Dyeing polyester yarn truly poses its own peculiar challenges and demands an exact technique to achieve the highest results. Polyester is a synthetic fiber, less hydrophilic than natural fibers, where traditional mechanisms of dyeing do not apply. But when done right, so with the right method, tools, and dyes, usually disperse dyes, the dyeing of polyester yarn can produce beautiful and permanent hues. The purpose of this book is to really unravel the process by providing extensive step-by-step directions from choosing the appropriate dye all the way to an even and consistent coloration. The knowledge contained therein, thus, can really help a textile professional or a DIYer master the proper dyeing of polyester yarn.
What is the Best Method for Dyeing Polyester Yarn?
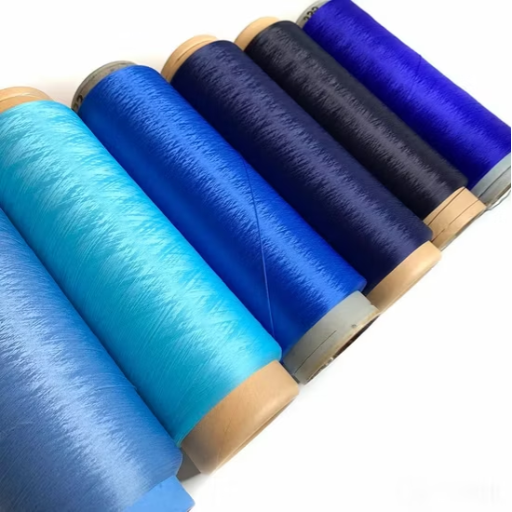
The most recommended way of dyeing polyester yarn is with disperse dyes through a high-temperature dyeing method. The process involves heating the polyester yarn in an aqueous solution to approximately 200°F (93°C) while adding disperse dye and a carrier chemical to promote penetration. The dye bonds with the synthetic fibers at a molecular level to yield bright and forever colors. The temperature and agitation should not drop for even dyeing. This method is widely considered to be the industry standard for polyester dyeing, due to its reliable and durable performance.
Understanding the Dyeing Process for Synthetic Fibers
Recently, the dyeing of synthetic fibers has been a field of much research, with the objective of enhancing process efficiency and quality while keeping the environment safe. One of the dyeing developments has been the introduction of low-temperature dyeing, where dyeing occurs below 200°F (93°C). Energy consumption is greatly minimized, all the while the dye-fiber bond is retained.
Another technology gaining prominence is supercritical carbon dioxide (CO₂) dyeing, which removes water entirely from the process. Dyes are dissolved into pressurized CO₂, which then carries the dye particles very well into polyester and other synthetic materials from the dyeing point of view. Thus, the supercritical CO₂ dyeing process conserves water and reduces chemical usage-furthering the sustainable manufacturing goals.
Further, the advancements in digital dyeing help control dye placement and depth at very slight tolerances, hence reducing waste and sharpening the design possibilities. These modern dyeing techniques along with continued research towards biodegradable carrying agents and environmentally friendly dye formulas should mark a major change in shifting the process towards greener and more efficient textile dyeing.
Dyeing Method for Polyester Yarn
- Pre-washing
Begin by pre-washing the polyester yarn with very mild detergent to remove any surface oils, any traces of dirt, or factory finishing that could hinder dyeing. Rinse very well and leave the yarn damp.
- Dye Bath Preparation
Pour in sufficient water into the stainless steel pot to cover the yarn entirely. Heat the water to maintain a temperature between 180°F and 200°F since polyester requires high heat for perfect dye absorption. Add the Rit Dyemore dye following the manufacturer’s directions for the amount of dye per weight of fabric to get the intensity of color desired. Stir the dye bath well to disperse the dye pigments evenly.
- Immersion and Agitation
Into the dye bath goes the damp polyester yarn. Agitate evenly for 30-60 minutes to ensure even coloration. Make use of the thermometer to maintain consistency in the water temperature throughout the process since the change in temperature would lead to uneven dyeing.
- Rinsing and Finishing
Is it Possible to Dye Polyester Fabric at Home?
