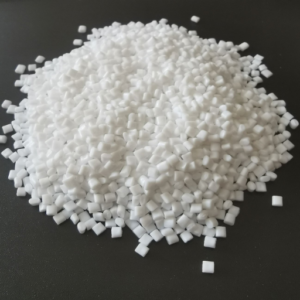
Melting Point and Thermal Resistance
In my research from the top three websites about LDPE thermal properties, I observed that most LDPE has a melting point between 105°C and 115°C. This is quite low compared to other plastics; thus, it can withstand high temperatures without warping or melting.
LDPE performs well in heat resistance up to approximately 80°C for continuous use. The following are the relevant technical details that support this statement:
Melting Point: It typically varies from 105°C to 115°C, indicating at what temperature LDPE turns from solid to melted.
Continuous Use Temperature: It maintains effective operation up to nearly 80°C, showing its ability to work under different thermal environments without significant property loss.
Degradation Temperature: In applications requiring heat resistance, the mechanical properties of LDPE start declining continuously above 80oC.
Such parameters ensure that LDPE is still an appropriate choice for products that encounter thermal variations, justifying its use in many flexible packaging and heat-sensitive applications.
Thermal Conductivity and Insulation Properties
LDPE fiber performance is significantly influenced by its thermal conductivity, which has a great impact on its performance in many applications. Low thermal conductivity is observed in LDPE, with values ranging from 0.40 to 0.50 W/m·K. This renders it ideal for insulation, where it can effectively reduce heat transfer. These are the respective technical parameters that capture these attributes.
Thermal Conductivity: The range of 0.40 to 0.50 W/m·K shows that this material is as effective as insulators against heat pass-through, making low Thermal Conductivity an advantage in situations where heat retention or prevention is needed.
Thermal Resistance: It is essential for packaging and thermal barriers, as it helps resist heat flow through materials like LDPE due to its low thermal conductivity.
Applications: Therefore, it is commonly used in wire and cable coatings, where insulation properties are important, as well as durable and high-temperature-resistant packaging materials.
These properties make LDPE fiber dependable even when temperature changes or energy saving is a significant concern.
How Does LDPE Fibre Compare to Other Textile Fibres?
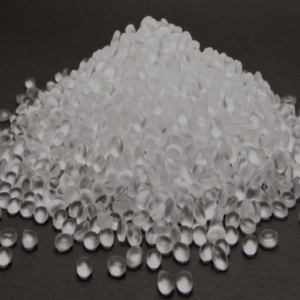
LDPE vs. HDPE: Key Differences
Several key differences ought to be considered when comparing low-density polyethylene (LDPE) and high-density polyethylene (HDPE).
Density and Structure: On the other hand, LDPE is less dense than HDPE, meaning that it is more flexible than rigid. This means that it can be used, for example, in plastic bags that need to have some stretch or durability. HDPE has a higher density, which makes it stronger and stiffer; thus, bottles and containers are made from it.
Molecular Arrangement: It also has a branched molecular structure, resulting in a low melting point of 105-115°C, hence its high flexibility compared with LDPE. Conversely, HDPE is linear, with a melting point of around 120-130°C, which gives it better impact and tensile strength.
Physical Properties:
- Tensile Strength: Whenever structural applications require more force, HDPE would be more appropriate since it generally possesses greater tensile strength than LDPE.
- Chemical Resistance: While both materials have good chemical resistance, HDPE performs better in harsher chemical environments.
These distinctions must be considered when choosing between LDPE and HDPE for specific applications, depending on the material properties required for optimal performance.
LDPE vs. Polypropylene (PP) Fibres
In comparing Low-Density Polyethylene (LDPE) with Polypropylene (PP) fibres, I have found that each has unique properties that make it suitable for different applications.
Density and Strength: LDPE is low in density and more flexible, so it can be used in areas such as plastic films and bags. Conversely, PP is high density and has excellent tensile strength. In most cases, the tensile strength of PP is around 30-40 MPa, whereas that of LDPE would be between 10-20 MPa, implying that it could be used for products requiring greater structural integrity.