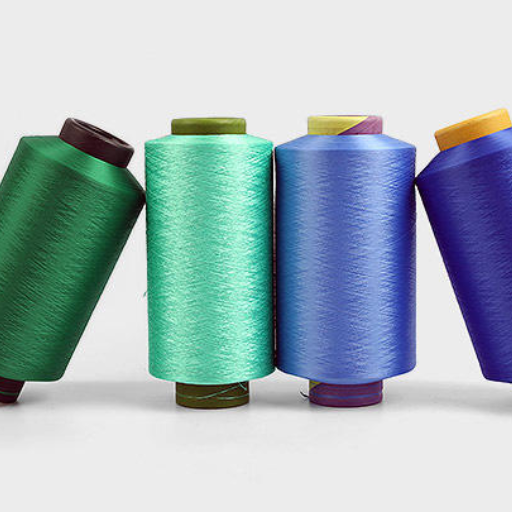
Undoubtedly, it is possible to dye polyester fabric at home, but some specific equipment and dyes are needed. Polyester is a man-made substance and is not readily absorbent to ordinary fabric dyes. One must have dispersed dye for the coloring purposes of synthetic fibers. The whole process involves heating the fabric and dye in regent water using high temperatures, about 200°F (93°C), to make the dye stick to the fibers. To this dyeing process and for the best results, it’s also important to anyways follow the instructions which come with the dye.
Step-by-Step Guide to Dyeing Polyester Fabric
- Prepare Your Workspace
Begin by establishing a well-lit and ventilated environment to avoid inhaling fumes. Have ready all materials, such as disperse dye, polyester fabrics, stainless steel pot/dyeing machine, measuring tools, gloves, and a stirring tool. Make sure that they are clean before use to not confuse or compromise the dyeing procedure.
- Wash the Polyester Fabric
Pre-washing fabric remains a necessary step for cleansing off any dirt, and oils, or factory finish that act as obstacles for uniform adhesion of the dye. Use mild detergent to wash and rinse thoroughly to keep the fabric clean for further steps of dyeing.
- Prepare the Dye Bath
In a big pot or dyeing machine, fill in water to permit movement of the fabric during the process and bring water to temperature of about 200°F (93°C). After the bath attains desired temperature, dissolve the disperse dye in little hot water before adding it to dye bath. To ensure even distribution of dye, stir the dye bath thoroughly.
- Add Fabric to the Dye Bath
Put the polyester fabric, prewashed, into the dye bath. Using a thermometer or controls on the dyeing machine, maintain an even temperature. Constantly stir the fabric to allow the dye to absorb evenly.
- Fix the Dye with Heat
The bonding of the dye with the synthetic fiber cannot take place without high temperature. The dyeing may last 30 minutes to 1 hour in the dye bath, according to the intensity of color needed. Stir occasionally to avoid uneven color or spotting.
- Rinse and Finish
After completing the process of dyeing, take out the fabric, and wash it with warm water, gradually moving to cold. This will clear most dye. The fabric is then gently washed with mild detergent to seal the color well and make it stable. Lastly, rinse once more.
- Dry the Fabric
Depending on care instructions, allow the fabric to dry well in the air or tumble dry at low heat. Do not dry the fabric in the sunlight lest the colors begin to fade.
Strict adherence to these steps will provide you with beautiful, permanent dyes for polyester with an impeccable finish.
Common Mistakes When Dyeing Polyester Yarn
- Using Incorrect Dye Types
In dyeing polyester, dyes intended for natural fibers such as cotton or wool are the first type of dyeing mistake. Polyester needs synthetic dyes, such as disperse dyes, which are specially made so that they may bond with the polymeric structure of the fiber. Using inappropriate dyes will lead to an unabsorbed dye, uneven coloring, or dye evaporation during washing.
- Neglecting Proper Heat Setting
Polyester fibers require high temperatures for dye molecules to be fixed effectively. Suppose these temperatures are omitted either during dyeing or after it. In that case, the colors may wear off poorly or superficially, so it is necessary to fix the colors by heating the dye bath correctly to 200°F (93°C) at the least.”
- Insufficient Preparation of the Yarn
One common mistake in dyeing is not cleaning the yarn well before dyeing. Polyester yarns generally contain processes oils, finishing, or residues, which can act as a barrier to the dyeing process. A thorough pre-wash procedure using a detergent designed to eliminate such impurities will give the results required for uniform and brilliant colors.
- Inaccurate Dye Measurements
Wrong estimation for any one dye quantity results in uneven operation or unpleasing shades. The exact amount should be measured for the weight of the yarn and dye manufacturer’s suggestions. Constant stirring and keeping the dye bath uniform are also critical to avoid blotches or streaks.
Why is Dyeing Polyester Yarn Difficult?
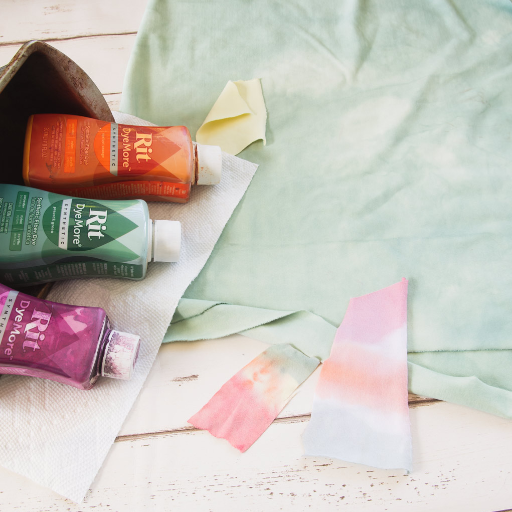
The dyeing of polyester yarns is a very difficult process due to the low absorbency ability of the material and the highly hydrophobic nature of the fiber. The synthetic polyester fibers being very tightly structured make it difficult for the dye molecules to penetrate the fiber and bind themselves adequately. Naturally, therefore, unlike those which dye their coloration by the use of disperse dyes and high heat processes, like boiling and pressure dyeing, they are best adapted to be dyed. Another important thing is uniform coloration, requiring careful temperature control and long processing time. An uneven distribution of heat at the surface could relatively cause uneven colouration, leading to patchiness and uneven tones. All these factors make the process of dyeing polyester a technically difficult one that requires specialized techniques and equipment for the same.
The Nature of Synthetic Fibers and Dye Absorption
Low absorption capacity and hydrophobic tendencies are characteristic of synthetic fibers like polyester, nylon, and acrylic, a major factor influencing their dye absorption behavior. The molecular construction of most of these fibers usually consists of tightly packed polymer chains, creating just limited opportunities for the dye molecules to penetrate the material. Thus, hydrophilic dispersing agents and carriers are generally introduced to assist with dye diffusion. Temperature, conversely, greatly influences as higher heat levels expand the polymer matrix of synthetic fibers, thereby raising their dye receptiveness. For instance, polyester needs to be dyed at temperatures exceeding 130 °C under pressurized conditions to gain perfect color uniformity. Besides, as the dye chemistry accelerated, providing cationic dyes for acrylic fibers, the affinity between synthetic materials and dyes is improved, thereby lessening the environmental impact. This growing domain provides continuous improvement to approaches that secure bright and durable coloration in synthetic textiles.
Compare the Different Type of Dye for Polyester
Type of Dye |
Key Features |
Suitable Use Cases |
Temperature Required |
Color Fastness |
---|---|---|---|---|
Disperse Dye |
Bonds with fabric at molecular level |
Polyester, blends with polyester content |
High (190-220°F / 88-104°C) |
Excellent (wash-resistant) |
Sublimation Dye |
Heat-transferred for vibrant colors |
Printing on polyester fabrics |
High (around 400°F / 204°C) |
Excellent (long-lasting) |
Rit DyeMore |
Accessible for home dyeing |
Polyester and nylon fabrics |
Medium-High (180°F / 82°C) |
Good (with care) |
Acid Dye |
Requires acidic environment to work |
Polyester-blended fabrics with wool/silk |
Medium (140-185°F / 60-85°C) |
Moderate (can fade) |
Fabric Paint or Spray |
Surface coloring only |
Polyester for customization/designs |
No heat required (drying) |
Varies (rub-resistant) |
Addressing Issues with Color Bleeding
Dye bleeding takes place when the dye utilized in fabric penetrates into the water or transfers to any other material that leads to discoloration or unwanted patterns. This problem mostly appears with polyester or synthetic blends where sometimes Type-D has a weaker adherence to them compared to natural fibers. Control measures should start by understanding the factors leading to dye instability, such as the temperature of the water, the pH value of the water, and the dye types used.
Apart from color bleeding, the fabric should always be pre-washed for at least half an hour in cold water before dyeing. This should conveniently get rid of any dirt, surface finish, or obnoxious loose dye particles that may affect future dyeing results. A fixative treatment matching the dye type should be applied, for example, Retayne for cotton-reactive dyes or an equivalent mordant for synthetic fabric. Afterward, always wash in cold water with a gentle detergent that helps retain the dye. Further, separate fabrics by colors and avoid adding outlandish mixes in the washer to reduce chances of dye transfer.