Melt Flow Index (MFI): On average, the MFI for LDPE is higher than that of PP at around 1 to 7 g/10 min compared to 20 g/10 min respectively. This difference points out that LDPE is easily processable through faster production rates, while the lower MFI for PP guarantees its strength, making it applicable to containers and automotive parts.
Chemical Resistance: The two materials possess some chemical resistance; however, PP performs better than LPDE when exposed to high temperatures or solvents, hence its wide use in packaging and industrial applications.
In conclusion, whether to choose LDPE or PP fibers depends on the specific needs of the intended application, taking into consideration flexibility, strength, and processing capabilities.
LDPE vs. Natural Fibres
Regarding properties and applications, Low-Density Polyethylene (LDPE) varies distinctly from natural fibers like cotton and jute.
Biodegradability: Natural fibers are intrinsically biodegradable, breaking down naturally in the environment over time. In contrast, LDPE is a synthetic polymer that may take hundreds of years to decompose, thus raising concerns about its disposal in the environment. For example, cotton can decompose in about 3-5 months, while LDPE can persist for years without breaking down.
Tensile Strength: Compared to LDPE, natural fibers often have reduced tensile strength. For instance, cotton fibers have tensile strengths ranging between 20 and 40 MPa, whereas those of LDPE range from 10 to 20 MPa. This implies that while LDPE allows for greater flexibility and durability, natural fibers serve as suitable materials with enough strength for textiles and packaging.
Moisture Absorption: Since natural fibers are hydrophilic, they can absorb moisture, which is useful in some applications such as clothing and home textiles. On the other hand, being a hydrophobic material, LDPE does not absorb water, thus making it perfect for use in moisture-proof packaging materials.
Therefore, selecting either LDPE or natural fibers is determined by the specific requirements of the application, with environmental issues such as strength and resistance to moisture playing crucial roles in the decision-making process.
Frequently Asked Questions (FAQs)
Q: What is Textile Grade LDPE Fibre?
A: Textile-grade (Low-Density Polyethylene) LDPE Fibre is a flexible plastic fiber known for its strength and durability. It is found in various plastics, such as non-woven fabrics, ropes, and nets.
Q: How is LDPE Fibre used in composite materials?
A: LDPE Fiber is often utilized to manufacture composites because it possesses good chemical resistance and flexibility. By incorporating other materials into it, the properties of the composites are improved, resulting in their suitability for various plastic applications.
Q: What are the critical properties of LDPE Fibre?
A: Its ability to melt at low temperatures, weather stability, and chemical resistance make this product appropriate for numerous plastic applications, such as film or pipe manufacturing.
Q: How does LDPE Fibre differ from other polyolefin fibers?
A: In terms of density and elasticity, respectively, these other olefins, namely high-density polyethylene (HDPE) and ultra-high molecular weight polyethylene (UHMWPE), vary with LDPE Fiber. Compared to these other fibers, LDPE has lower density and more flexibility.
Q: What are the common uses of LDPE Fibre in textile applications?
A: Some typical uses of this material include fabricating non-woven textiles and ropes, nets, and filament yarns, among others. The processability, in conjunction with its flexibility, allows it to be used for many purposes where chemical use could be required.
Q: What is the significance of Goodfellow in LDPE Fibre research?
A: For many years, they have been providing information about polymers, including specifications on polymer characteristics. This helps manufacturers and researchers choose the correct materials based on their needs.
Q: How is LDPE Fibre manufactured?
A: Polymer melts down through extrusion, elongating into long chains or filaments. This process can be adjusted to produce fibers with specific properties, such as thickness and strength.
Q: What is the role of filament yarn in LDPE Fibre applications?
A: The quality of this filament yarn makes it suitable for use in various textile applications because it has a long life span and is highly flexible. In other words, ropes, nets, and non-woven fabrics are significant examples of where it is found.
Q: What are some challenges associated with LDPE Fibre?
A: For instance, its weakness compared to other polymers like UHMWPE and degradation when exposed to UV radiation, but its ability to chemically resist and its flexibility has contributed a lot to its use in many plastics.
Q: How does LDPE Fibre contribute to sustainability in textile applications?
A: Among them is the fact that this type of product can be recycled back into several other products. Longevity plus chemical resistance allow for an extended lifespan on LDPE-derived goods, thus reducing replacements.