Heat setting the dye on polyester fabric is the most important step to secure adhesion and to avoid bleeding. Depending on the instructions for the particular dye product, you can consider steaming, ironing (with a press cloth), or simply baking the fabric. Avoiding any sort of bleeding on your dyed or painted pieces will preserve their essence for longer.
How to Use Disperse Dye for Polyester Yarn?
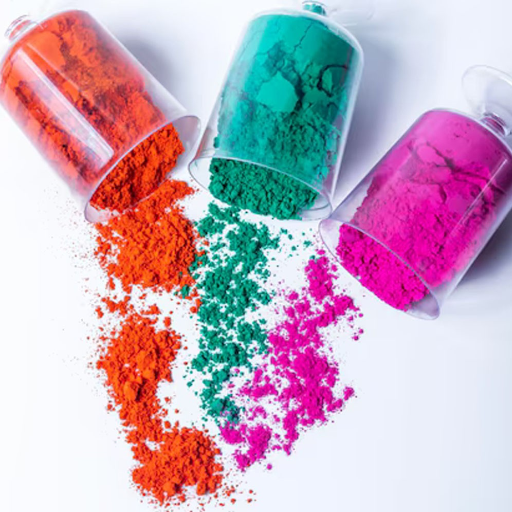
- Prepare the Yarn: The polyester yarn has to be cleaned from any dirt residues or finishes. One may wash it using mild detergent and then rinse it well.
- Create the Dye Bath: Disperse dye powder is dissolved in hot water as per the manufacturer’s instruction. A dispersing agent may be used for better dispersion of dye powder.
- Heat the Bath: Transfer the solution to a dye pot and then gradually heat it up to 200°F to 212°F (93°C to 100°C). It is at high temperatures that polyester can hold dye fast.
- Add the Yarn: Immerse the whole yarn in the dye bath.
- Set the Dye: Keeping the temperature during setting for 30-60 minutes, depending on how deep you want to do it. The commitment to using the thermometer all through ensures temperature consistency.
- Rinse and Dry: Then rinse the yarn with warm water until the water is clear; this will be the color you want. Finally, place the yarn for drying whenever it’s ready for application.
What is Disperse Dye and How Does it Work?
Disperse dye is a class of dyes that are considered non-ionic while being insoluble in water. Polyester fiber, acetate fiber, and nylon fiber are the primary fibers treated with disperse dyes. Dyes contain very finely ground particles. These particles are dispersed as a suspension in water during the dyeing process; when the particles of dye are soluble in water, these particles are called water-soluble dyes. Heat and pressure are applied for disperse dyes to soften dye molecules and insert them into the fibers, which are hydrophobic by nature.
The dyeing mechanism exploits thermal expansion of fibers. Upon heating, polymer chains in synthetic fiber relax slightly to form temporary spaces into which disperse dye molecules diffuse and interact with the fiber by Van der Waals force and hydrogen bonding. This bond retains color under conditions of washing and exposure to light.
Preparing Disperse Dye for Dyeing Polyester
The procedure for preparing disperse dye solutions comprises several exact steps that are intended to guarantee their value at the time of the dyeing process. First, it must be ensured that the disperse dye is effectively dispersed in water, usually with assistant dispersing agents such as lignin sulfonates or naphthalene sulfonates that keep in suspension the dye particles. These agents help to stabilize the suspension of the particles and prevent aggregation.
After dispersing, pH adjustment ergo swelling is carried out in such a way that the dye solution pH is kept to an optimum pH of 4.5-5.5. This pH adjustment will guarantee compatibility with the polyester fiber and prevent hydrolysis of the dye. The solution is then diluted to a concentration considering constant coloration of textile batches.
How Much Dye Do I Need for Polyester Fabric?
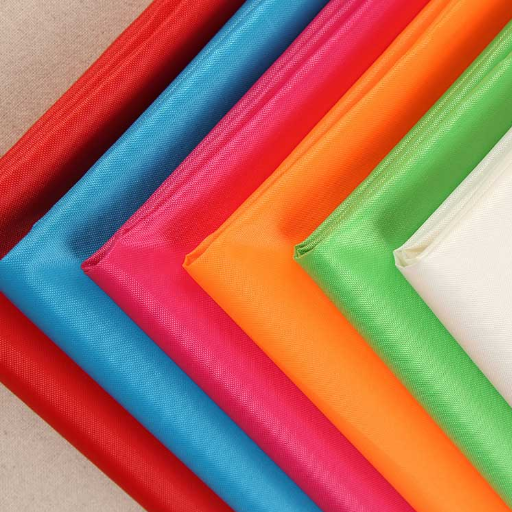
Based on the weight of the fabric and the color intensity required, the quantity of dye for polyester fabric is determined. As a rule of thumb, 1-2% dye weight of fabric (OWF) is used. For instance, if you dye 500 grams of polyester fabric, then the dye needed for a medium to deep shade would be 5-10 grams. For lighter shades, a lesser quantity would be sufficient, while for darker and brighter shades, a slight increase in dye quantity can be absorbed. It is always better to follow the instructions given by the dye manufacturer since every manufacturer might endorse a different quantity depending on the kind of dye used and its formulation.
Determining the Amount of Dye per Pound of Fabric
Also, certain fabrics, such as cotton, may absorb the dyes in a different manner from artificial wool, thus affecting the percentage of OWF required. Consulting technical specifications about saturation limits for the dye type under consideration assures perfect color reproduction. Also, consider environmental elements like bath pH and dyeing temperature affect the uptake of the dye, stressing the complexity of the procedure for uniform coloration. Always cross-reference dye manufacturers’ usage charts for the most precise information tailored to your materials.
Adjusting Dye Quantities for Desired Color Depth
Reference Sources
-
“Review on Intermolecular Forces between Dyes Used for Polyester Dyeing and Polyester Fiber” (2020): This study explores the interactions between disperse dyes and polyester fibers, emphasizing hydrogen bonds, van der Waals forces, and dipole-dipole interactions.
-
“Disperse dyes, temperature and yarn parameters’ effect on microfibre shedding of polyester spun yarn”: This study identifies microfibre (MF) shedding as a significant environmental concern during polyester yarn dyeing. It finds that long-staple, fine yarns dyed at lower temperatures release fewer microfibres compared to coarser yarns dyed at high temperatures. The study also highlights the inefficiency of current wastewater treatment plants in removing microplastics.
Frequently Asked Questions (FAQs)
Q: Why is polyester considered difficult to dye?
A: Polyester is a synthetic fabric that is difficult to dye because it does not absorb dye as easily as natural fibers. This characteristic requires specific dyeing methods and materials, such as polyester with disperse dye, to achieve vibrant colors.
Q: Can I use a washing machine to dye 100% polyester?
A: Yes, you can use a washing machine to dye 100% polyester, but you need to ensure you are using the right dye, such as disperse dye, and follow the proper instructions to achieve the desired dye color.
Q: How do I determine how much dye I need to dye polyester?
A: To determine how much dye you need, you should consider the weight of the polyester item you want to dye. Generally, dye brands suggest using enough dye to dye up to two pounds of fabric, and you may need to adjust based on the dye color and intensity you desire.
Q: What should I do if I notice excess dye on my polyester fabric after dyeing?
A: If you notice excess dye, you can use a dye carrier solution or rinse the fabric with cold water to remove excess dye. Additionally, washing the item with a mild detergent can help remove any remaining excess dye.
Q: What kind of dye is best for dyeing polyester?
A: The best dye for dyeing polyester is disperse dye, which is specifically formulated to adhere to synthetic fabrics like polyester. Reactive dye is not suitable for polyester as it is designed for natural fibers.
Q: Can I dye a polyester cotton blend fabric the same way as 100% polyester?
A: Dyeing a polyester cotton blend requires special consideration, as the cotton part will absorb dye differently than the polyester. You may achieve varied results, so be sure to use dye that works effectively on both fibers, typically a disperse dye for polyester and a suitable dye for cotton.
Q: How do I submerge the fabric into the dye correctly?
A: To properly submerge the fabric into the dye, fill a container with hot water and your chosen polyester dye. Stir the mixture well, then add the fabric slowly to ensure even coverage and prevent clumping. Make sure the fabric is fully submerged for best results.
Q: Is it possible to remove dye from polyester items?
A: Yes, it is possible to remove dye from polyester items using products like Rit Color Remover. However, the effectiveness may vary, and complete removal may not always be achievable. It’s best to test on a small area first.
Q: What temperature is recommended for dyeing polyester?
A: Dyeing polyester typically requires high temperatures, usually between 190°F to 212°F (88°C to 100°C), depending on the dye being used. Make sure to follow the dye brand instructions to achieve the best results.